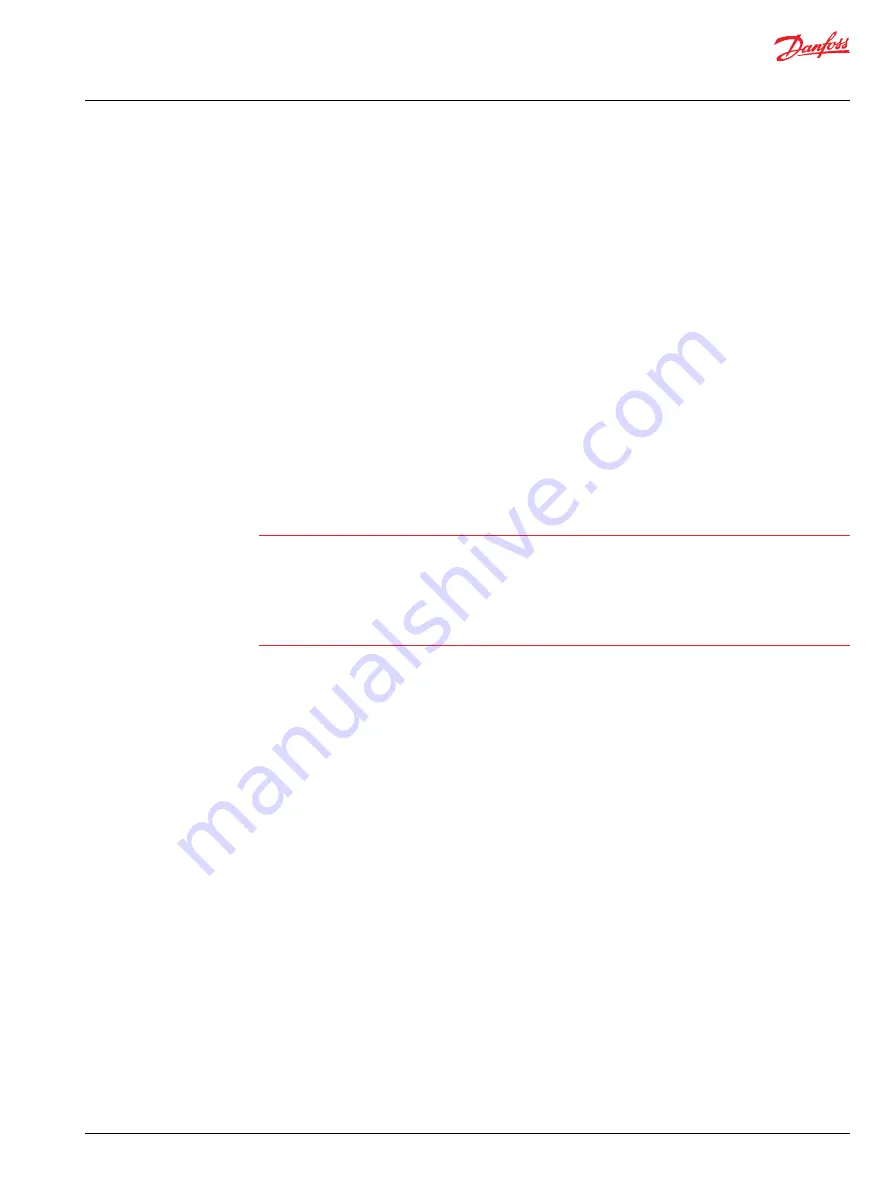
Safety in application
All types of control valves (incl. proportional valves) can fail, thus the necessary protection against the
serious consequences of function failure should always be built into the system. For each application an
assessment should be made for the consequences of pressure failure and uncontrolled or blocked
movements. To determine the degree of protection that is required to be built into the application,
system tools such an FMEA (Failure Mode and Effect Analysis) and Hazard and Risk Analysis can be used.
FMEA – IEC EN 61508
FMEA (Failure Mode and Effect Analysis) is a tool used for analyzing potential risks. This analytical
technique is utilized to define, identify, and prioritize the elimination or reduction of known and/or
potential failures from a given system before it is released for production. Please refer to the standard IEC
FMEA 61508.
Hazard and risk analysis ISO 12100-1/14121
This analysis is a tool used in new applications as it will indicate whether there are special safety
considerations to be met according to the machine directives EN 13849. Dependent on the determined
levels conformity this analysis will detirmine if any extra requirements for the product design,
development process, production process or maintenance, example the complete product life cycle.
W
Warning
All brands and all types of directional control or proportional valves, which are used in many different
operation conditions and applications, can fail and cause serious damage.
Analyze all aspects of the application. The machine builder/system integrator alone is responsible for
making the final selection of the products and assuring that all performance, safety and warning
requirements of the application are met. The process of choosing the control system and safety levels is
governed by the machine directives EN 13849 (Safety related requirements for control systems).
Safety guidelines
•
When failure, damage or defect occurs, the PVE-EX has to be replaced.
•
A failing PVE-EX must under no circumstance be repaired.
•
No modifications, which could damage the explosion-safety and protection, are allowed to the PVE-
EX, the cable gland, or on the cable.
•
Demounting a PVE-EX should be done in an atmosphere with no potenential for explosions.
•
The machine and system approval has to be issued before using the PVE-EX in explosive-areas.
•
The manufacturer has the application responsibility and is solely responsible for the safety of the
system.
•
Deviations from recommended torque when mounting parts can harm performance and the PVE-EX.
•
Do not adjust, bend or damage the position transducer (LVDT) as this will influence the safety and
performance.
•
When replacing the PVE-EX, the electrical and the hydraulic systems must be turned off and the oil
pressure released.
•
Hydraulic oil can cause both environmental damage and personal injuries.
•
Module replacement can introduce contamination and errors to the system. It is important to keep
the work area clean and components should be handled with care.
Technical Information
Electrohydraulic Actuators PVE-EX
Safety and monitoring
©
Danfoss | October 2017
BC00000393en-US0102 | 21