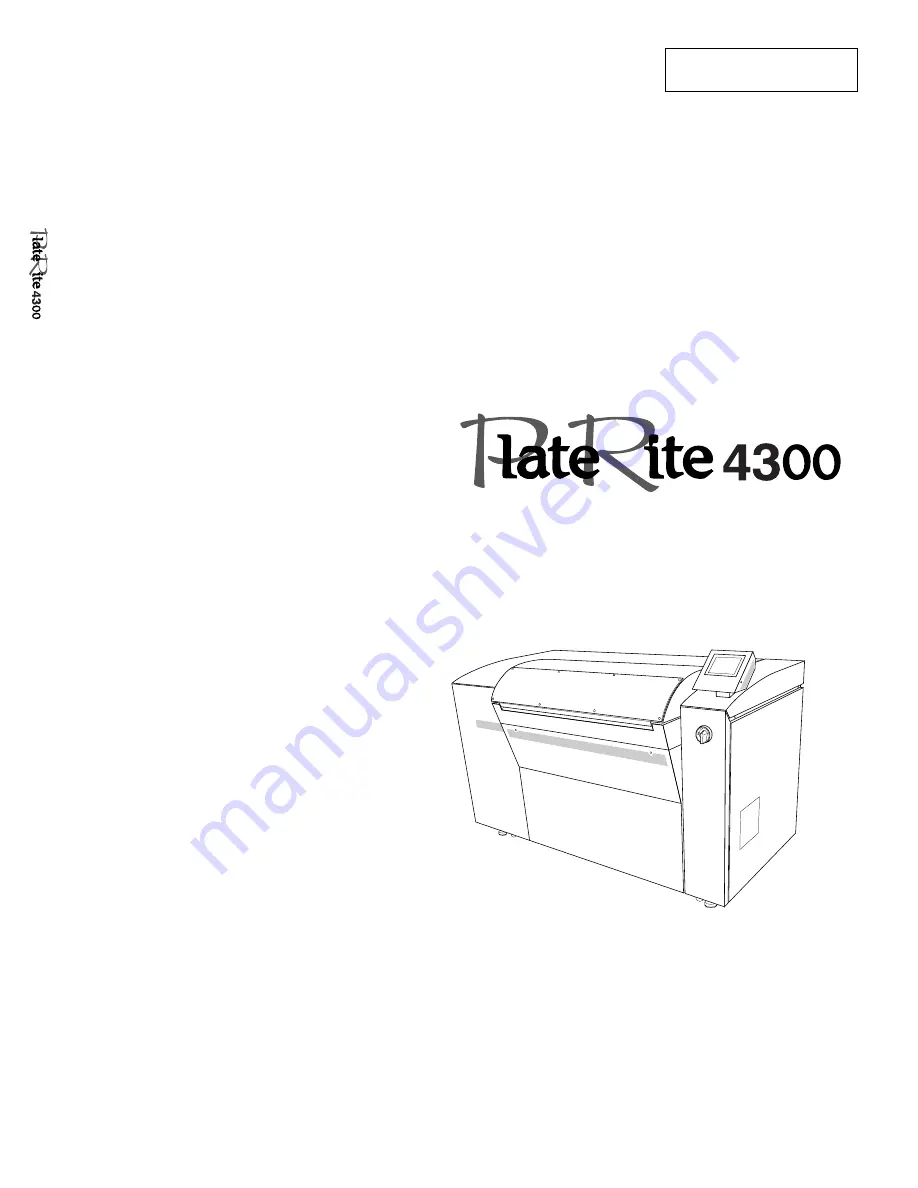
For operators (including
the machine administrator)
No. 100027907V00
PT-R4300
Ver. 1.0-
Thermal Plate Recorder
USERS MANUAL
Before attempting to operate this product, you should thoroughly read and fully
understand the contents of this manual.
The administrators of the PT-R4300 should not let anyone who does not
understand the contents of this manual operate or inspect the PT-R4300.
Thermal Plate Recorder Ver. 1.0-
USERS MANU
AL
• Printed on recycled paper.
Summary of Contents for PLATE RITE 4300
Page 10: ...x...
Page 11: ...Chapter 1 Ensuring Safety 1 This chapter gives information necessary for safe use of the PT R...
Page 26: ...PT R4300 USERS MANUAL 1 16 End of Chapter 1...
Page 38: ...PT R4300 USERS MANUAL 3 8 End of Chapter 3...
Page 39: ...This chapter explains the basic procedures for operating the PT R Chapter 4 Basic Operation 4...
Page 60: ...PT R4300 USERS MANUAL 4 22 End of Chapter 4...
Page 61: ...This chapter explains the procedures for setting PT R parameters Chapter 5 User Menu 5...
Page 122: ...PT R4300 USERS MANUAL 5 62 End of Chapter 5...
Page 157: ...This chapter explains this typical PT R problem and the solutions Chapter 8 Jamming 8...
Page 163: ...This chapter gives technical information on the PT R Chapter 9 Technical Information 9...