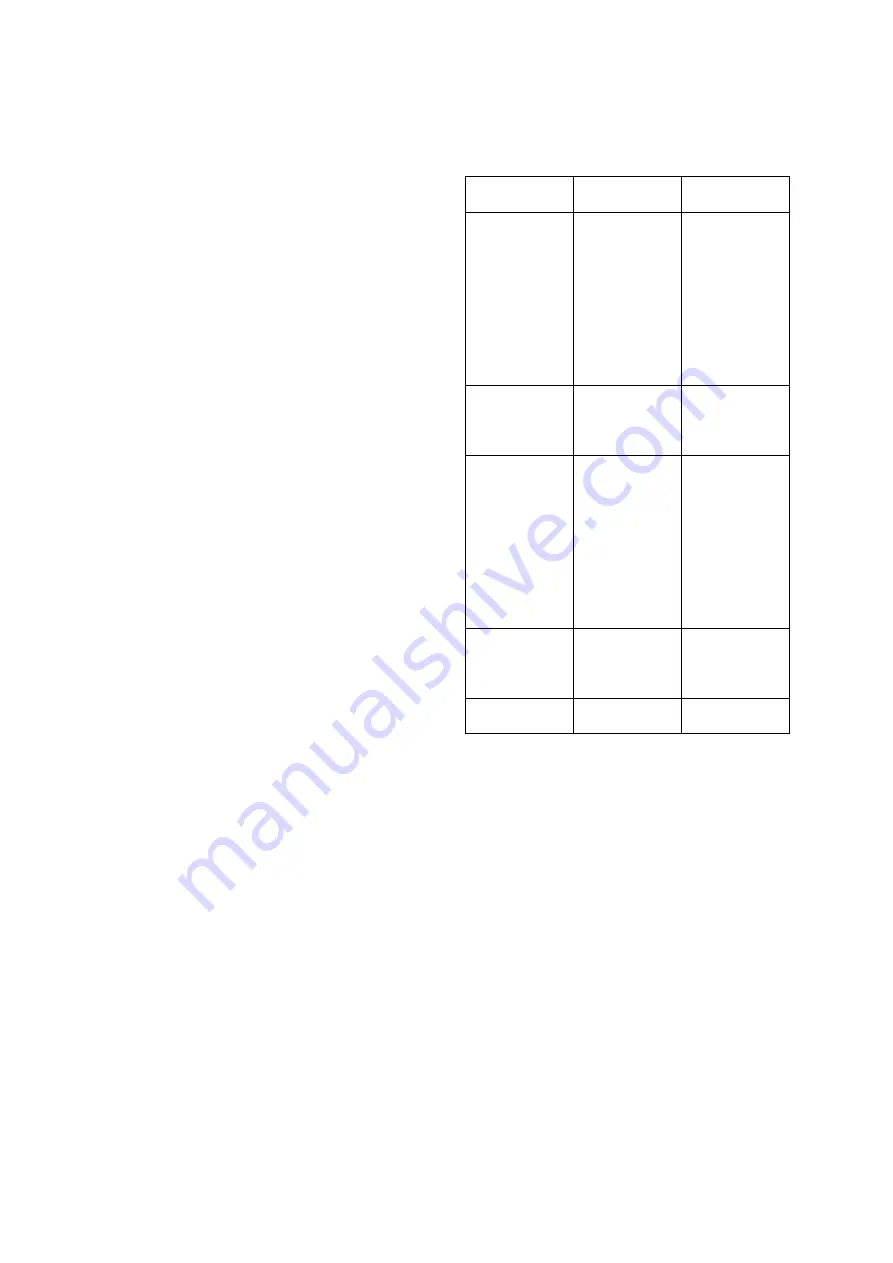
•
Unscrew the plunger retaining cap
from the pump barrel by rotating the
handle.
•
Withdraw the plunger and apply
silicone grease to the O-ring.
•
When re-assembling ensure the O-ring
is not trapped between the outer edge
of the plunger moulding and the inside
of the pump barrel.
Pump non-return valve:
(situated at the bottom of the pump barrel)
•
This stops the compressed air in the
container from escaping back into the
pump.
•
If it is faulty, the unlocked pump handle
will rise when the container is
pressurised.
•
To remove the valve, lift the edge of
the valve and pull. ( take care not to
damage the sealing face of the barrel).
•
To replace, place the valve over the
centre hole and push down firmly.
Pump barrel sealing rings:
•
These make an air tight seal between
both the pump barrel and adapter;
•
Also between the adapter and
container when both are screwed
down tight.
•
To check this, turn the pressurised
sprayer upside down and if there is a
leak, liquid will be forced from the
joints.
Nozzle cap:
•
Keep this clean and free from
obstruction.
•
Also, the two swirl grooves at the end
of the lance must be kept clean and
free from sediment to ensure a good
spray pattern.
•
The nozzle O-ring should be kept
lubricated with silicone grease.
Lance:
•
Keep the trigger clean and free from
build up of sediment and chemicals by
regularly flushing through after use.
•
Of necessary remove and clean the
shuttle in the trigger.
Outlet and dip tube:
•
To rewash the outlet or replace the dip
tube, unscrew the hose nut and pull
the outlet spigot and dip tube through
the outlet body.
Winter use:
•
Drain liquid from all parts after use to
prevent damage from freezing.
Annual maintenance:
•
At least once a year thoroughly clean
the whole sprayer and apply silicone
grease to all moving parts.
•
Test with water and if any washer or
seal has perished it must be replaced.
FAULT FINDING CHART
Fault
May be due
to
Remedy
Weak or no
spray
1. insufficient
pressure or
loss of air
2. obstruction
1. if
insufficient
pressure
check
maintenance.
2. if
obstruction
check
maintenance.
Distorted
spray
Partial
blockage in
spindle or
nozzle
Check
maintenance
Leaks
1.build up of
sediment or
foreign
matter on
internal
sealing
surfaces
2. split
sealing ring.
1. check
maintenance
and if
necessary
replace
sealing rings.
2. replace
sealing rings.
Unit will not
function
Swelling of
sealing rings
or total
blockage
Check
maintenance.
Handle rises
Faulty non-
return valve
Check
maintenance
GUARANTEE
Refer to the enclosed guarantee conditions for
the terms and conditions of guarantee.
ENVIRONMENT
Should your machine need replacement after
exceeded use, do not put it in the domestic
waste but dispose of it in an environmentally
safe way.