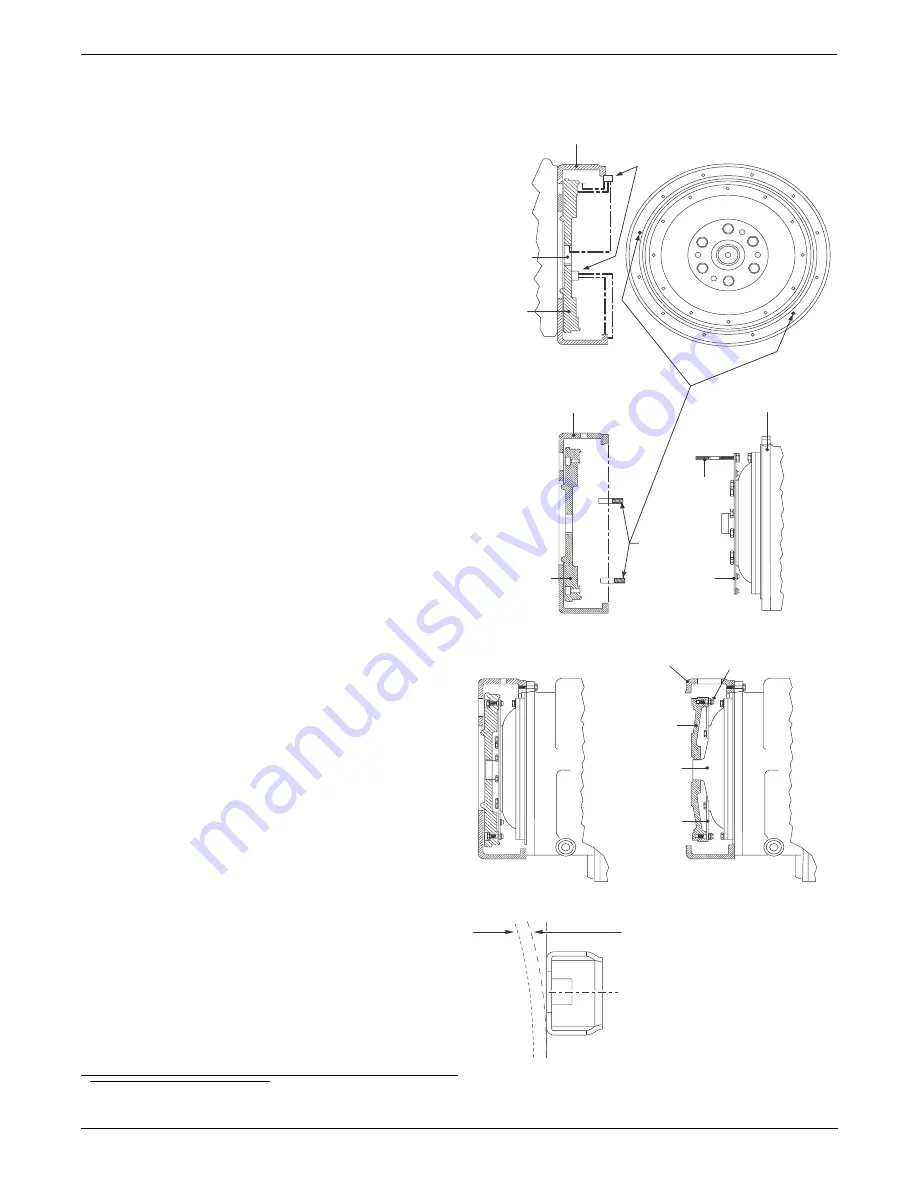
13
Dana Holding Corporation
TSM-0064 - TE27/32 4-Speed LD with Full Flow Control Valve Service Manual
TRANSMISSION TO ENGINE INSTALLATION
1.
Remove all burrs from flywheel mounting face and
nose pilot bore. Clean drive plate surface with sol-
vent. Dry thoroughly.
2.
Check engine flywheel and housing for conformance to
standards SAE #3 per SAE J-927 and J-1033 tolerance
specifications for pilot bore size, pilot bore runout, and
mounting face flatness. Measure and record engine
crankshaft end play.
3.
Install two 2.50” [63.5 mm] long transmission to fly-
wheel housing guide studs in the engine flywheel hous-
ing as shown. Rotate the engine flywheel to align a drive
plate mounting screw hole with the flywheel housing
access hole.
4.
*
Install a 4.00” [101.6 mm] long drive plate locating stud
.3750-24 fine thread in a drive plate nut. Align the locat-
ing stud in the drive plate with the flywheel drive plate
mounting screw hole positioned in Step 3.
5.
Rotate the transmission torque converter to align the
locating stud in the drive plate with the flywheel drive
plate mounting screw hole positioned in Step 3. Locate
transmission on flywheel housing.
6.
Align drive plate to flywheel and transmission to fly-
wheel housing guide studs. Install transmission to fly-
wheel housing screws. Tighten screws to specified
torque. Remove transmission to engine guide studs.
Install remaining screws and tighten to specified torque.
7.
*
Remove drive plate locating stud.
8.
Install drive plate attaching screw and washer. Snug
screw but d
do not tighten. Some engine flywheel hous-
ings have a hole located on the flywheel housing cir-
cumference in line with the drive plate screw access
hole. A screwdriver or pry bar used to hold the drive
plate against the flywheel will facilitate installation of the
drive plate screws. Rotate the engine flywheel and
install the remaining seven (7) flywheel to drive plate
attaching screws. Snug screws but d
do not tighten. After
all eight (8) screws are installed, tighten each capscrew
to 26-29 lbs. ft. (35-39 N•m). This will require tightening
each screw and rotating the engine flywheel until the full
amount of eight (8) screws have been tightened to
specified torque.
9.
Measure engine crankshaft end play after transmission
has been completely installed on engine flywheel. This
value must be within 0.001” [0.025 mm] of the end play
recorded in Step 2.
10.
Axial force acting on flywheel is continuous 940 N /
intermittent 1885 N.
11.
Hose line operating requirements: Pressure lines
suitable for operating from ambient to 120°C contin-
uous operating temperature, must withstand 25 bar
continuous pressure, with 50 bar intermittent surges.
Reference SAE spec J-517, 100RI hydraulic hose
specification. All hose lines used must be conform to
SAE spec J-1019 tests and procedures for high tem-
perature transmission oil hose. All hose lines and fit-
ting have a 19 mm inside diameter unless noted.
*
Does not apply to units having 3 intermediate drive plates. See Figure 4.
FLYWHEEL H OUSING
ENGINE
FLYWHEEL
FIG. 1
FLYWHEEL
PILOT BORE
MOUNT
DIAL INDICATOR
HERE
FLYWHEEL
FLYWHEEL HOUSING
CONVERTER HOUSING
DRIVE
PLATE
4"STUD
2
1/2
"ALIGNING
STUDS
FIG. 3
FIG.4
FLYWHEEL HOUSING
SPECIAL STUD, WASHER AND
SELF LOCK NUT FURNISHED
BY ENGINE MANUFACTURER.
FLYWHEEL
IMPELLER
COVER
INTERMEDIATE
DRIVE PLATES
FIG. 5
PLATES TO BE INSTALLED
WITH CONCAVE SIDE
TOWARD ENGINE FLYWHEEL.
Summary of Contents for SPICER TE27
Page 2: ......