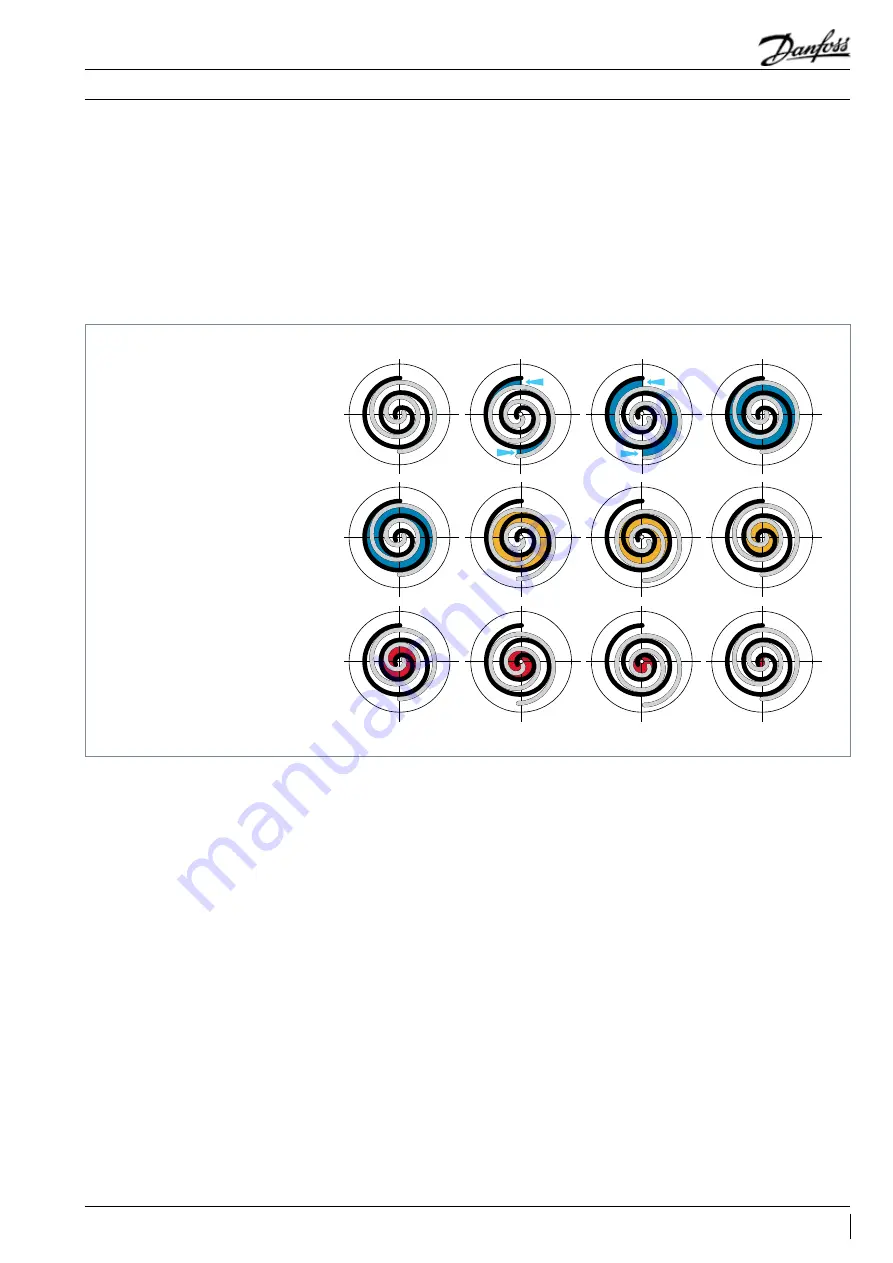
Scroll compression principle
Danfoss scroll compressors are manufactured
using the most advanced machining, assembly
and process control techniques. In the design
of both the compressor and the factory, very
high standards of reliability and process control
were first priority. The result is a highly efficient
product with the highest reliability obtainable,
and a low sound level.
The entire scroll compression process is
illustrated below. The center of the orbiting scroll
traces a circular path around the center of the
fixed scroll. This movement creates compression
pockets between the two scroll elements.
Low pressure suction gas is trapped within each
crescent-shaped pocket as it forms; continuous
motion of the orbiting scroll serves to seal the
pocket, which decreases in volume as the pocket
moves towards the center of the scroll set,
with a corresponding increase in gas pressure.
Maximum compression is achieved as the pocket
reaches the discharge port at the center.
Scroll compression is a continuous process: when
one pocket of gas is being compressed during
the second orbit, another gas quantity enters
a new pocket formed at the periphery and,
simultaneously, another is being discharged.
The scroll compression
process
SUCTION
COMPRESSION
DISCHARGE
7
FRCC.PC.035.A5.02
Application Guidelines
Single compressors