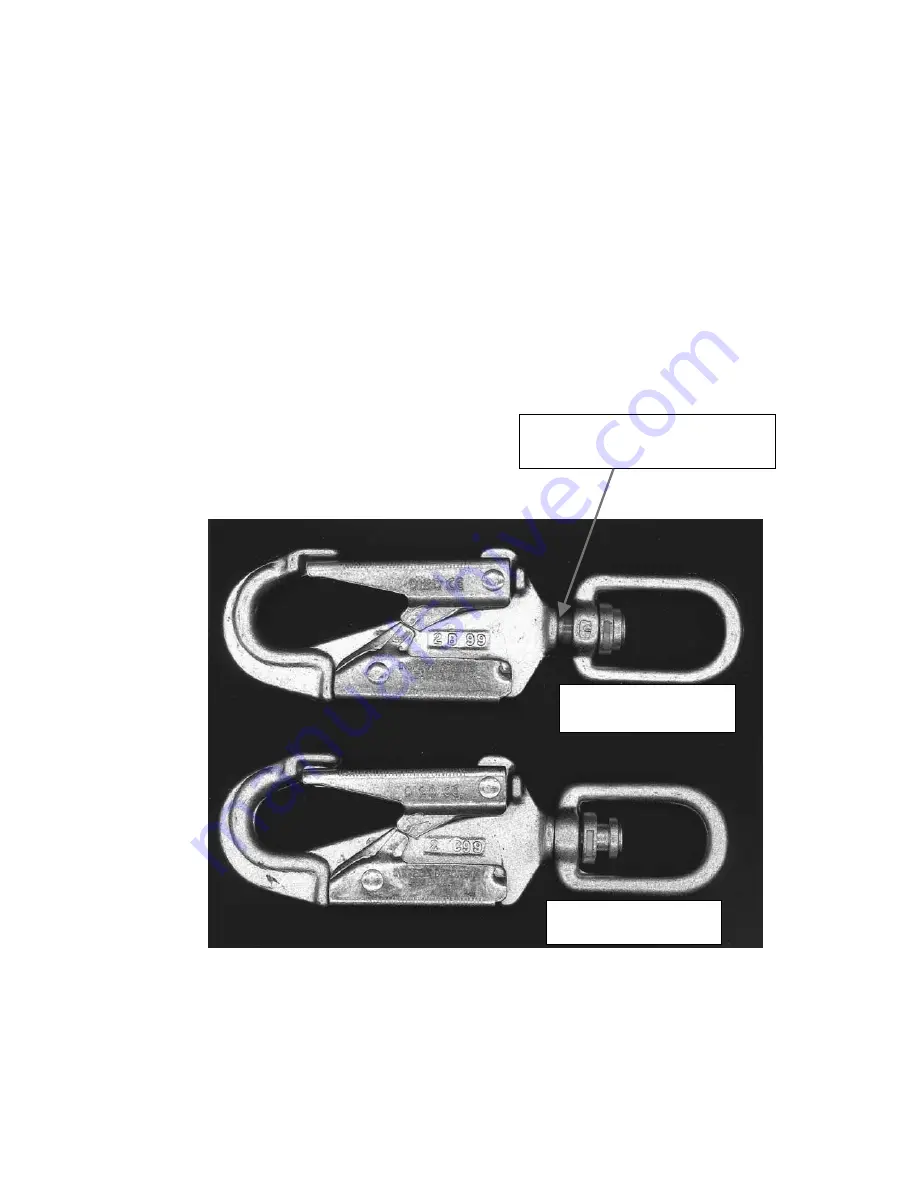
3.con’t
Starting
in
September of 2000
, new
UCL Safety Systems Lifeline assemblies will
incorporate a double-locking swivel snap with a
built in overload indicator. These snaps are
designed to visually identify lifeline assemblies
that have been subjected to loading in excess
of double the winch’s rated working load limit of
310 lbs.
Any winch on which the overload indicator has
been activated must be removed from service
immediately and inspection, repair, and re-
certification.
All warranties and liabilities shall be void for
winches on which the overload indicator has
been activated.
Exposed Red Overload
Indicator
Activated Snap
Indicator
Un-Activated Snap
Indicator
Figure 20 Load Indicator Double Locking Snap
29