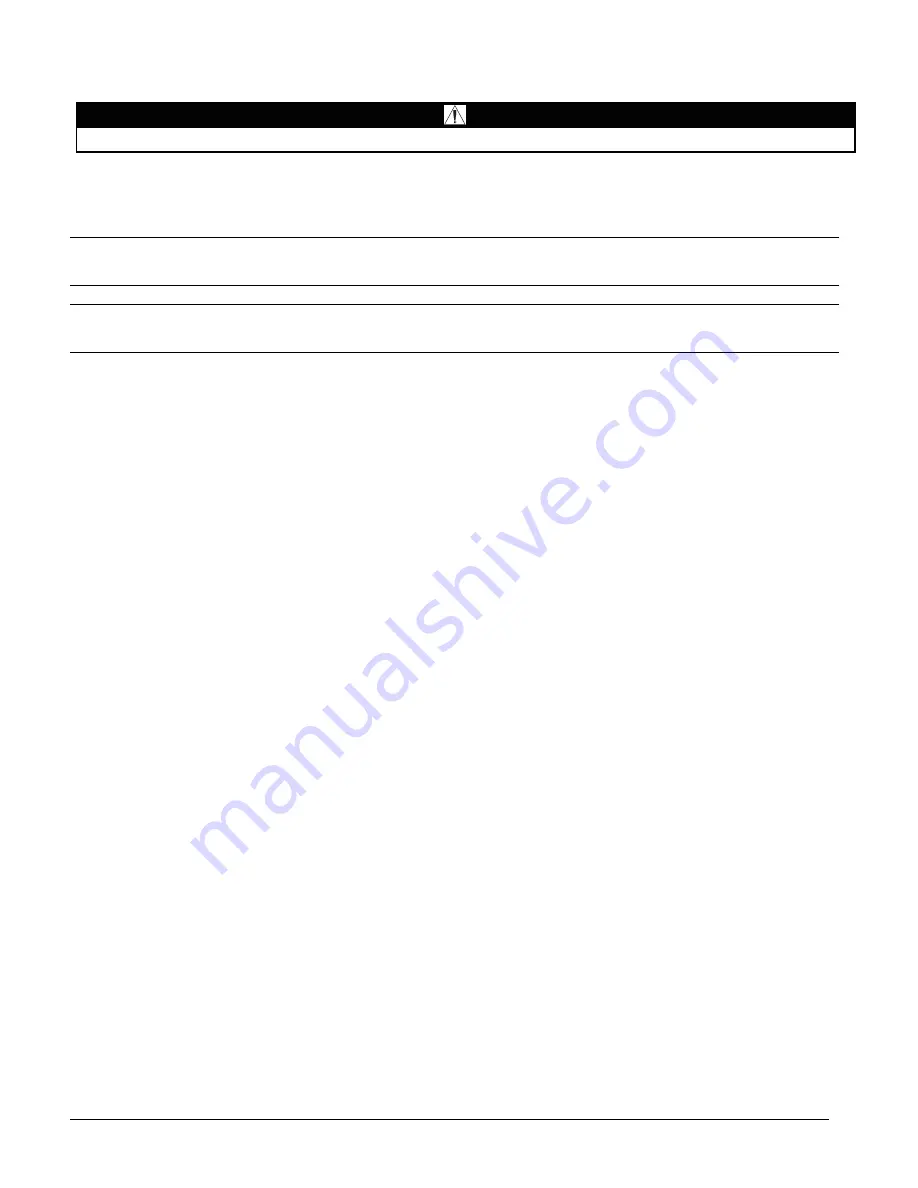
24
Centrifugal Chillers
IM 1044-2
The start-up technician will determine the phase sequence.
CAUTION
Connections to terminals must be made with copper lugs and copper wire.
Care must be taken when attaching leads to compressor terminals.
Use only copper supply wires with ampacity based on 75°C conductor rating. (Exception: for equipment rated over
2000 volts, 90°C or 105°C rated conductors should be used).
Note
: For installing remote-mounted, free-standing starters see
Daikin
manual IOMM 1158; for VFDs see
Daikin
manual IOMM 1159.
Note
: Do not make final connections to motor terminals until wiring has been checked and approved by a
Daikin
technician.
Under no circumstances should a compressor be brought up to speed unless proper sequence and rotation have
been established. Serious damage can result if the compressor starts in the wrong direction. Such damage is not
covered by product warranty.
600 +Volts Motor Insulation
It is the installing contractor's responsibility to insulate the compressor motor terminals when the unit voltage is
600 volts or greater. This is to be done after the
Daikin
start-up technician has checked for proper phase
sequence and motor rotation. Following this verification by the
Daikin
technician, the contractor should obtain
and apply the following items on medium voltage (above 600 volts) applications.
Materials required:
1. Loctite
brand safety solvent (12 oz. package available as
Daikin
part number 350A263H72)
2. 3M
Co. Scotchfil™ brand electrical insulation putty (available in a 60-inch roll as
Daikin
part number
350A263H81)
3. 3M Co. Scotchkote
brand electrical coating (available in a 15 oz. can with brush as
Daikin
Part Number
350A263H16)
4. Vinyl plastic electrical tape
The above items are available at most electrical supply outlets.
Application procedure:
1) Disconnect and lock out the power source to the compressor motor.
2) Using the safety solvent, clean the motor terminals, motor barrel adjacent to the terminals, lead lugs, and
electrical cables within the terminal 4OX to remove all dirt, grime, moisture and oil.
3) Wrap the terminal with Scotchfil putty, filling in all irregularities. The final result should be smooth and
cylindrical.
4) Doing one terminal at a time, brush the Scotchkote coating on the motor barrel to a distance of up to '/2"
around the terminal and on the wrapped terminal, the rubber insulation next to the terminal, and the lug and
cable for approximately 10". Wrap additional Scotchfil insulation over the Scotchkote coating.
5) Tape the entire wrapped length with electrical tape to form a protective jacket.
6) Finally, brush on one more coat of Scotchkote coating to provide an extra moisture barrier.