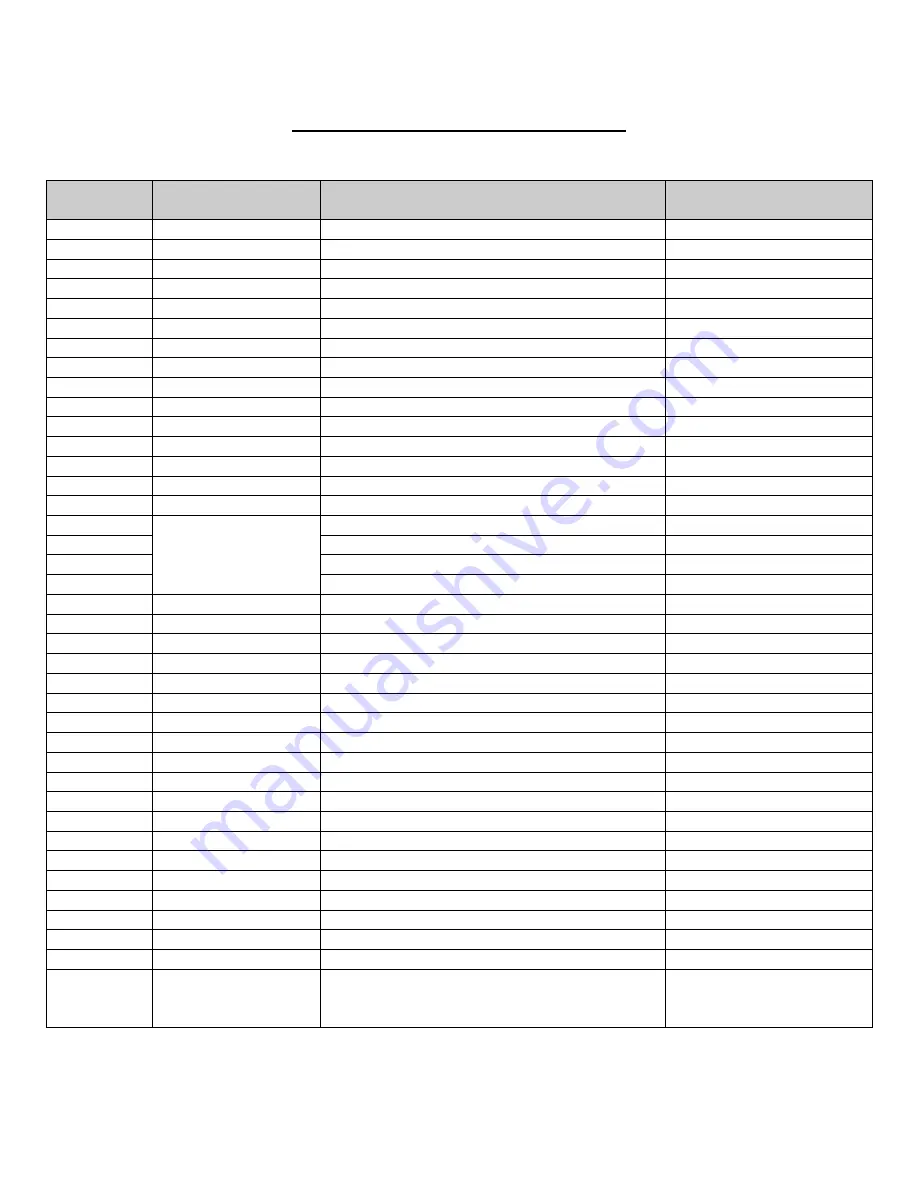
10/2/2019
Euromatic 370
3
Head Cylinder Unit
(Ref .005)
Pos.
Number
Part No.
Description
Specification
101
Gasket
TDUO 80 (CORTECO)
*102
Nut
M12
103
Cylinder Head
104
Tank Head
105
Plug ¼ gas
106
11558
Gasket
– 2 pieces
OR 4212
107
300273
Transparent Pipe
108
Tank Bottom
109
Pipe
80-86
110
Chromium Plated Rod
111
Gasket
NI 150/22
112
Gasket
– 2 Pieces
OR 4287
113
Central Head
114
Gasket
N 118086
115
Gasket
OR 147
*116
302164
Washer
*117
Bush
*118
Small Piston
*119
Ring Seeger
28
120
Pipe
50-56
121
Gasket
OR 147
122
Gasket
N 118086
123
Scraper Ring
WRM 086118
124
Brake Head
125
Chromium Plated Head
126
Filter 1/8 Gas
127
Gasket
OR 147
128
Gasket
OR 3087
129
Flange
130
Panel
131
Gasket
OR 3068
132
Adjusting Shaft
133
Gasket
OR 2106
134
Hexagon
135
Bottom
136
Pressure Gauges
300155
Cylinder Repair kit
301332
Cylinder complete
Kit
300155
Cylinder repair kit items 101, 106, 111, 112,
114, 115, 121, 122, 123, 126, 127, 128, 131,
133
Summary of Contents for Euromatic 370 PP
Page 9: ...370 S 370 S L 370 PP 370 PP L 9 ...
Page 10: ...370 S 370 S L 370 PP 370 PP L 10 Actual control panel layout may vari ...
Page 32: ...370 S 370 S L 370 PP 370 PP L 32 ...
Page 33: ...370 S 370 S L 370 PP 370 PP L 33 ...
Page 38: ...ALIMENTAZIONE 230V 60Hz 230V 60Hz POWER SUPPLY POWER SUPPLY ...
Page 39: ...HL4 ILLUMINAZIONE LAMA POWER SUPPLY ...
Page 40: ...LAMPEGGIATORE LAMA IN MOTO 24VAC MORSA 24VAC EMERGENCIES ...
Page 44: ...9 11 2 4 5 10 3 6 7 8 1 CH1 LC4HR424ACJ KA5 RITORNO CARRO COUNTER ...
Page 45: ...TERMINAL ...
Page 49: ...10 2 2019 Euromatic 370 2 Head Cylinder Unit Ref 005 ...
Page 51: ...10 2 2019 Euromatic 370 4 Bedplate Unit Ref 008 ...
Page 53: ...10 2 2019 Euromatic 370 6 Head Unit Ref 002 ...
Page 55: ...10 2 2019 Euromatic 370 8 Vise Unit Ref 004 ...
Page 57: ...10 2 2019 Euromatic 370 10 Group Feeder P R ...
Page 59: ...10 2 2019 Euromatic 370 12 Group Alimentador P P Ref 014b Alimentador Ref 014b ...