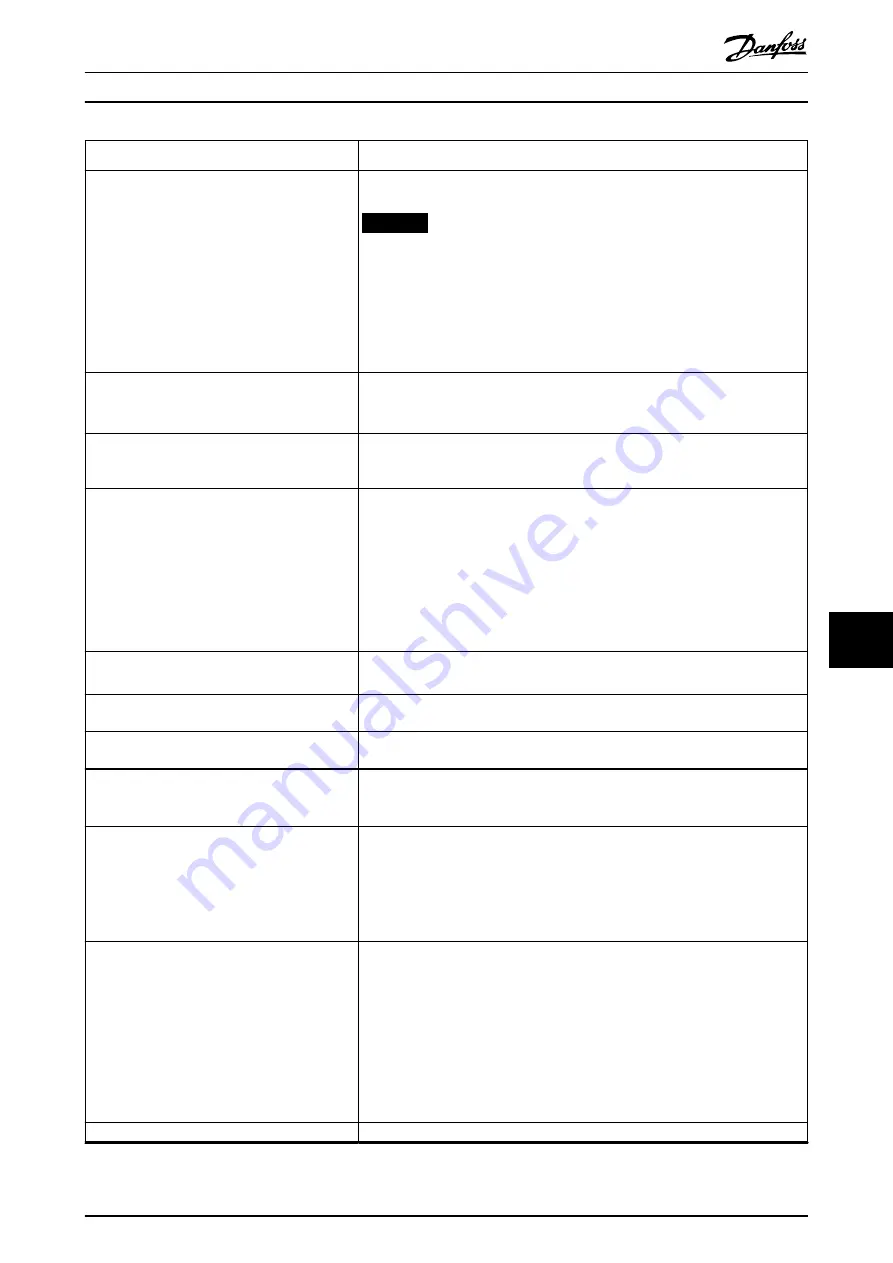
Symptom
Probable cause
Motor does not reach full speed.
•
If the start current is too low, the motor does not produce enough torque to
accelerate to full speed. The soft starter may trip on excess start time.
NOTICE
Make sure that the motor starting parameters are appropriate for the
application and that the intended motor starting profile is used. If
parameter 3-3 Input A Function
is set to
Motor Set Select
, check that the
corresponding input is in the expected state.
•
Check if the load is jammed. Check the load for severe overloading or a locked
rotor situation.
Erratic motor operation.
•
The SCRs in the soft starter require at least 5 A of current to latch. If testing the
soft starter on a motor with full load current less than 5 A, the SCRs may not
latch correctly.
Erratic and noisy motor operation.
If the soft starter is connected to the motor using inside delta configuration, the soft
starter may not be detecting the connection correctly. Contact the local Danfoss
supplier for advice.
Soft stop ends too quickly.
•
The soft stop settings may not be appropriate for the motor and load. Review the
settings of
-
Parameter 1-10 Stop Mode
.
-
Parameter 1-11 Stop Time
.
-
Parameter 7-10 Stop Mode-2
.
-
Parameter 7-11 Stop Time-2
.
•
If the motor is lightly loaded, soft stop has limited effect.
Adaptive control, DC brake, and jog functions not
working.
•
These features are only available with in-line installation. If the soft starter is
installed inside delta, these features do not operate.
A reset does not occur after an auto-reset when
using a remote 2-wire control.
•
Remove and reapply the remote 2-wire start signal for a restart.
Remote start/stop command overrides auto-start/
stop settings when using remote 2-wire control.
•
Only use auto-start/stop in auto-on mode with 3-wire or 4-wire control.
After selecting adaptive control, the motor used an
ordinary start and/or the 2
nd
start was different
from the 1
st
.
•
The 1
st
adaptive control start is
Current limit
. The soft starter then learns from the
motor characteristics. Subsequent starts use adaptive control.
Non-resettable
Thermistor Cct
trip, when there is a
link between thermistor inputs 05 and 06, or when
the motor thermistor connected between 05 and
06 is permanently removed.
•
The thermistor input is enabled once a link is fitted and short-circuit protection
has activated.
Remove the link, then load the default parameter set. This disables the thermistor
input and clears the trip.
Place a 1k2
Ω
resistor across the thermistor input.
Turn thermistor protection to
Log only
(
parameter 16-9 Motor Thermistor
).
Parameter settings cannot be stored.
•
Make sure to save the new value by pressing [OK] after adjusting a parameter
setting. If pressing [Back], the change is not saved.
•
Check that the adjustment lock (
parameter 15-2 Adjustment Lock
) is set to
Read/
Write
. If the adjustment lock is on, settings can be viewed, but not changed.
Knowing the security access code is necessary to change the adjustment lock
setting.
•
The EEPROM may be faulty on the main control PCB. A faulty EEPROM also trips
the soft starter, and the LCP shows the message
Par. Out of Range
. Contact the
local Danfoss supplier for advice.
The LCP shows message
Awaiting data
.
The LCP does not receive data from the control PCB. Check the cable connection.
Table 10.2 General Fault Messages
Troubleshooting
Operating Guide
MG17K602
Danfoss A/S © 05/2016 All rights reserved.
81
10
10