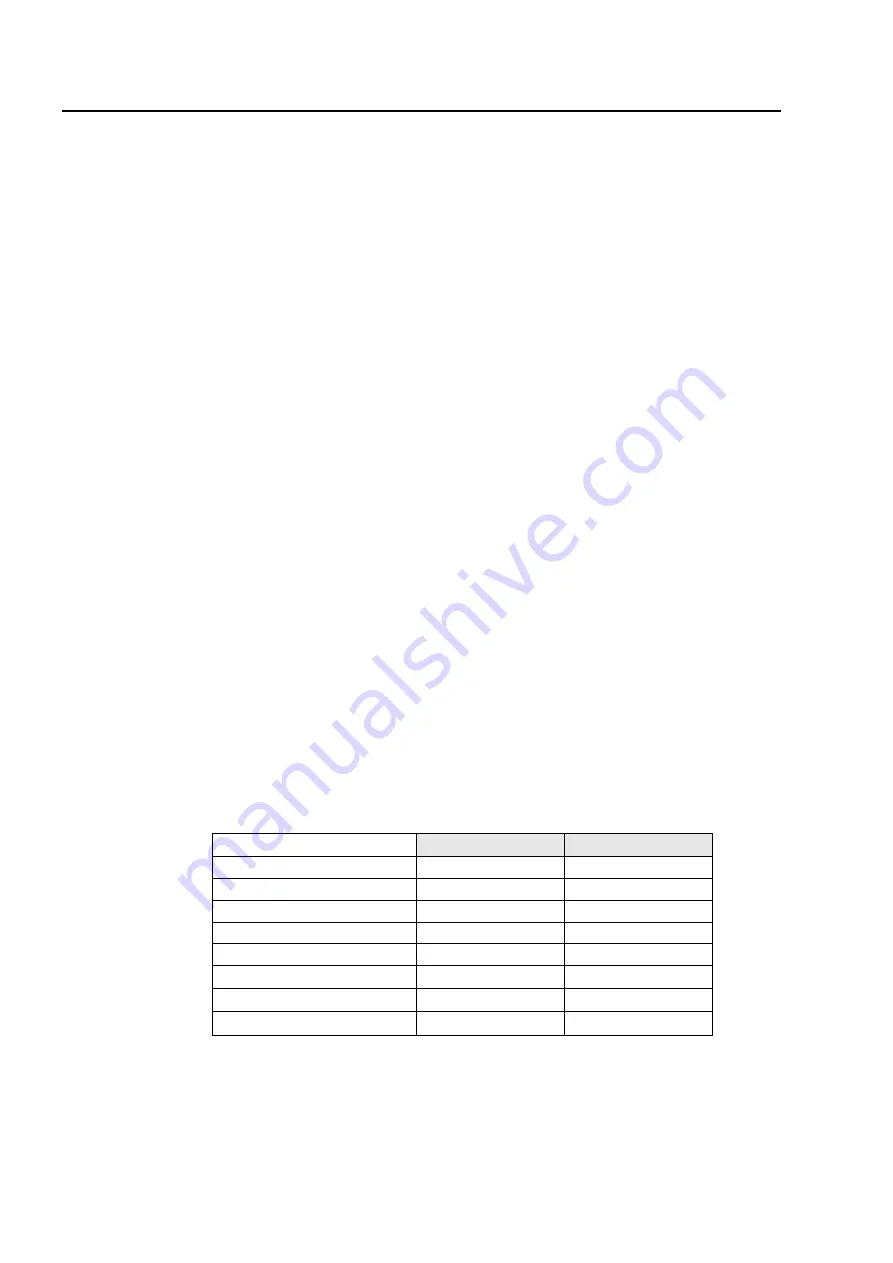
ROLLOMAXIMUM XL
Page 8
Road transport
•
All statutorily required safety and warning features must be fitted and tested
before transporting the machine on public roads. The driver is responsible for
correct lighting and warning signs in accordance with traffic regulations.
•
Check with local traffic authorities whether transport on public roads is allowed
given the machine's dimensions.
•
When transporting, ensure permitted total weight for tractor is not exceeded
and that loading on tractor front axle is not less than 20% of tractor net weight.
If this is the case, use weights on tractor front.
Correct use
•
Correct use of the machine includes observing the manufacturer's operating,
maintenance and repair instructions, and ensuring that original spare parts
are always used.
•
The implement may only be used, maintained or repaired by persons who are
familiar with it and who are aware of the risks that may be involved.
•
The manufacturer cannot be held liable for injury or damage arising from modi-
fications made to the machine performed without its prior agreement. Neither
can the manufacturer be held liable for injury or damage arising from incorrect
use. Such liability rests solely with the user.
•
Do not add extra weight to the implement.
Technical data
ROLLOMAXIMUM XL
Width (cm)
930
1230
HP (recommended)
Min. 275
Min. 350
Weight in kg (cross-kill):
10,470
12,970
Transport width
3.00 m
3.00 m
Sections back (pcs.)
6
8
Axles front (pcs.)
5
3
Wheels
600/50-22.5
710/40-22.5
Brakes
Yes
Yes
Light
Yes
Yes