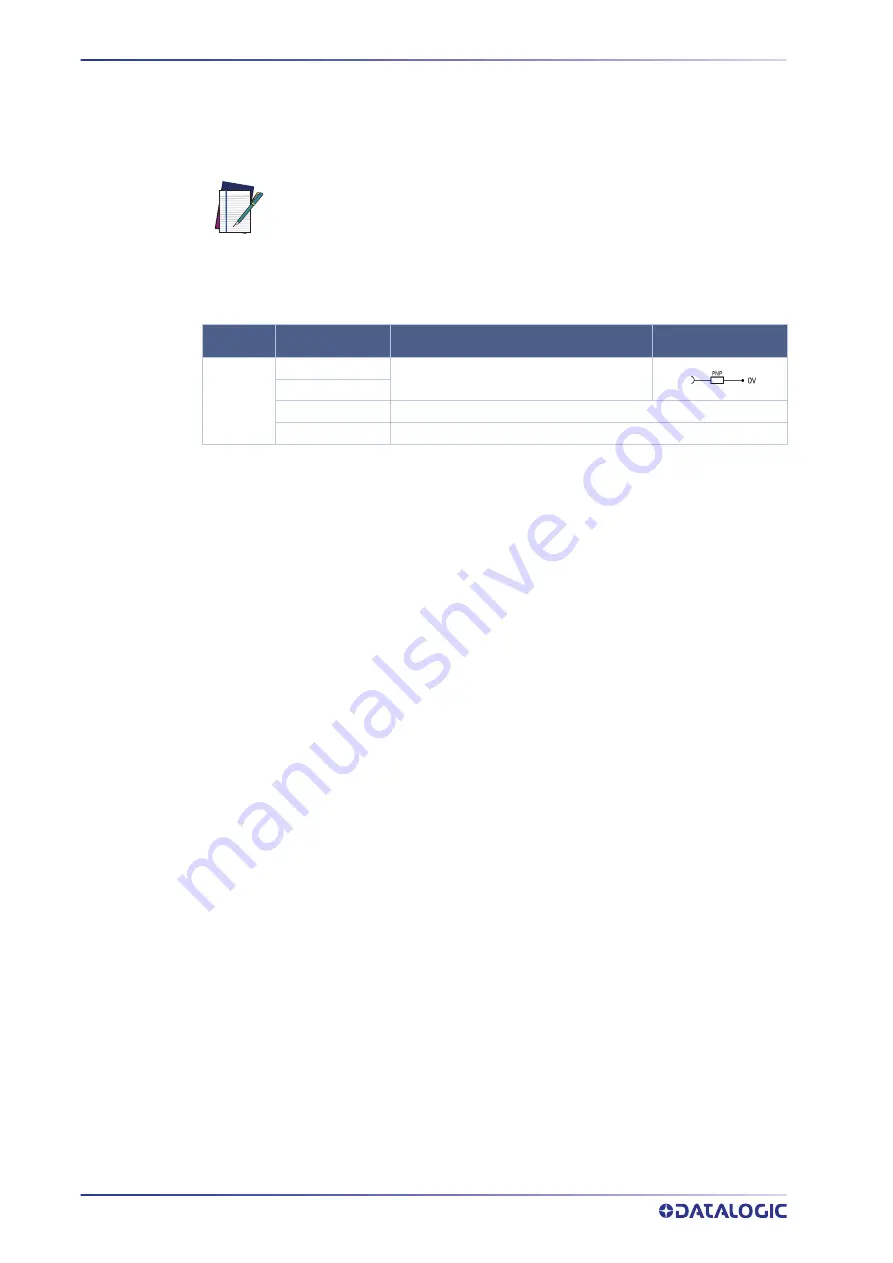
ELECTRICAL CONNECTIONS
48
SAFERY LASER SCANNER
Multi In/Out (17 pole and 17+8 pole models)
The Multi In/Out are signals that can be configured both as inputs and outputs. Laser
Sentinel allows the operator to connect from one to three OSSD pairs; it is possible to
assign to the same electrical pin input and output signals defined as Multi In or Multi
Out.
NOTE
MULTI
IN/OUT
OSSD 31
Activates the third OSSD pair
OSSD 32
MULTI IN
MULTI IN/OUT inputs can be configured as MULTI IN inputs
MULTI OUT
MULTI IN/OUT inputs can be configured as MULTI OUT inputs
The additional OSSDs are aligned to the main outputs OSSD11 and OSSD12
requirements (OSSD11 and OSSD12 are not configurable). If a Multi Out pin
is selected, a second signal linked to it will be automatically configured
(EN 61496). This will ensure that the two Multi Out outputs will be used for
the same purpose.
TYPE
FUNCTION
DESCRIPTION
CONNECTION
Summary of Contents for Laser Sentinel
Page 1: ...Laser Sentinel INSTRUCTION MANUAL Safety Laser Scanner ...
Page 18: ...GENERAL VIEW xviii SAFERY LASER SCANNER ...
Page 140: ...122 SAFERY LASER SCANNER APPENDIX B OVERALL DIMENSIONS LASER SENTINEL STAND ALONE MODEL ...
Page 149: ......
Page 150: ......
Page 151: ......