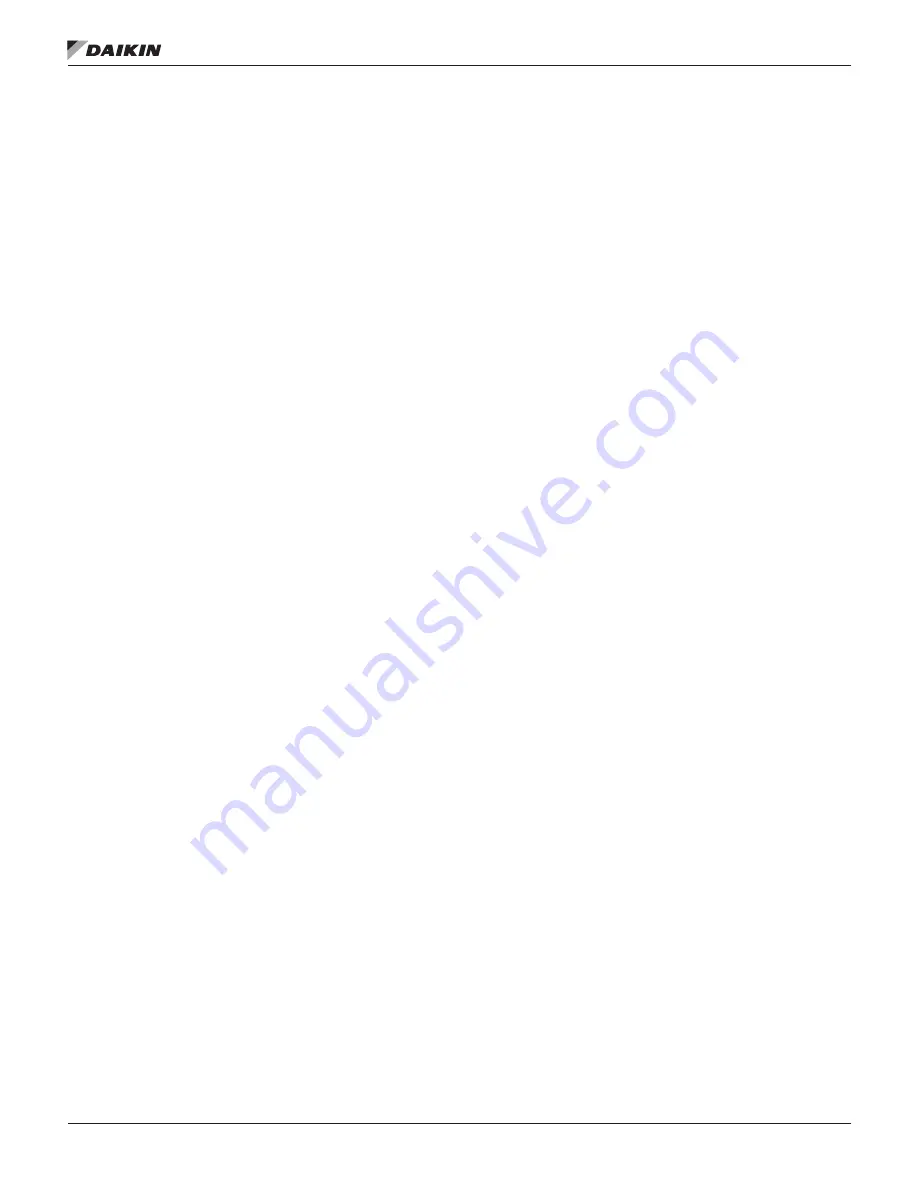
IOM 1281-2 • CENTRIFUGAL WATER CHILLERS 12 www.DaikinApplied.com
Installation
Cooling Tower Control
Control of the cooling tower is required to maintain stability and
avoid operational issues. This can be achieved through a BAS
or by using the MicroTech
®
II controller. For systems utilizing a
common condenser water loop for multiple purposes, the BAS
contractor must provide the control but use of the MicroTech®
output signal is still recommended.
The preferred cooling tower control utilizes a variable speed
fan. MicroTech® II will provide a control signal to determine the
proper fan speed. It can also control up to three stages of fan
cycling. Note that fan cycling can cause cooling tower water
temperature to fluctuate as fans stage on/off, potentially adding
instability to the system.
Special consideration must be given to starting the chiller when
cold condenser water is present, such as with inverted starts
or changeover from free (tower) cooling to mechanical cooling.
Daikin Applied chillers will start with entering condenser water
temperature as low as 55°F (42.8° C) providing the chilled
water temperature is below the condenser water temperature.
The minimum entering condenser water temperature while
operating is a funcion of the leaving chilled water temperature
and load. It is required that some method be used to control
the condenser water to maintain proper head pressure as
indicated by the MicroTech
®
II controller. Refer to
“Tower
Control Settings” on page 50
for control strategy details in
the HMI.
Each of the following acceptable methods can be controlled by
the MicroTech® II or through a BAS utilizing the MicroTech®
output signals:
1. Three-Way Bypass Valve Operation. A traditional method
for building condenser pressure at startup with colder
condenser water is with the use of a three-way bypass
valve. The device blends warmer water leaving the
condenser with cooler water from the cooling tower at the
condenser inlet. The bypass valve position will change
until full flow from the tower to the condenser is obtained.
The MicroTech
®
II provides only the valve position control
signal. Main power to drive the valve’s actuator must be
provided by the installer. The three-way valve should be
located close to the chiller within the equipment room to
minimize the volume of water.
2. Two-Way Valve Operation
Another condenser control method is to use a modulating
two-way control valve located on the outlet connection of
the condenser. The valve will be nearly closed at startup
to restrict water flow, which keeps generated heat in
the condenser until an acceptable minimum condenser
pressure is reached. As heat builds, the valve will open
slowly until a full flow condition from the cooling tower
is established. A separate power source is required to
provide power to the valve actuator.
NOTE:
To ensure proper operation, caution should be
used when utilizing the two-way valve option.
3. VFD Operating with a Condenser Water Pump
A third method of condenser control for startup is
utilizing a variable frequency drive with the condenser
water pump. The speed will change as directed by the
MicroTech® II output signal until design flow is reached.
Speed adjustments may be required during the initial
chiller startup as determined by the service technician.
NOTE:
Not using the MicroTech® II logic to control valves
and variable frequency drives may result in system
instability, capacity reduction, and issues starting the
chiller with cold condenser water temperature.
Condenser Pump Sequencing
It is recommended to utilize the logic built into the MicroTech
®
II controller to start the condenser pump. MicroTech
®
II has the
capability to operate a primary pump and a secondary standby
pump. The condenser water flow should be stopped when
the chiller shuts off. This will conserve energy and prevent
refrigerant from migrating to the condenser. Moisture in the
air can condenser on the cooler surfaces of the un-insulated
condenser barrel if flow is present when the chiller is idle.
Water Side Economizer Cycle
Operation
Water side economizers are commonly used for ASHRAE 90.1
compliance and energy savings. This system utilizes a heat
exchanger external to the chiller when cold cooling tower water
is available to provide cooling. The most common system
has a heat exchanger used in conjunction with the chiller’s
evaporator.
The BAS contractor will need to provide controls for the heat
exchanger including isolation valves and temperature control.
The BAS contractor will also need to control the isolation
valves for the chiller. It is important to use slow-acting type
valves to prevent rapid changes in system flows. Changeover
from economizer cooling to mechanical cooling requires one
of the methods previously mentioned to maintain suitable
condenser head pressure.
Contact your local Daikin Applied representative for more
information on this application.