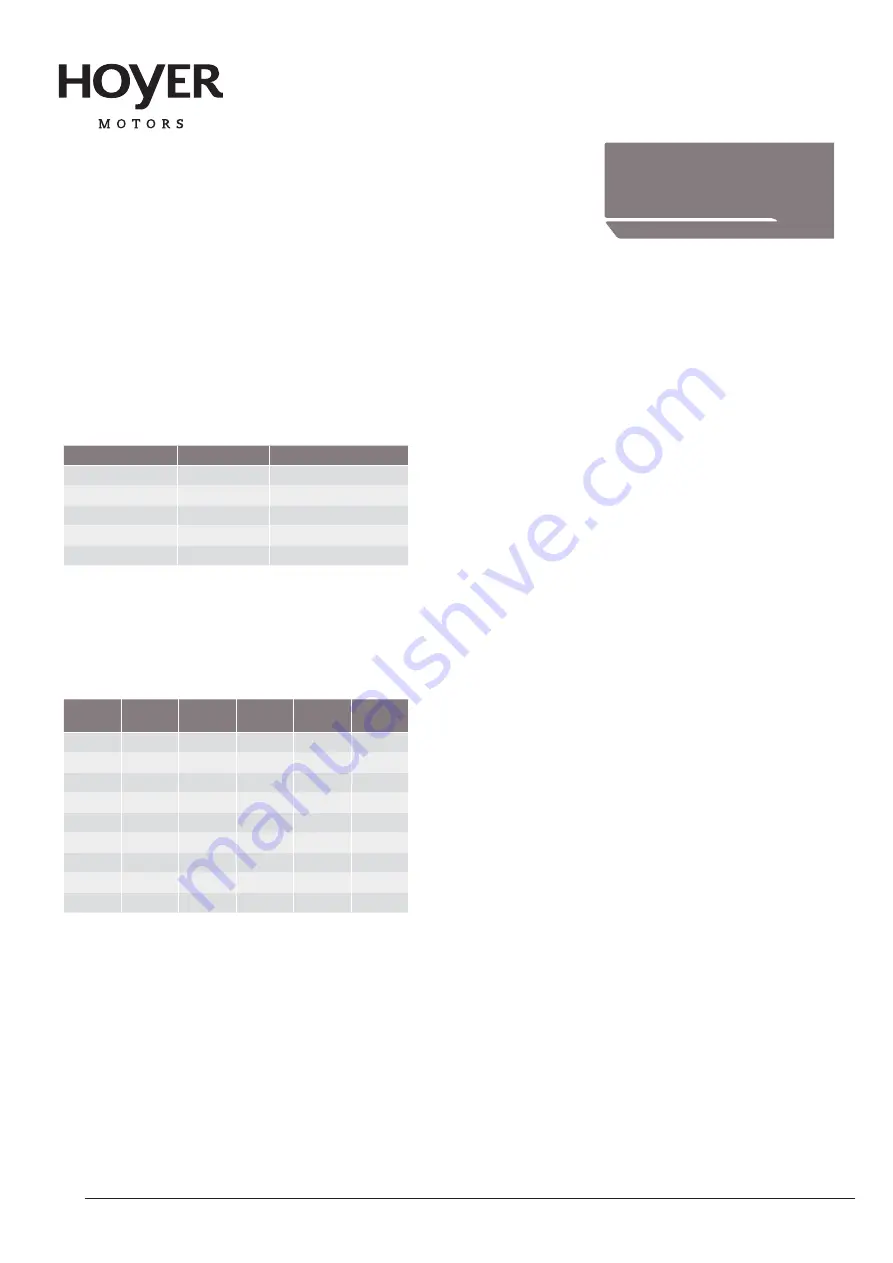
180R9288_AQ109686503100en-001301 | 57
© Danfoss | 2023.12
Operation guide
Installation, Operation and Maintenance Manual for PAHT 20-90 pumps
3
Motor
Manual
connections must be checked and tightened if necessary.
Bearing size and type are specified on the rating plate. Motor
types HMA3 and HMC3 is as standard with lifetime greased
bearings in motors size
≤
180 for cast iron and size
≤
132 for
aluminium. Motor types HMA2 and HMC2 is as standard
with lifetime greased bearing in motors size
≤
225.
Motor types MS and Y2E is as standard with lifetime greased
bearing in motors size
≤
160.
Typical duty hours for lifetime lubricated bearings.
Frame size
Poles
Typical lifetime
56 - 160
2 - 8
40,000h
180
2
35,000h
200
2
27,000h
225
2
23,000h
180 - 225
4 - 8
40,000h
Motors with a re-greasing system must be lubricated with
high quality lithium complex grease, NLGI grade 2 or 3, with
a temperature range of between -40°C to +150°C.
Motors are normal fitted with a data plate with greasing
information; if it is missing use the following re-greasing
intervals.
Frame
size
Grease
(g)
2 pole
(h)
4 pole
(h)
6 pole
(h)
8 pole
(h)
160
20
4200
7000
8500
8500
180
20
4200
7000
8500
8500
200
25
3100
6500
8500
8500
225
25
3100
6500
8500
8500
250
35
2000
6000
7000
7000
280
35
2000
6000
7000
7000
315
50
1500
5500
6500
6500
355
60
1000
4000
5000
6000
400
80
800
3000
4000
6000
Grease the motor while running, open the grease outlet plug
and let the motor run 1-2 hours before the outlet grease plug
is closed again.
Grease the motor for the first time during commissioning.
The following applies in general for both lifetime lubricated
and re-lubricated bearings:
At 60Hz the time will be reduced by app. 20%.
Data for vertically mounted motors are half of the above
values.
The table values are based on an ambient temperature of
25°C. The values must be halved for every 15K increase in
bearing temperature.
Higher speed operations, e.g. frequency converter drive will
require shorter greasing intervals. Typically, doubling the
speed will reduce the values by 50%.
Special note for Atex Zone 22 and nA motors
Designation of motor according to IEC standard:
II 3D Ex tc IIIB T120°C
II 3G Ex nA IIC T3
The hazardous 3-phase asynchronous motors are in
accordance with International standard IEC 60079-31 and
IEC 60079-15.
Only one electrical installation may be installed in one
specified area (zone).
Only certificated cable glands may be used. Unused glands
must be closed.
Connections must be made in such a way as to ensure that
a permanently safe electrical connection is maintained, both
for the main supply and earth connection.
Installations must be in accordance with actual standards
for installation in hazardours area.
It is recommended that the IEC standard is followed according
to temperature and dust on the motor surface.
The use of motors with so much surface dust that the motor
temperature increases is not permitted.
Regularly cleaning is recommended.
The radial shaft sealing ring is part of the ATEX certification.
It is important that the ring is always intact.
The shaft sealing must be regularly checked, and if dry it
must be lubricated. It is recommended that the seal is re-
lubricated regularly.
Always use the original seal ring when replaced.
Replacing bearings also means replacing the seals.
All machines must be inspected regularly for mechanical
damage.
The user is responsible for changing parts in accordance
with the lifetime of parts, in particular:
bearings, grease and lubrication of shaft sealing.
Maintenance, repairs and replacement on this type must
only be carried out by qualified specialists.