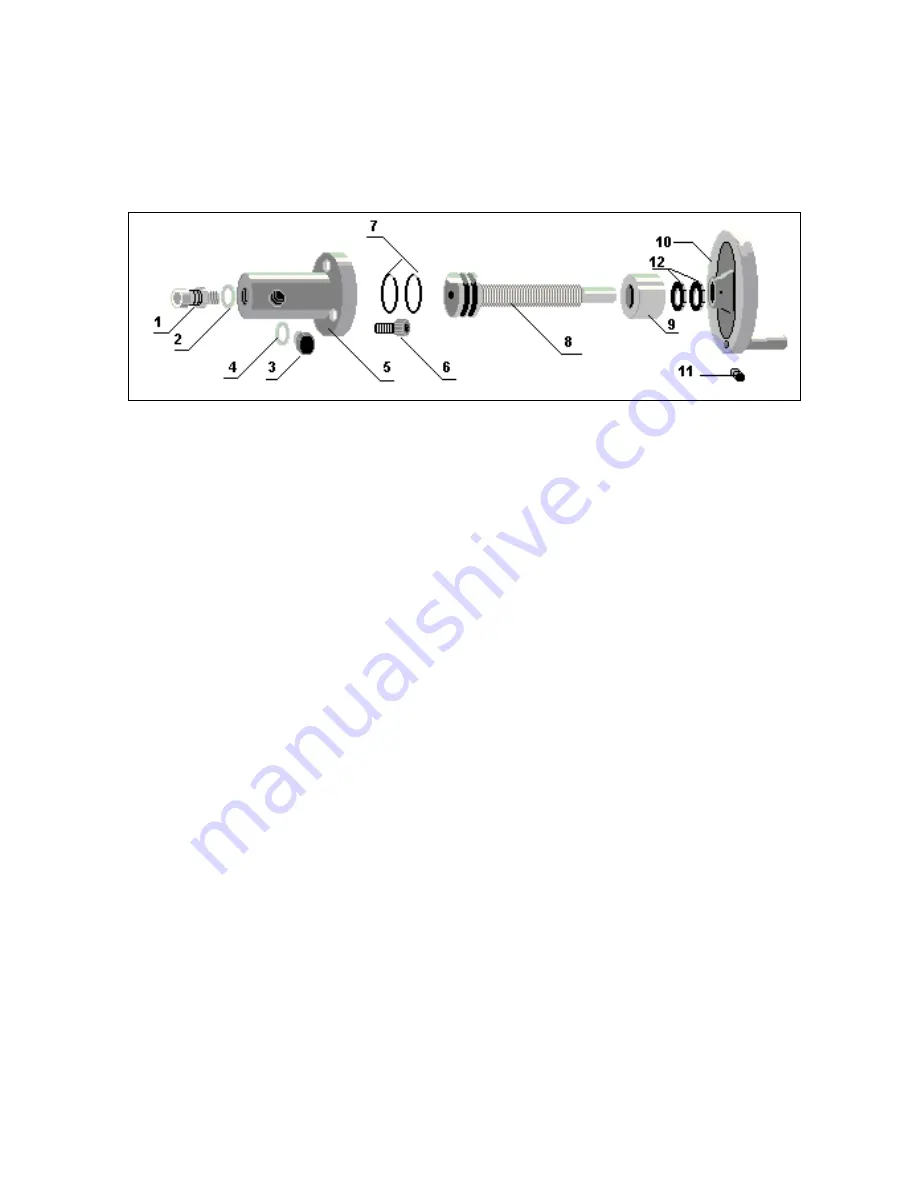
4/29/03
Manual V-16, V-24, VH-24, V-40 & VH-40
8 – Section I
FILLING THE SPEED REGULATOR
1. Turn the saw on.
2. Screw the handwheel in.
3. Turn the saw off once handwheel is in.
4. Remove the mounting screws (item 6).
5. Remove the plug from the cylinder (Item 3).
6. Turn screw out.
7. Add oil (Lightweight hydraulic oil) slowly while turning the wheel out.
8. When it is completely full, replace the plug (Item 3).
9. Re-mount the cylinder to the saw body.
10. Turn on the saw and adjust to the desired speed.
11. When saw is at maximum RPM, re-adjust the lock nuts on Item 8
MACHINE OPERATION
Prior to performing any cutting with the machine, it is recommended that the personal become
familiar with the various controls and accessories.
PRECAUTIONS
•
No loose clothing.
•
Eye protection should be worn.
•
All guards must be in position.
•
Table is secured in place and locked. Table load capacity should be noted and not exceeded.
•
Extra supports may be required for large or cumbersome components.
•
Irregular shapes and small objects should be secured by means of a clamp or suitable fixture.
•
Machine and surrounding should be kept free of tools, scrap and foreign objects.
•
Machine should be locked out before making any adjustments.
•
Care in uncoiling, and coiling and installation of blades should be observed. Gloves recommended.
•
Storage of blades in an area near the machine will allow operating personal, to use the proper
blade for each operation.
•
Machine is furnished with electrical door interlocks. These interlocks should periodically be checked
for proper operation.