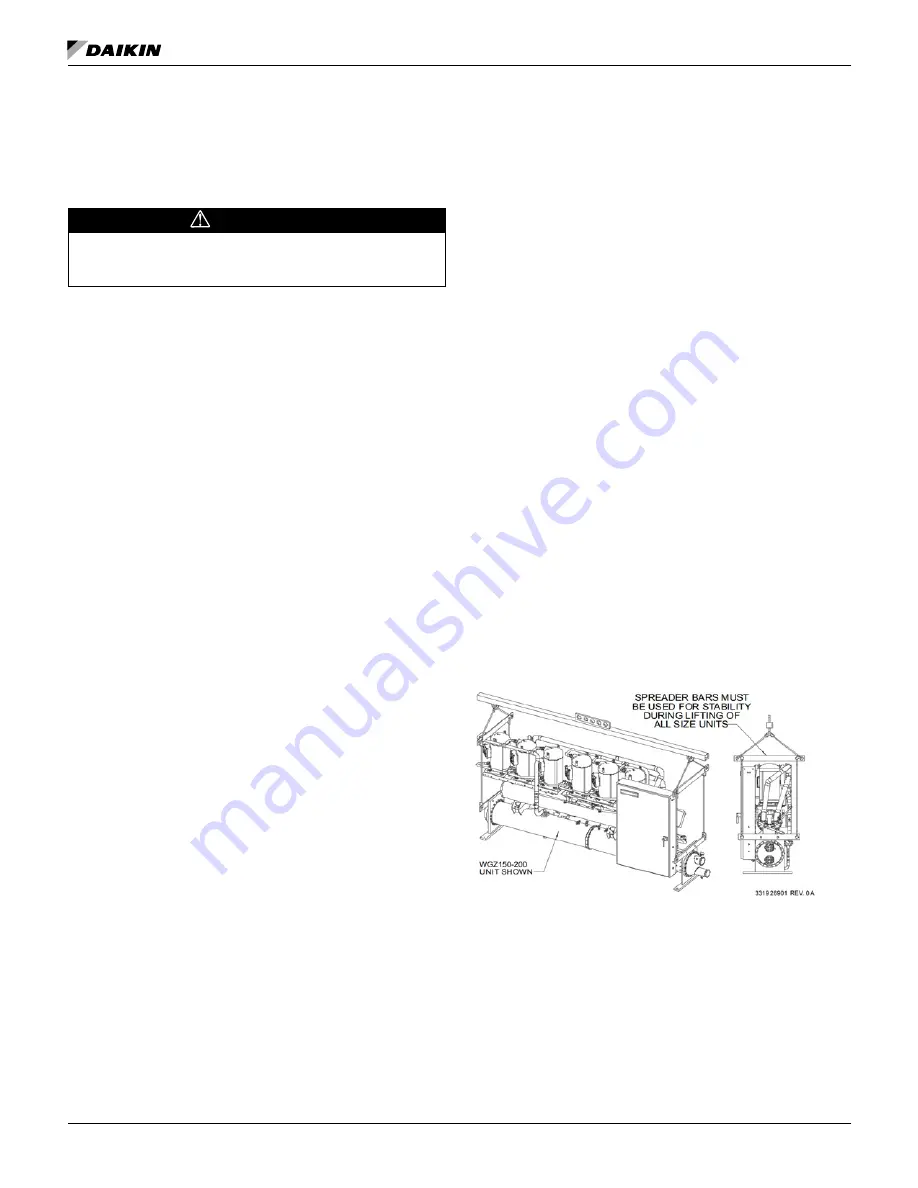
www.DaikinApplied.com
7
IOM 1322 • WATER-COOLED SCROLL COMPRESSOR
Installation
NOTE:
Installation and maintenance are to be performed
only by qualified personnel who are familiar with local
codes and regulations, and experienced with this type
of equipment.
CAUTION
When around sharp edges, wear appropriate Personal Protective Equipment
(PPE), such as gloves, protective clothing, foot wear, eye protection etc. to
prevent personal injury.
Location
WGZ chillers are intended only for installation in an indoor or
weather protected area consistent with the NEMA 1 rating on
the chiller, controls, and electrical panels. Equipment room
temperature for operating and standby conditions is 40°F to
122°F (4.4°C to 50°C).
Because of the electrical control devices, the units should not
be exposed to the weather. A plastic cover over the control
box is supplied as temporary protection during shipment. A
reasonably level and sufficiently strong floor is required for
the water chiller. If necessary, additional structural members
should be provided to transfer the weight of the unit to the
nearest beams
Space Requirements for Connections
and Servicing
For brazed plate evaporators - the chilled water and condenser
water (on units with a water-cooled condenser) piping enters
and leaves the unit from the right side when looking at the
control panel. Left-hand condenser connections are an option.
For shell and tube evaporators, the water connections are on
the back side of the unit. A clearance of at least 3 feet (1219
mm), or more if codes require, should be provided beyond this
piping and on all other sides and ends of the unit for general
servicing or for changing the compressors, if it ever becomes
necessary. Allow a minimum of 4-ft clearance in front of the
control panel or as required by NEC or local codes.
On units equipped with a water-cooled condenser (Type
WGZDW) clearance should also be provided for cleaning
or removal of condenser tubes on one end of the unit. The
clearance for cleaning depends on the type of apparatus
used, but can be as much as the length of the condenser (10
feet, 3050 mm). Tube replacement requires the length of the
condenser (as much as 12 feet) plus three feet of workspace.
This space can be provided via a doorway or other opening.
Moving the Unit
Refer to Lifting/Mounting weights beginning on
The packaged unit skid option is strongly recommended for
ease of handling and to help prevent damage if a crane is not
available for rigging at site. Properly designed field supplied
skids or dollies are acceptable. Do not push unit along a
floor without them. The condenserless models (AGZ-DA) are
manufactured with a base suitable for moving with rollers.
All moving and handling of packaged units (
) must be performed with skids or dollies under the unit and
they should not be removed until the unit is in the final location.
Never put the weight of the unit against the control box.
In moving, always apply pressure to the base on the skids only
and not to the piping or other components. A long bar will help
move the unit. Avoid dropping the unit at the end of the roll.
If the unit must be hoisted, lift the unit from the removable
lifting arms factory-bolted to each end of the unit adjacent
to the tube sheet by attaching cables or chains to the end of
the arms. A spreader bar must be used to protect the piping,
control panel and other areas of the chiller (
). The lifting arms should be removed after use.
Do not attach slings to piping or equipment. Do not attempt
to lift the unit by lifting points mounted on the compressors.
They are for lifting only the compressor should one need to
be removed from the unit. Move unit in the upright horizontal
position at all times. Set unit down gently when lowering from
the truck or rollers. Improper rigging, lifting, or moving of a unit
can result in property damage, severe personal injury or death.
Follow rigging and moving instructions carefully. Do not stand
beneath the unit while it is lifted or being installed.
Figure 1: Lifting the Unit
Introduction and Installation
Summary of Contents for WGZ030DA
Page 4: ......
Page 75: ...Unit Controller Operation www DaikinApplied com 75 IOM 1322 WATER COOLED SCROLL COMPRESSOR ...
Page 76: ...IOM 1322 WATER COOLED SCROLL COMPRESSOR 76 www DaikinApplied com Unit Controller Operation ...
Page 103: ... www DaikinApplied com 103 IOM 1322 WATER COOLED SCROLL COMPRESSOR Maintenance Schedule ...
Page 104: ...IOM 1322 WATER COOLED SCROLL COMPRESSOR 104 www DaikinApplied com Troubleshooting Chart ...
Page 111: ... www DaikinApplied com 111 IOM 1322 WATER COOLED SCROLL COMPRESSOR Limited Product Warranty ...