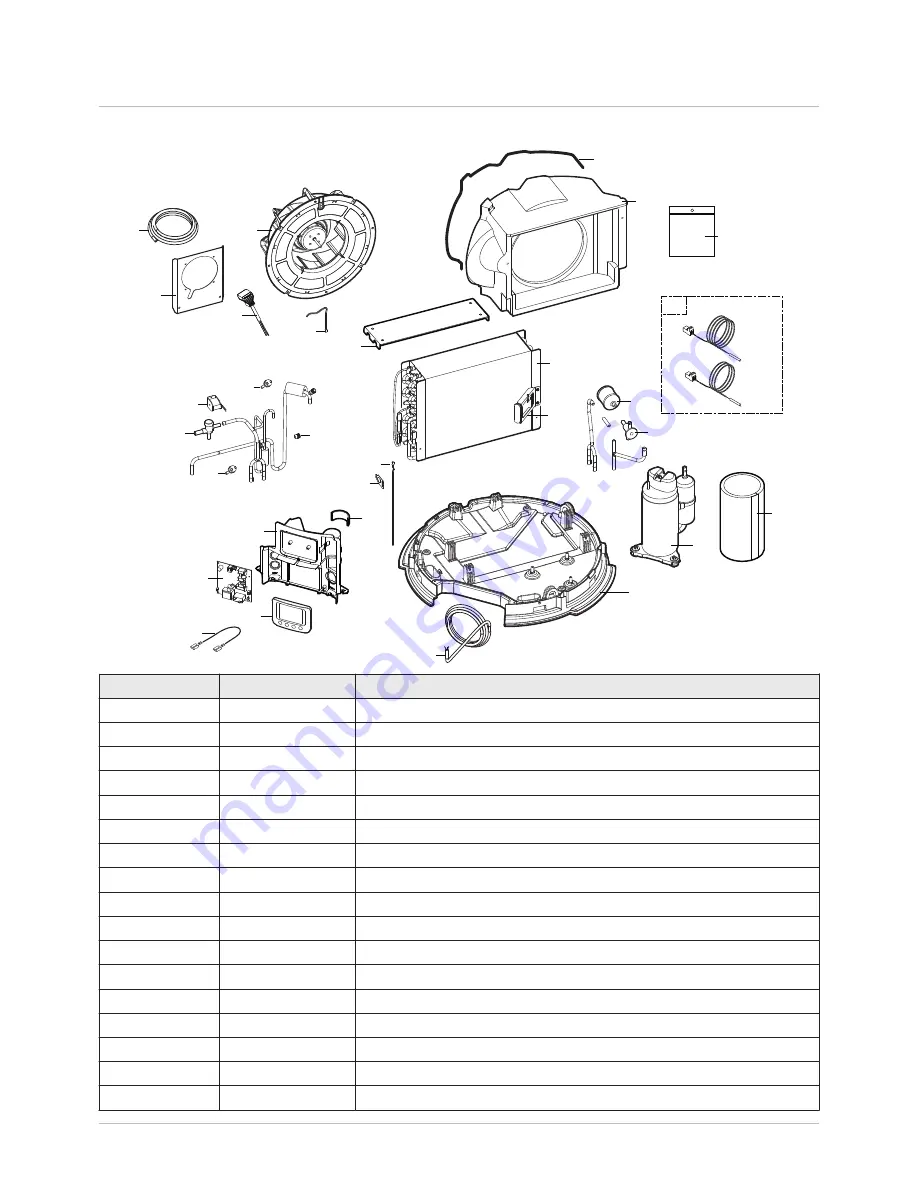
10.3 Spare parts list (from January 2016)
Fig.59
Heat pump
MW-1000419-2
8
21
16
22
19
13
1
18
5
15
3
14
6
2
2
12
17
11
4
7
10
4
20
23
25
24
26
27
28
29
Markers
References
Descriptions
1
SFH41000
Base frame
2
7606446
Sensor harness
3
7611992
Cabled high pressure pressure switch
4
SFH32178
Main electrical harness
5
SFH24053
Coil
6
SFH40173
Sensor bracket
7
SFH31034
Control module
8
SFH20050
Compressor
10
SFH33170
Earthing connector
11
SFH37008
Motorised fan
12
7641131
Control system PCB
13
SFH23108
Expansion valve
14
SFH24052
Solenoid valve
15
SFH22234
Low pressure pressure switch
16
SFH21038
Filter drier
17
SFH40172
Fan bracket
18
SFH41001
Bracket for control panel
10 Spare parts
300026515 - v09 - 25072017
65