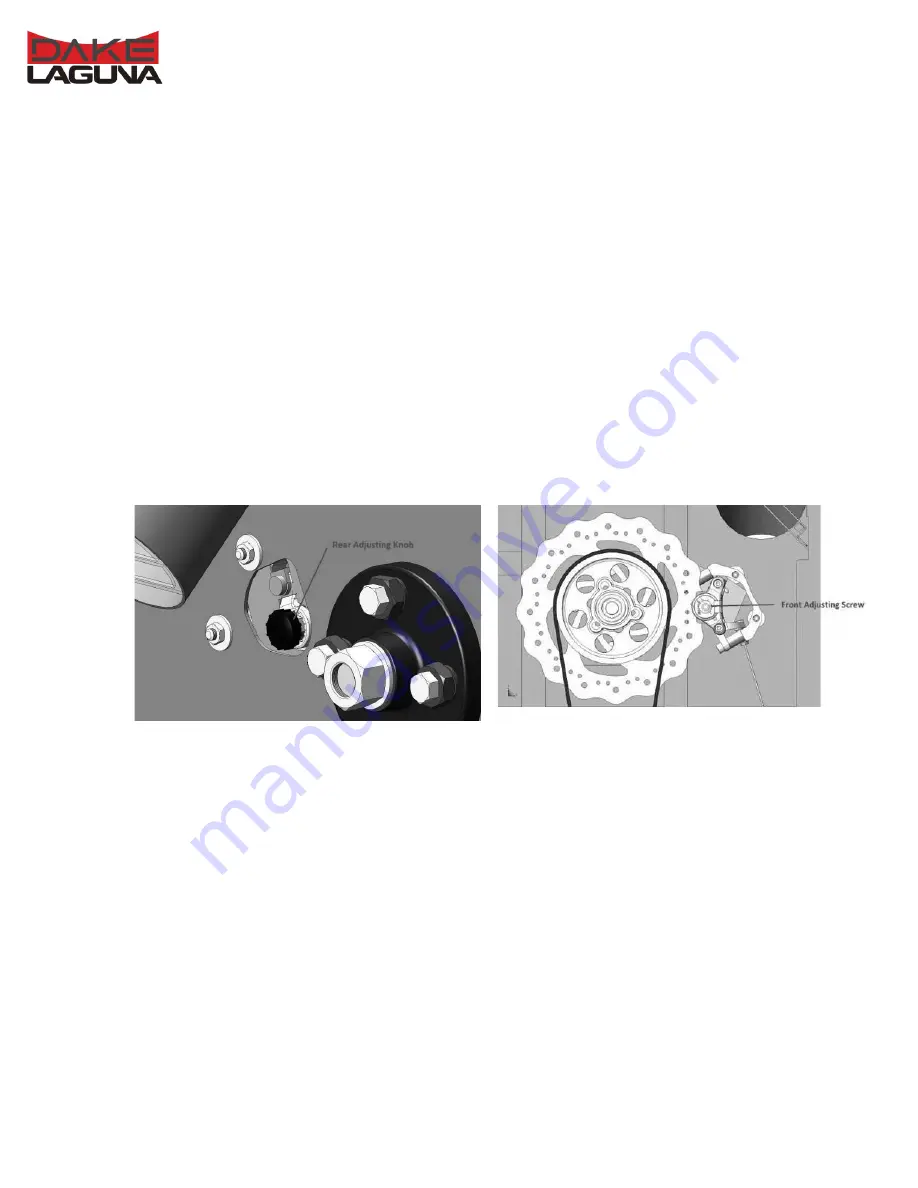
14CX
25
REV#072023
Replacing the Drive Belt
1. Loosen the motor clamp bolts and move the motor so that the tension is completely removed
from the drive belt. Remove the blade. Loosen the two hex nuts that hold the brake to the
bandsaw frame and slide it out of the way of the disc.
2. Remove the flywheel shaft nut that clamps the wheel axle (back of the bandsaw).
3. Pull the lower flywheel off the bandsaw. You may have to use a gear puller to remove the lower
wheel.
4. Replace the drive belt.
5. Refit the lower wheel and re-clamp with the flywheel shaft nut.
6. Tension the drive belt and tighten the motor clamping bolts.
Note:
It is better to replace the drive belt early than to have a breakdown during an important job.
Note:
Take great care not to damage the bearings when taking the flywheel off and reassembling.
Adjusting the Brake
The back break adjustor moves clockwise to remove slack in the brake pad.
The front brake adjustor is rotated clockwise with an Allen key to remove slack in the brake pad.
Back break adjuster
Front brake adjuster
(Flywheel not shown for clarity)
Summary of Contents for LAGUNA 14CX
Page 26: ...14CX 26 REV 072023 WIRING DIAGRAMS...
Page 27: ...14CX 27 REV 072023...