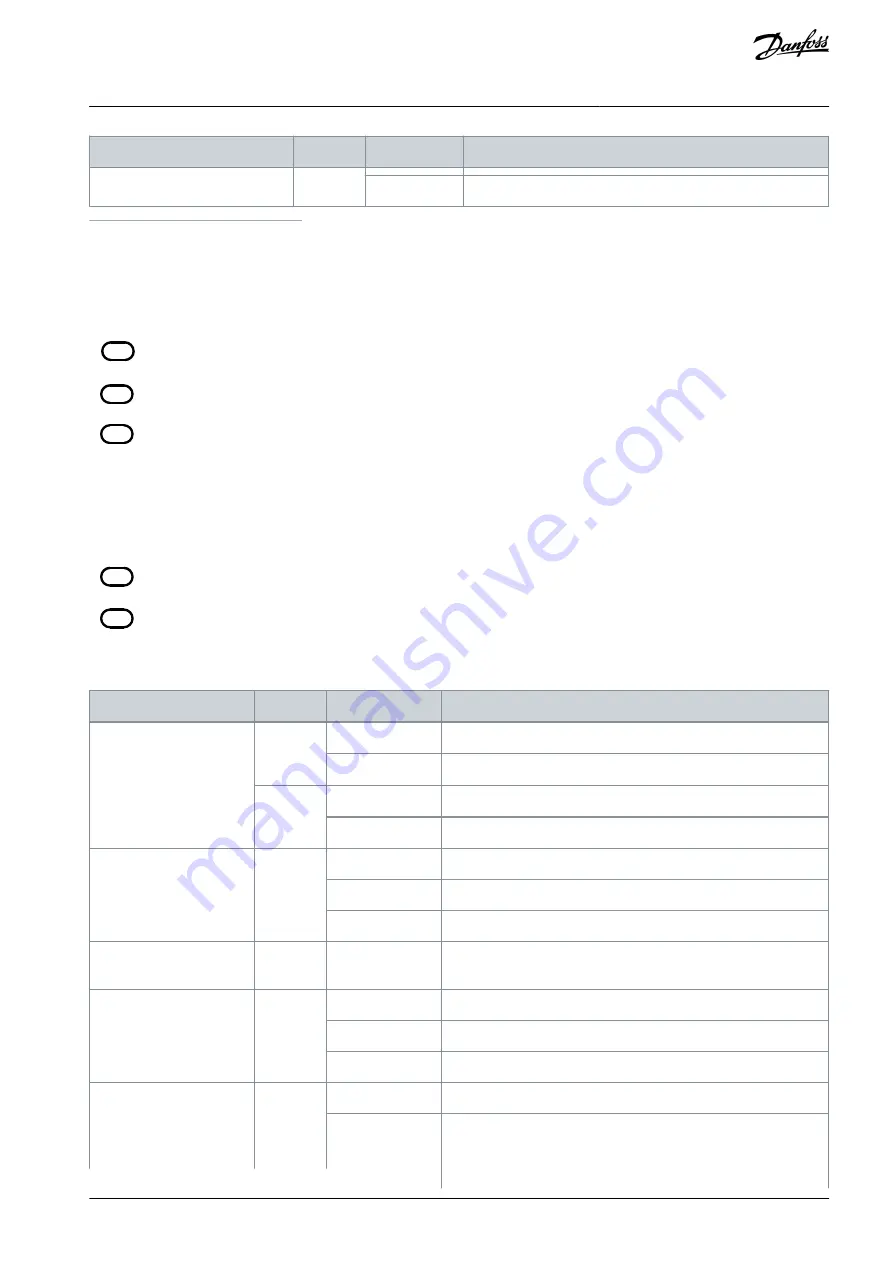
LED
Color
Flash status
Description
(Link/activity status of
Out
)
Off
No link.
1
POWERLINK
®
: Refer to the corresponding fieldbus standard.
7.2.4 Operating LEDs on the ACM 510
STATUS ACM
LINK/ACT
DEV
CAP ST
NET ST
X1
X2
e30bg578.10
Illustration 54: Operating LEDs on ACM 510
Table 20: Operating LEDs on ACM 510
LED
Color
Flash status
Description
DEV
Green
On
Device is in state
Operation enabled
.
Flashing
Device is in state
Standby
or
Power-up
.
Red
On
Device is in state
Fault
or
Fault reaction active
.
Flashing
DC-link is not applied at the input.
CAP ST
Green
On
Capacitors fully charged.
Flashing
Capacitors charging/discharging.
Off
Capacitors discharged.
NET ST
Green/red Fieldbus depend-
ent
Network status of the device (see corresponding fieldbus stand-
ard).
(1)
LINK/ACT X1
(Link/activity of
In
)
Green
On
Ethernet link established.
Flashing
Ethernet link established and active.
Off
No link.
LINK/ACT X2
Green
On
Ethernet link established.
Flashing
Ethernet link established and active.
AQ377148425069en-000101
/ 130R1213 | 87
Danfoss A/S © 2023.08
Operation
VLT® Servo Drive System ISD 511
Operating Guide