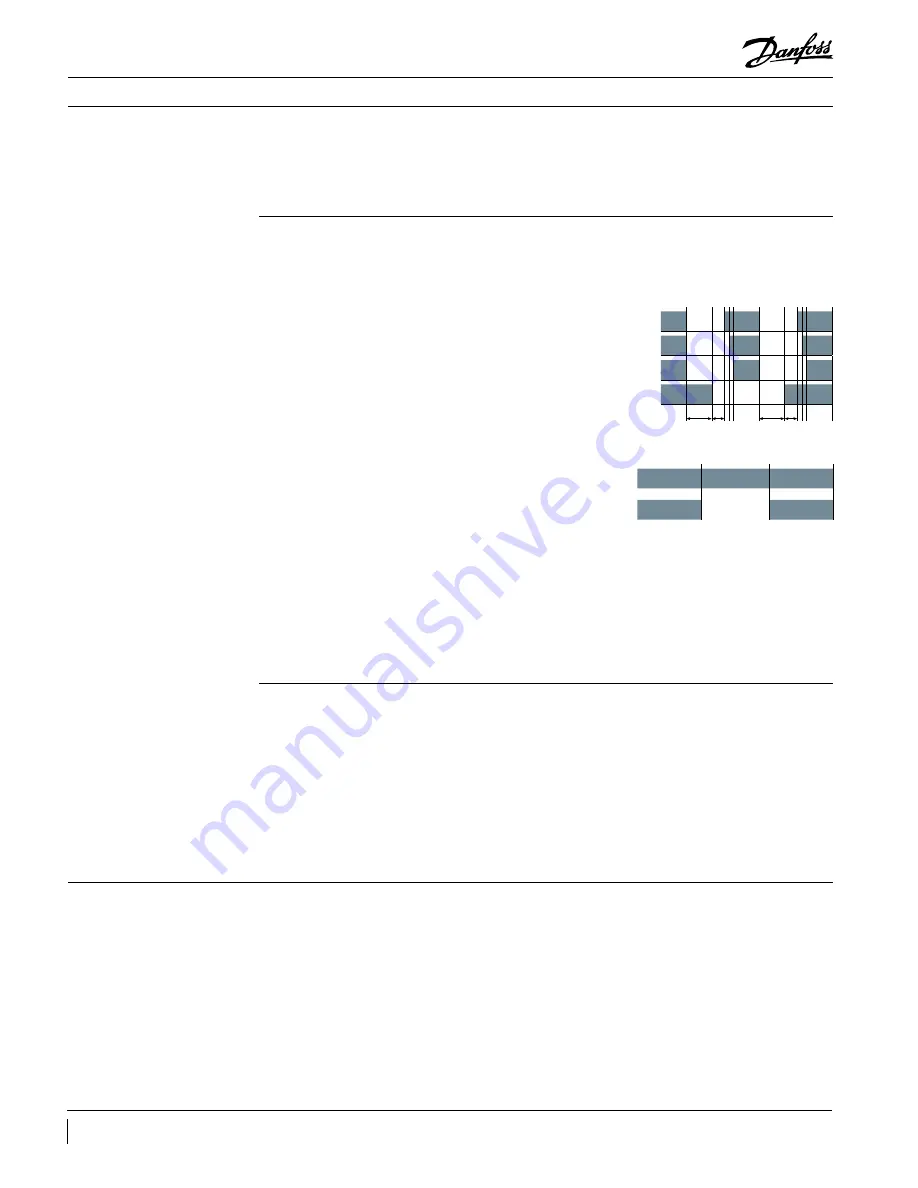
Application guidelines
40
FRCC.PC.021.A5.22
Specific application recommendations
Apart from residual moisture in the system
after commissioning, water could also enter the
refrigeration circuit during operation. Water in
the system shall always be avoided. Not only
because it can shortly lead to electrical failure,
sludge in sump and corrosion but in particular
because it can cause serious safety risks.
Common causes for water leaks are corrosion and
freezing.
Corrosion: Materials in the system shall be
compliant with water and protected against
corrosion.
Freezing: When water freezes into ice its volume
expands which can damage heat exchanger
walls and cause leaks. During off periods water
inside heat exchangers could start freezing when
ambient temperature is lower than 32°F. During
on periods ice banking could occur when the
circuit is running continuously at too low load.
Both situations should be avoided by connecting
a pressure and thermostat switch in the safety
line.
Water utilizing systems
The use of a suction line accumulator is strongly
recommended in reversible-cycle applications.
This because of the possibility of a substantial
quantity of liquid refrigerant remaining in the
evaporator, which acts as a condenser during the
heating cycle.
This liquid refrigerant can then return to the
compressor, either flooding the sump with
refrigerant or as a dynamic liquid slug when
the cycle switches back to a defrost cycle or to
normal cooling operations.
Sustained and repeated liquid slugging and
flood back can seriously impair the oil’s ability
to lubricate the compressor bearings. This
situation can be observed in wet climates where
it is necessary to frequently defrost the outdoor
coil in an air source heat pump. In such cases a
suction accumulator becomes mandatory.
Suction line accumulator
Defrost and reverse cycle
gas to collect and to reduce the pressure peak
during the time it takes for the valve to change
position. At the same time, it is important that
the selection and sizing of the reversing or 4-way
valve ensure that the valve switches quickly
enough to prevent against too high discharge
pressure and nuisance high-pressure cutouts.
Check with the valve manufacturer for optimal
sizing and recommended mounting positions.
The Danfoss PSH scroll compressor has the
ability to withstand a certain amount of liquid
refrigerant dynamic slug.
When compressors are installed in parallel,
in order to limit liquid amount handled per
compressor when beginning and ending defrost,
it is recommended to avoid running part load
(keep all compressors running or keep them
stopped when moving 4-way valves).
In order to limit liquid amount handled per
compressor when beginning & ending defrost,
one of the 2 defrost cycle logics are required:
stop all compressors before moving the
4 way valve:
first stop compressors
wait for 10 seconds
move the 4 way valve
wait for 2 seconds
restart the compressors with a max. 0.5
second delay between 2 successive starts
or
keep all compressors running during defrost
cycle
Defrost cycle logic must respect all system
components recommendations, in particular 4
way valve Max. Operating Pressure Differential.
EXV can also be opened when compressors are
stopped and before 4 way valve is moving in
order to decrease pressure difference. Opening
degree and time have to be set in order to keep
a minimum pressure difference for 4 way valve
moving. Each application design however should
be thoroughly tested to ensure acceptable
operating characteristics.
Start of defrost
sequence
End of defrost
sequence
Compressor 1 on
Compressor 1 off
Compressor 2 on
Compressor 2 off
Compressor 3 on
Compressor 3 off
4 way valve position 1
4 way valve position 2
10" 2"
10" 2"
Start of defrost
sequence
End of defrost
sequence
Compressors on
Compressors off
4 way valve 1
4 way valve 2