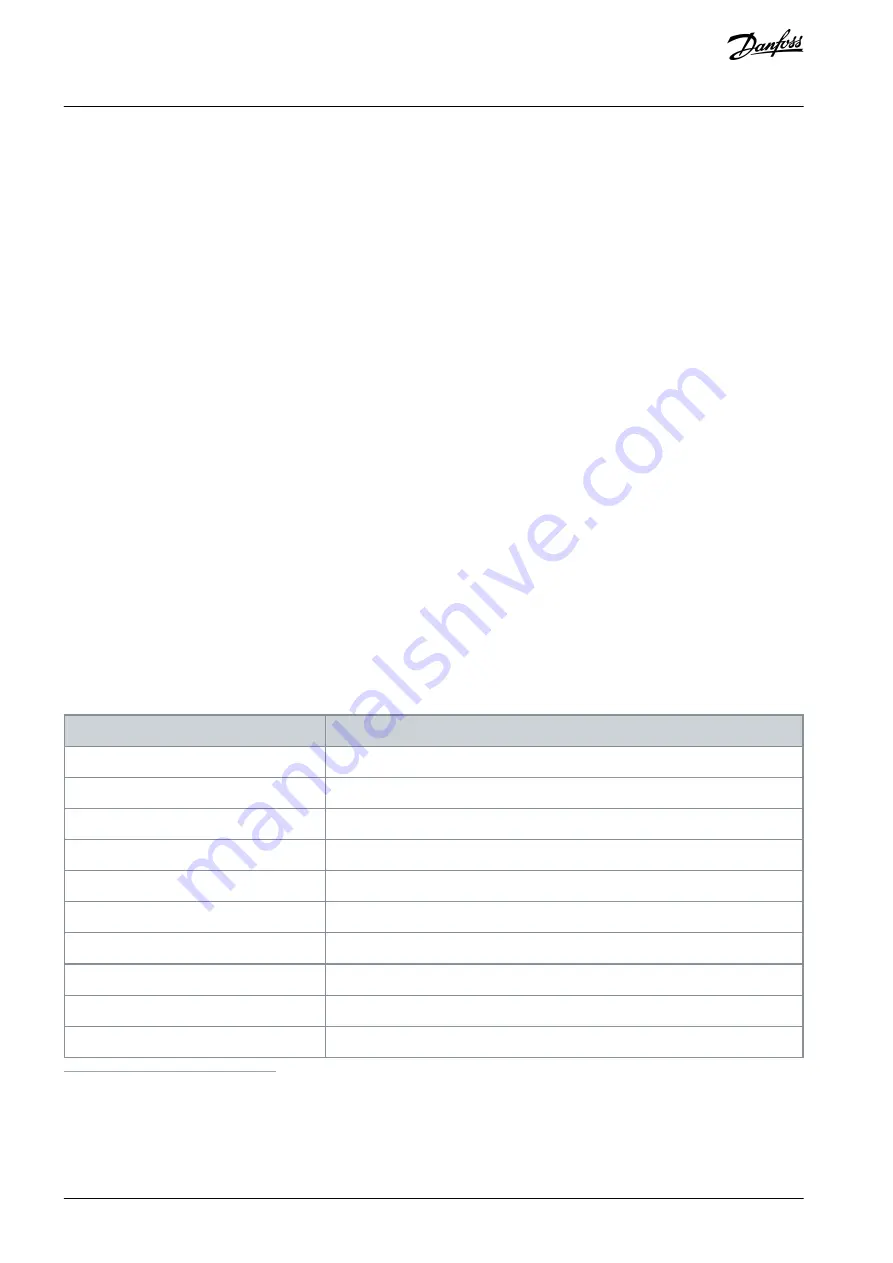
2.
3.
4.
5.
6.
7.
•
•
•
•
•
•
•
Set
parameter 20-93 PI Proportional Gain
to 0.3 and increase it until the feedback signal begins to oscillate. If necessary, start
and stop the drive or make step changes in the setpoint reference to attempt to cause oscillation.
Reduce the PI proportional gain until the feedback signal stabilizes.
Reduce the proportional gain by 40–60%.
Set
parameter 20-94 PI Integral Time
to 20 s and reduce it until the feedback signal begins to oscillate. If necessary, start and
stop the drive or make step changes in the setpoint reference to attempt to cause oscillation.
Increase the PI integral time until the feedback signal stabilizes.
Increase the integral time by 15–50%.
3.3 Ambient Running Conditions
3.3.1 Air Humidity
The drive has been designed to meet the IEC/EN 60068-2-3 standard, EN 50178 9.4.2.2 at 50 °C (122 °F).
3.3.2 Acoustic Noise or Vibration
If the motor or the equipment driven by the motor - for example, a fan - makes noise or vibrations at certain frequencies, configure
the following parameters or parameter groups to reduce or eliminate the noise or vibrations:
Parameter group 4-6* Speed Bypass
.
Set
parameter 14-03 Overmodulation
to
[0] Off
.
Switching pattern and switching frequency
parameter group 14-0* Inverter Switching
.
Parameter 1-64 Resonance Dampening
.
3.3.2.1 Acoustic Noise
The acoustic noise from the drive comes from 3 sources:
DC-link coils.
Integral fan.
RFI filter choke.
Table 6: Typical Values Measured at a Distance of 1 m (3.28 ft) from the Unit
Enclosure size
Level [dBA]
(1)
H1
43.6
H2
50.2
H3
53.8
H4
64
H5
63.7
H6
71.5
H7
67.5 (75 kW (100 hp) 71.5 dB)
H8
73.5
H13
73
H14
75
1
The values are measured under the background of 35 dBA noise and the fan running with full speed.
AJ363928382091en-000101 / 130R0983
30 | Danfoss A/S © 2021.04
Product Overview
VLT® Flow Drive FC 111
Design Guide