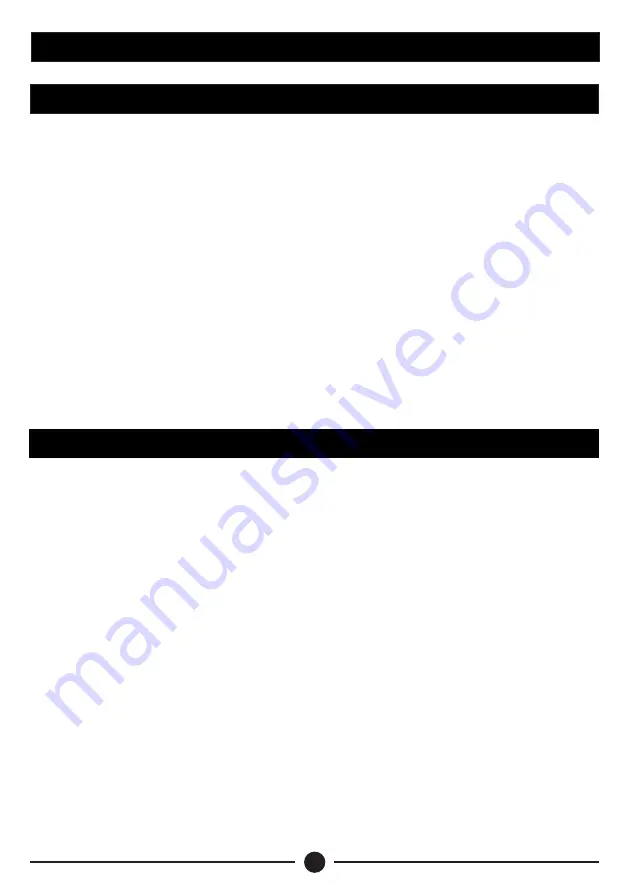
32
5. TERMS OF WARRANTY
If equipment failure occurs in the normal course of service having been competently
installed and when operating within its specified duty limits warranty will be provided as
follows:-
Ÿ
Up to 6 months - The item will be replaced or repaired at no charge.
Ÿ
Over 6 months, less than one year - The item will be replaced or
repaired at a cost to the customer of 50% of the Davis & Shirtliff
market price.
The warranty on equipment supplied or installed by others is conditional upon the
defective unit
being promptly returned free to a Dayliff retailer
and collected
thereafter when repaired. No element of site repair is included in the warranty and any site
attendance costs will be payable in full at standard charegeout rates. Also proof of
purchase including the purchase invoice must be provided for a warranty claim to be
considered.
Ÿ
In lieu of any warranty, condition or liability implied by law, the liability of Dayliff in
respect of any defect or failure of equipment supplied
is limited to making good by
replacement or repair
(at the Distributors discretion) defects which under proper use
appear therein and arise solely from faulty design, materials or workmanship within a
specified period. This period commences
immediately after the equipment has
been delivered to the customer
and at its termination all liability ceases. Also the
warranty period will be assessed
on the basis of the date that the Distributors is
informed of the failure
.
Ÿ
The warranty applies solely to equipment supplied and no claim for
consequential damages
, however arising, will be entertained. Also the warranty
specifically excluded defects caused by fair wear and tear, the effects of careless
handling, lack of maintenance, faulty installation, incompetence on part of the
equipment user, Acts of God or any other cause beyond the Distributors reasonable
control. Also, any repair or attempt at repair carried out by any other party
invalidates
all warranties.
i) General Liability
ii) Standard Warranty