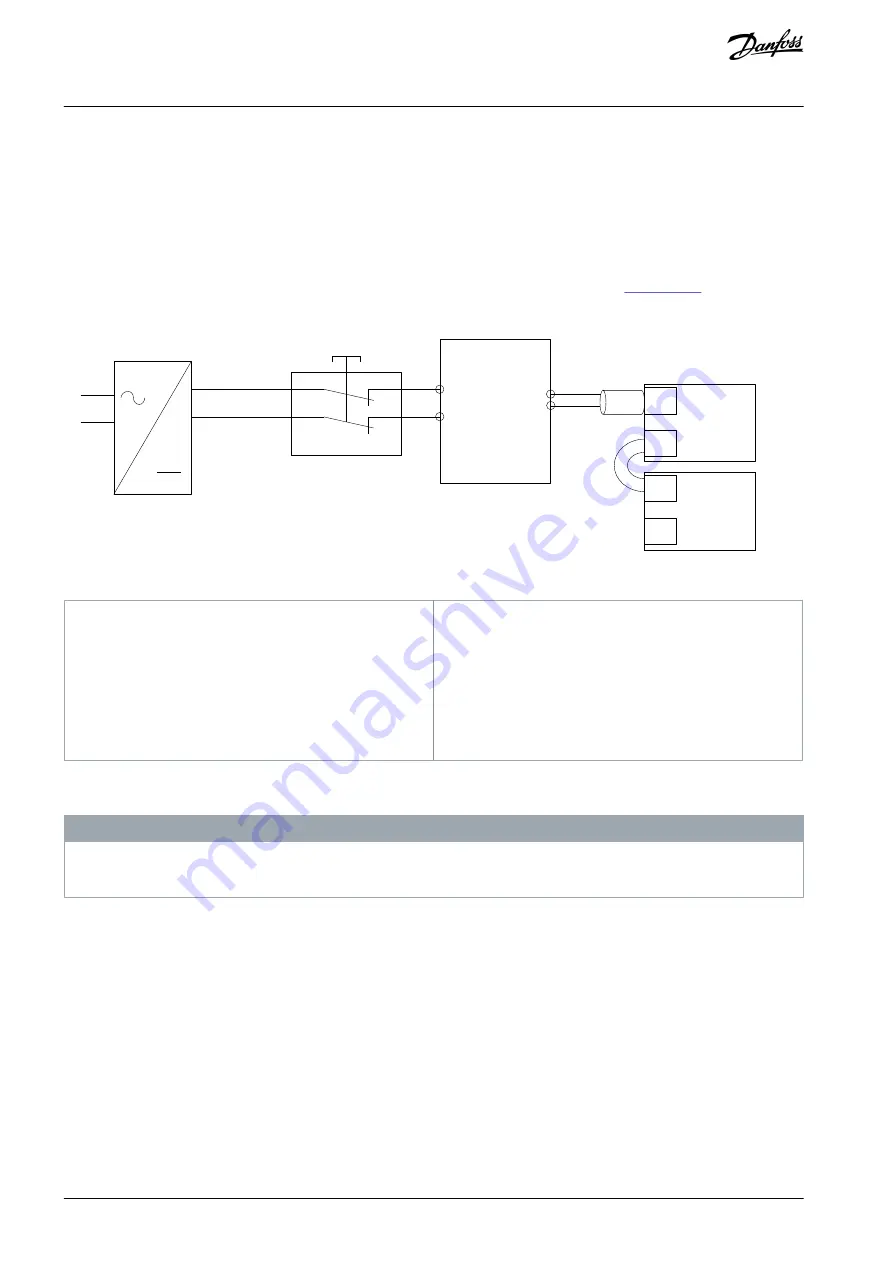
•
•
•
•
•
-
-
-
-
-
8.6.1 Protective Measures
Install the system modules in an IP54 cabinet as per IEC 60529 or in an equivalent environment. A higher IP protection may be
necessary for certain applications.
If external influences can affect the motor axis, for example suspended loads, use additional measures, such as a safety holding
brake, to eliminate hazards.
8.7 Application Example
An example of an application that can be put in Safe Torque Off mode by a safety circuit is shown in
.
Select the safety switch devices in accordance with the requirements of the application.
+24 VDC
GND
e30bg273.10
8a
8b
5
3
4
2
1
X1
X2
X1
X2
9
7
6
Illustration 56: Application Example: Safe Torque Off Function
1
24 V DC supply
2
Safety device
3
Emergency stop button
4
Safety device contacts
5
Decentral Access Module (DAM 510)
6
Hybrid cable
7
Feed-in cable
8a
Servo drive
8b
Servo drive
9
Loop cable
8.8 Commissioning Test
N O T I C E
Perform a commissioning test for the whole servo system after installation of the STO function, after every change to the
installed function, or after a safety fault.
There are 2 ways to implement the commissioning test depending on the method used to program the PLC, however the steps of
the test are the same:
Using the Danfoss Library.
Bit-wise readout of the status.
8.8.1 Commissioning Test using Libraries
Depending on the application, 1 or both of the following libraries are required to program the commissioning test:
Danfoss Library
MC_ReadAxisInfo_DDS
MC_ReadStatus_DDS
MC_ReadAxisError_DDS
MC_Reset_DDS
AQ377148425069en-000101
/ 130R1213
92 | Danfoss A/S © 2023.08
Safety Concept
VLT® Servo Drive System ISD 511
Operating Guide