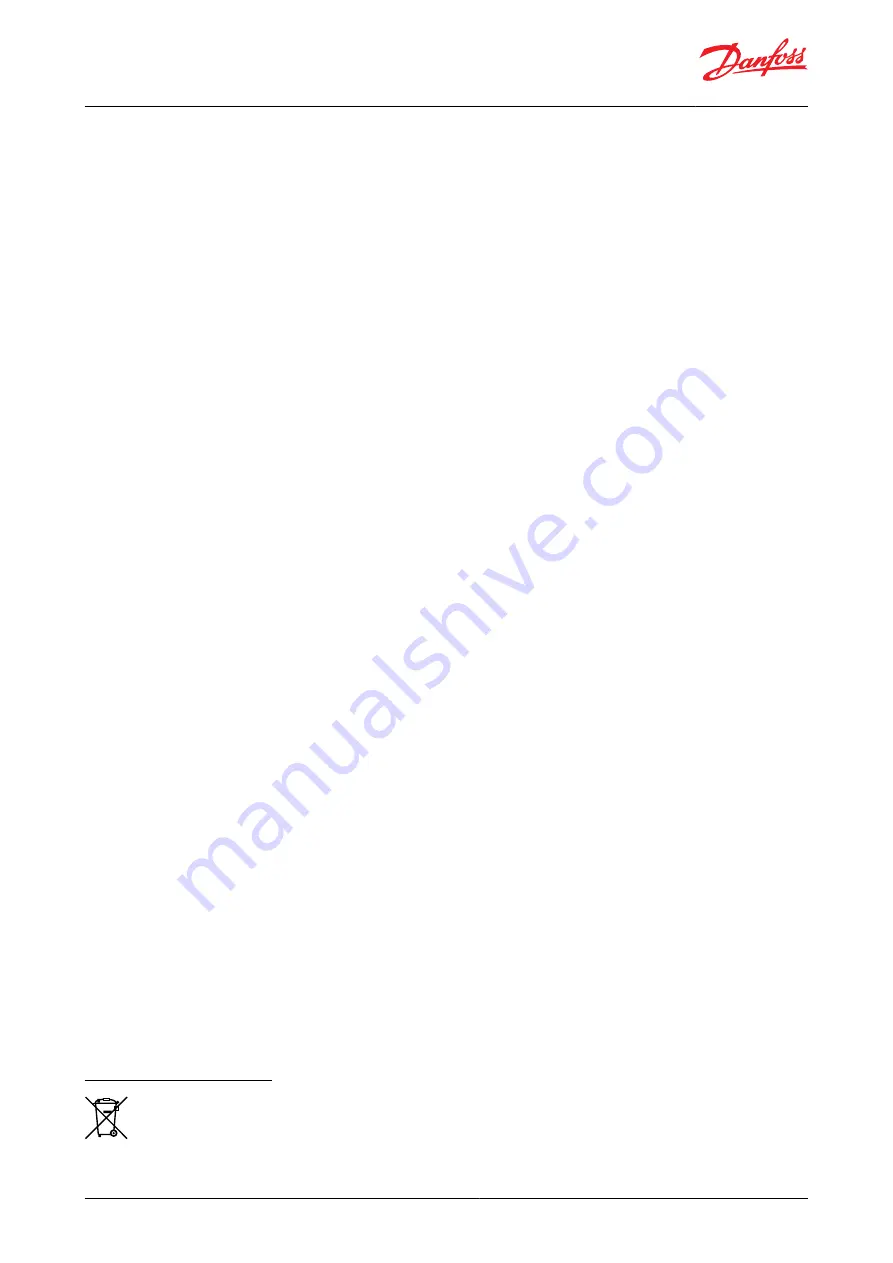
• Phase order: Reverse rotation is obvious if the compressor does not build up pressure and sound level is abnormal
high. VCH compressor will only operate properly in one direction. If electrical connections are done correctly
between the drive and the compressor terminals (compressor terminals T1, T2 ,T3 and drive terminals U, V & W
matching), the drive will provide correct phase supply to the compressor, and reverse rotation will be not possible:
For more details refer to
• Voltage and voltage imbalance within tolerance: For more details refer to section
Initial start-up
• Cranckcase heaters must be energized at least 6 hours in advance to remove liquid refrigerant.
• Do not provide any power to the drive unless suction and discharge service valves on compressor are open, if
installed.
• Energize the drive. The compressor must start, according to
defined
ramp-up settings. If the compressor does not
start, check wiring conformity.
• Check the frequency converter control panel: If any alarm is displayed check the wiring and in particular the
polarity of the control cables. If an alarm is shown, refer to the frequency converter application manual. Verify in
particular the combination of compressor, frequency converter and refrigerant.
• Check current draw and voltage levels on the mains. The values for the compressor electrical motor can be directly
displayed on the frequency converter control panel.
System monitoring
The system must be monitored after initial startup for a minimum of 60 minutes to ensure proper operating
characteristics such as:
• Proper metering device operation and desired superheat readings
• Suction and discharge pressure are within acceptable levels
• Crankcase heaters must be energized at least 6 hours in advance to remove refrigerant.
• Correct oil level in compressor sump indicates proper oil return
• Low foaming in sight glass and compressor sump temperature above 12K for VCH115 saturation temperature to
show that there is no refrigerant migration taking place
• Current draw of compressor within acceptable values (MOC ratings)
• No abnormal vibrations and noise.
Oil level checking and top-up
In installations with good oil return and line runs up to 15m (49.2 feet), no additional oil is required. If installation
lines exceed 15m (49.2 feet), additional oil may be needed. 3% of the total system refrigerant charge (in kg/lb) can
be used to roughly
define
the required oil top-up quantity (in liters) but in any case the oil charge has to be adjusted
based on the oil level in the compressor sight glass.
In the phase of system study, oil sight glass would be added.
When the compressor is running under stabilized conditions, the oil level must be visible in the sight glass.
The presence of foam
filling
in the sight glass indicates large concentration of refrigerant in the oil and / or presence
of liquid returning to the compressor.
The oil level can also be checked a few minutes after the compressor stops, the level must be visible in sight glass.
When the compressor is
off,
the level in the sight glass can be
influenced
by the presence of refrigerant in the oil.
Top-up the oil while the compressor is idle. Use any accessible connector on the compressor suction line and a
suitable pump.
Dismantle and disposal
Danfoss recommends that compressors and compressor oil should be recycled by a suitable company at its
site.
Scroll compressors, VCH115 | Application
© Danfoss | Climate Solutions | 2023.08
AB392939083370en-000202 | 48