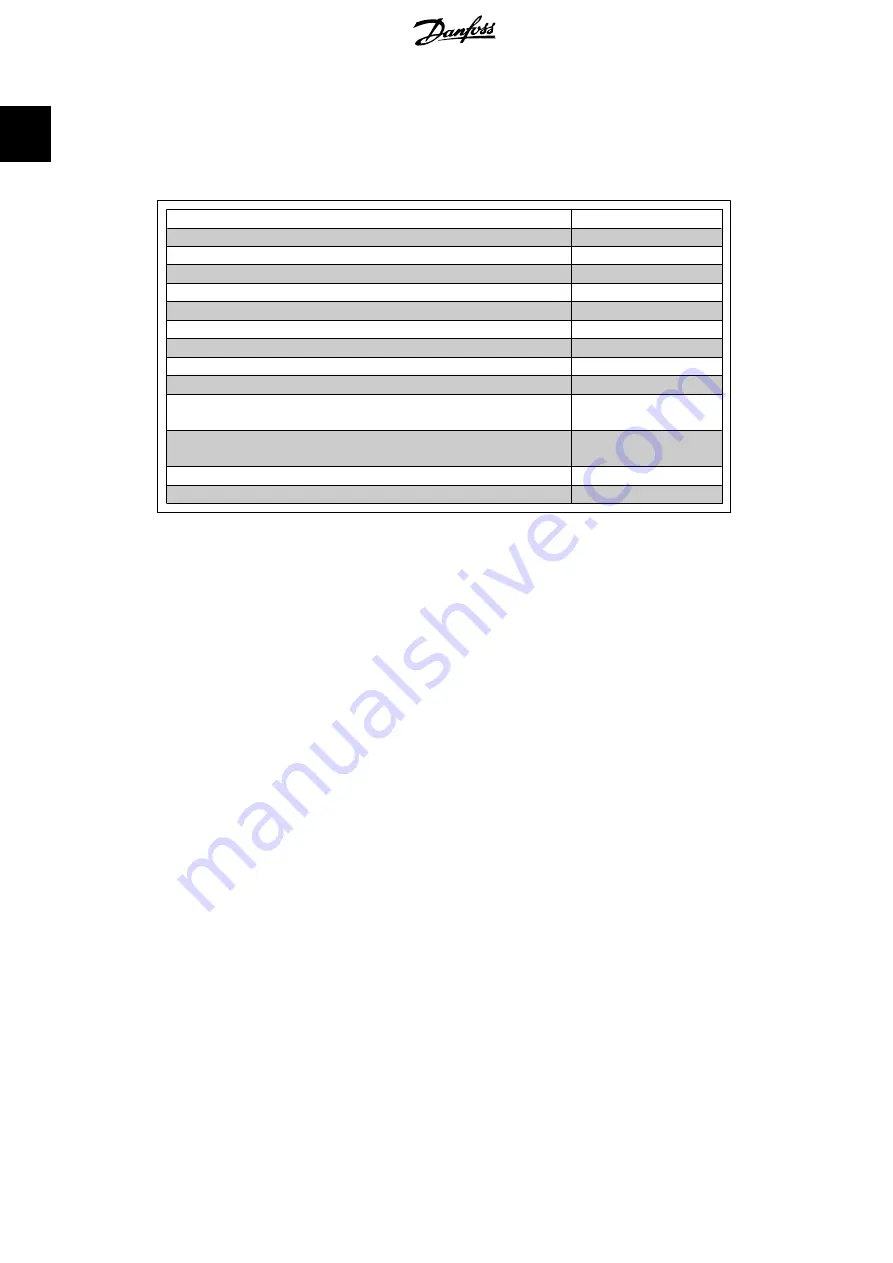
1.8. Available Literature
The following literature is available for the FC 100, 200 and 300 series.
Title
Literature no.
VLT HVAC Drive FC 100 Operating Instructions
MG.11.AX.YY
VLT HVAC Drive FC 100 Design Guide
MG.11.BX.YY
VLT HVAC Drive FC 100 Programming Guide
MG.11.CX.YY
VLT AQUA Drive FC 200 Operating Instructions
MG.20.NX.YY
VLT AQUA Drive FC 200 Design Guide
MG.20.MX.YY
VLT AQUA Drive FC 200 Programming Guide
MG.20.OX.YY
VLT AutomationDrive FC 300 Operating Instructions
MG.33.AX.YY
VLT AutomationDrive FC 300 Design Guide
MG.33.BX.YY
VLT AutomationDrive FC 300 Programming Guide
MG.33.MX.YY
VLT AutomationDrive FC 100, 200 and 300 PROFIBUS Operating
Instructions
MG.33.CX.YY
VLT AutomationDrive FC 100, 200 and 300 DeviceNet Operating In-
structions
MG.33.DX.YY
VLT AutomationDrive FC 300 MCT 10 Software Dialogue
MG.33.EX.YY
PROFIBUS DP V1 Design Guide
MG.90.EX.YY
X = Revision number
Y = Language code
Please also refer to
www.danfoss.com/drives
for frequently asked questions and additional infor-
mation.
1. Introduction
FC 100/ 200/ 300 DeviceNet
10
MG.33.D3.02 - VLT
®
is a registered Danfoss trademark
1