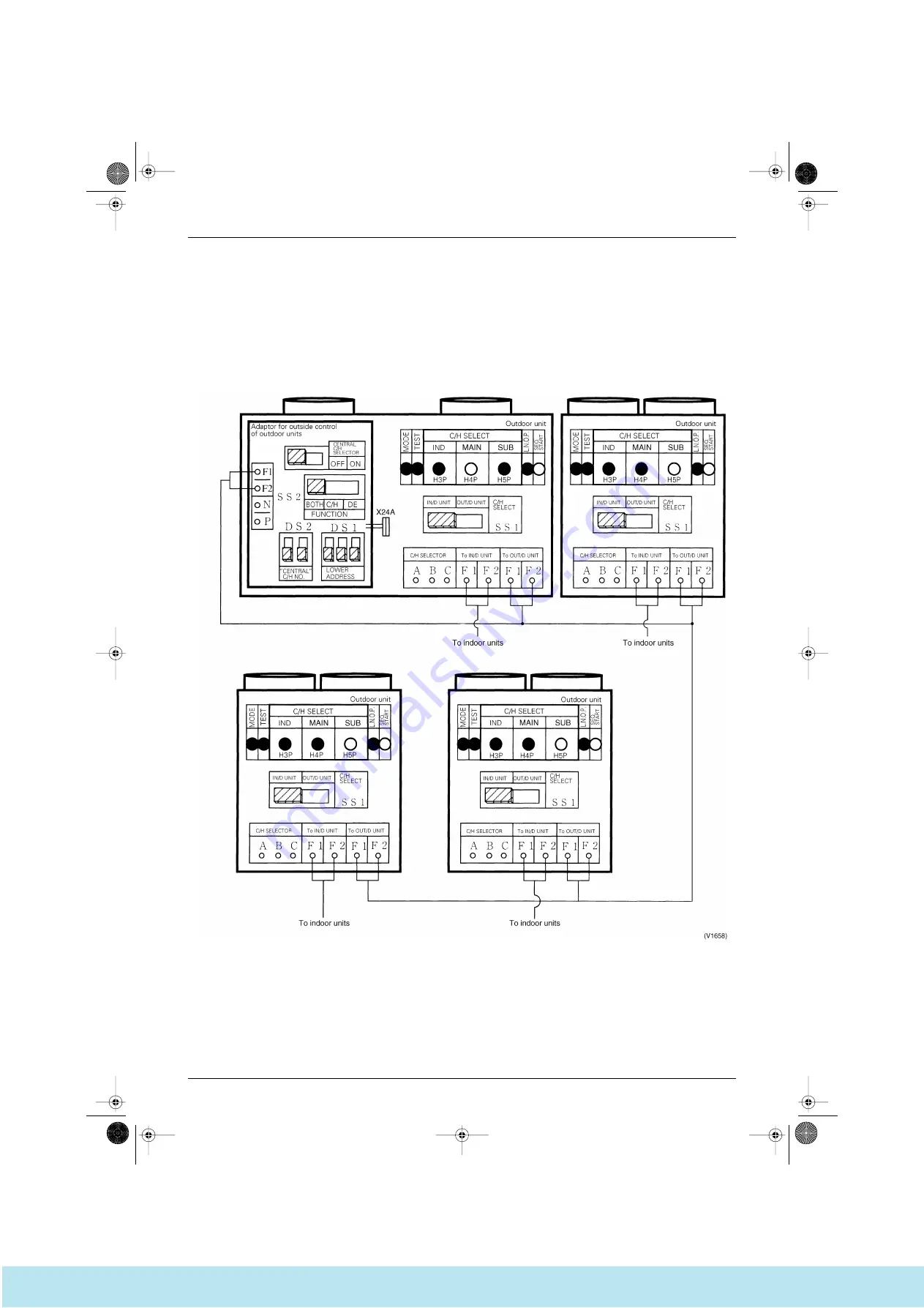
Test Operation
SiE33-102
74
General Information
4.5.3
Setting of Cool / Heat by Outdoor Unit System Group in Accordance with Group Main
Outdoor Unit by Indoor Unit Remote Control
Install the External control adaptor for outdoor unit on either the outdoor - outdoor, indoor - outdoor, or
indoor - indoor transmission line.
Set SS1 of the outdoor unit PCB to “IN / D UNIT” (factory set).
In setting mode 1, set the outdoor unit you want to give cool/heat selection permission to as the group
main, and set the other outdoor units as group sub units.
Set SS1 of the External control adaptor for outdoor unit to “BOTH” (factory set) or “C / H.” Set SS2 to
“OFF” (factory set).
4.5.4
Setting of Cool / Heat by Outdoor Unit System Group in Accordance with Group Main
Outdoor Unit by Cool/Heat Selector
In addition to 1.5.3, change the following:
Install a cool / heat selector to the group main outdoor unit.
Set SS1 of the group main outdoor unit’s PCB to “OUT / D UNIT.”
Si33-102.book Page 74 Tuesday, June 26, 2001 3:18 PM
Все каталоги и инструкции здесь:
http
:
//splitoff.ru/tehn-doc.html