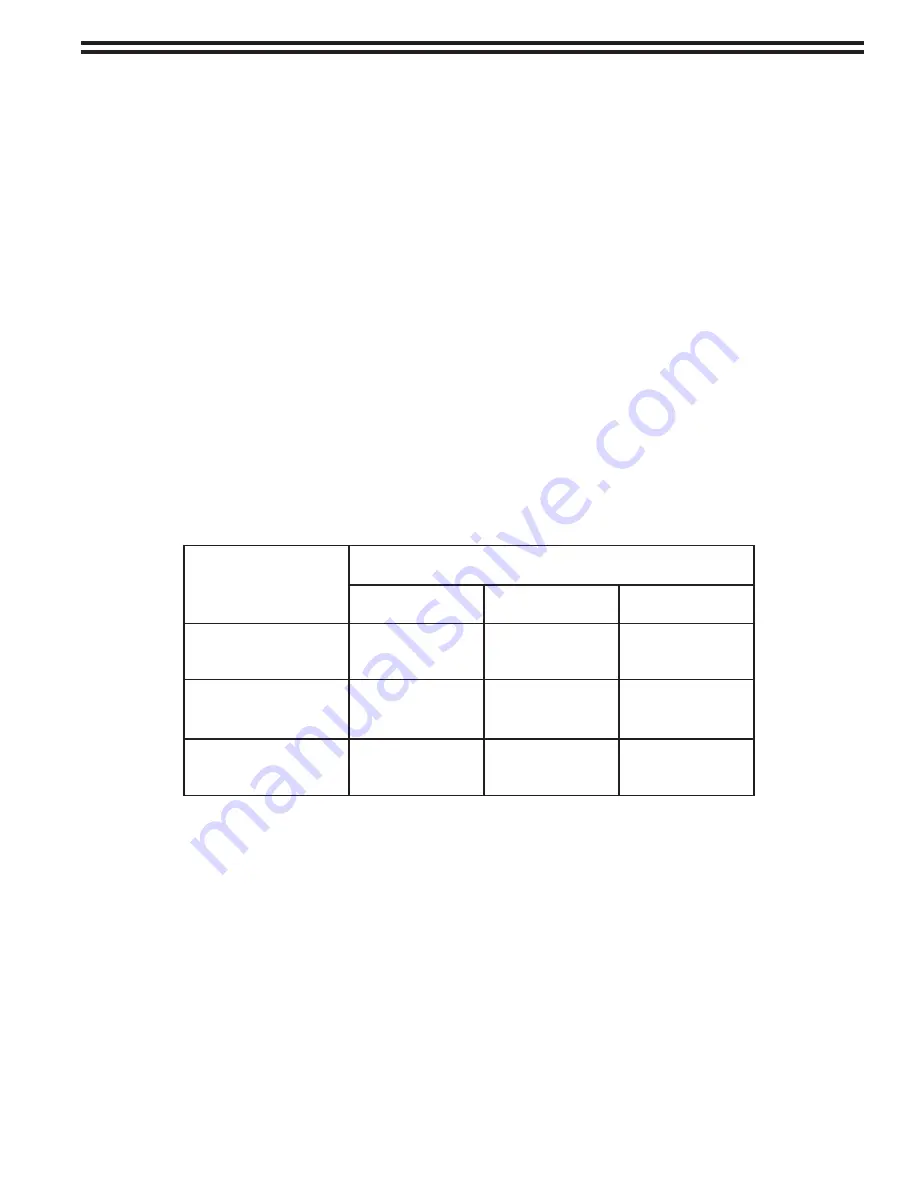
- 7 -
115.6031.0
Liquid Chemical
Being Handled
Electric Immersion Heater
12 kW
15 kW
18 kW
Chlorine
6000 lb/day
120 kg/h
8000 lb/day
160 kg/h
12000 lb/day
227 kg/h
Suflur Dioxide *
4500 lb/day
85 kg/h
5900 lb/day
115 kg/h
7500 lb/day
140 kg/h
Ammonia
1500 lb/day
30 kg/h
2000 lb/day
40 kg/h
2500 lb/day
50 kg/h
TABLE 1-1. Vaporizer Capacity
* In order to attain the referenced capacities for Sulfur Dioxide, the following conditions must exist:
The Vaporizer must be clean and have an ambient temperature of 70°F.
Inlet pressure must be greater than 50 psi.
Piping between the pressure reducing and shut off valve, and the Vaporizer should be short and fully insulated.
Controlled continuous, minimum make-up water must be provided.
1 INTRODUCTION
1.1 General Description
CAPITAL CONTROLS® Series 71V3B Electrically Heated Vaporizers are used to convert liquid Chlorine, Sulfur Dioxide
or Ammonia, as specified at time of purchase, into a superheated gaseous state. The Vaporizer consist of a vaporizing
chamber housed within a self-standing vented water chamber heated by an integrally mounted electric immersion
heater. The Vaporizers are equipped with controls and gauges to provide safe operation under normal conditions and
close supervision.
Functionally, liquid chemical from the supply system is directed into the bottom of the vaporizing chamber, absorbs
heat from the hot wall of the chamber, is converted from liquid into gas, and is discharged through the gas outlet
opening at the top of the chamber to the gas handling components of the system requiring the gas.
The maximum capacity of these Vaporizers, all similar in design and construction, is related to the liquid chemical
being handled and the rating of the electric immersion heater. These capacities are listed in Table 1-1.
WARNING: All components of the Vaporizer System are constructed of materials capable of with standing the
corrosive action of the particular gas for which the system has been specified. Never use any component for
handling a gas different from which it has been purchased.
Summary of Contents for Capital Controls 71V3B Series
Page 1: ... 1 115 6031 0 Instruction Manual Series 71V3B Electrically Heated Vaporizer CAPITAL CONTROLS ...
Page 9: ... 9 115 6031 0 Figure 1 Sectional Diagram ...
Page 17: ... 17 115 6031 0 Figure 4 Outline Mounting Dimensions 12 kW 15 kW Heaters ...
Page 18: ...115 6031 0 18 Figure 5 Outline Mounting Dimensions 18 kW Heater ...