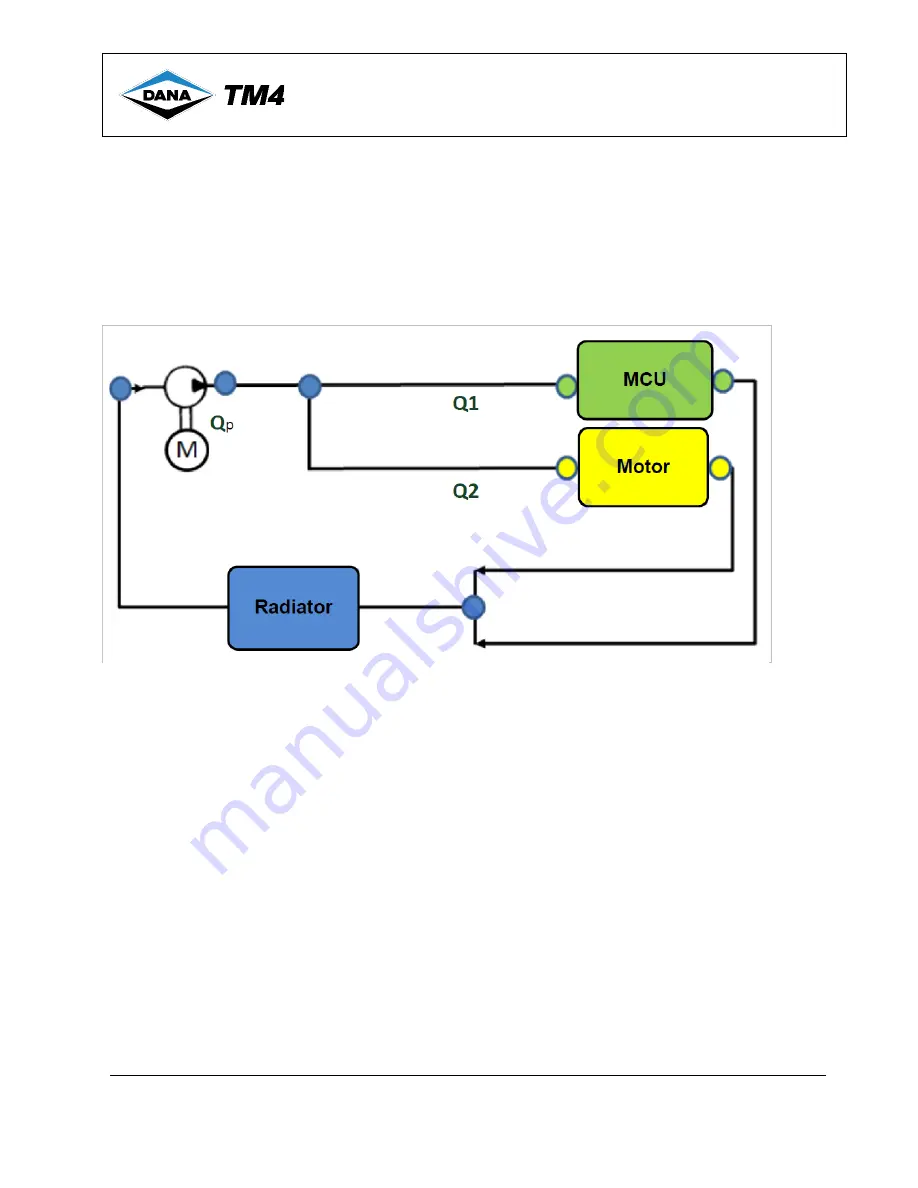
Installation Guide
CONFIDENTIAL
TG-0057_19 TM4 SUMO HD CO300-A1_A2_A2.5 Installation Guide
© Dana TM4 inc., 2013-2020
Page 18 of 42
2020-11-20
4.4.2 Parallel configuration
This configuration involves the MCU and motor being cooled in parallel.
As the cooling units are supplied by the vehicle integrator and the cooling system setup involves fine-tuning
and testing at the customer site, TM4 has no specific recommendations on how to achieve optimum
configuration but coolant liquid pressure must not reach or exceed 30 PSI.
See the System Specifications [5] for estimated pump requirements.
Figure 4
Parallel cooling system
See the System Specifications [5] for more information on coolant pressure drops and rate flow
management.