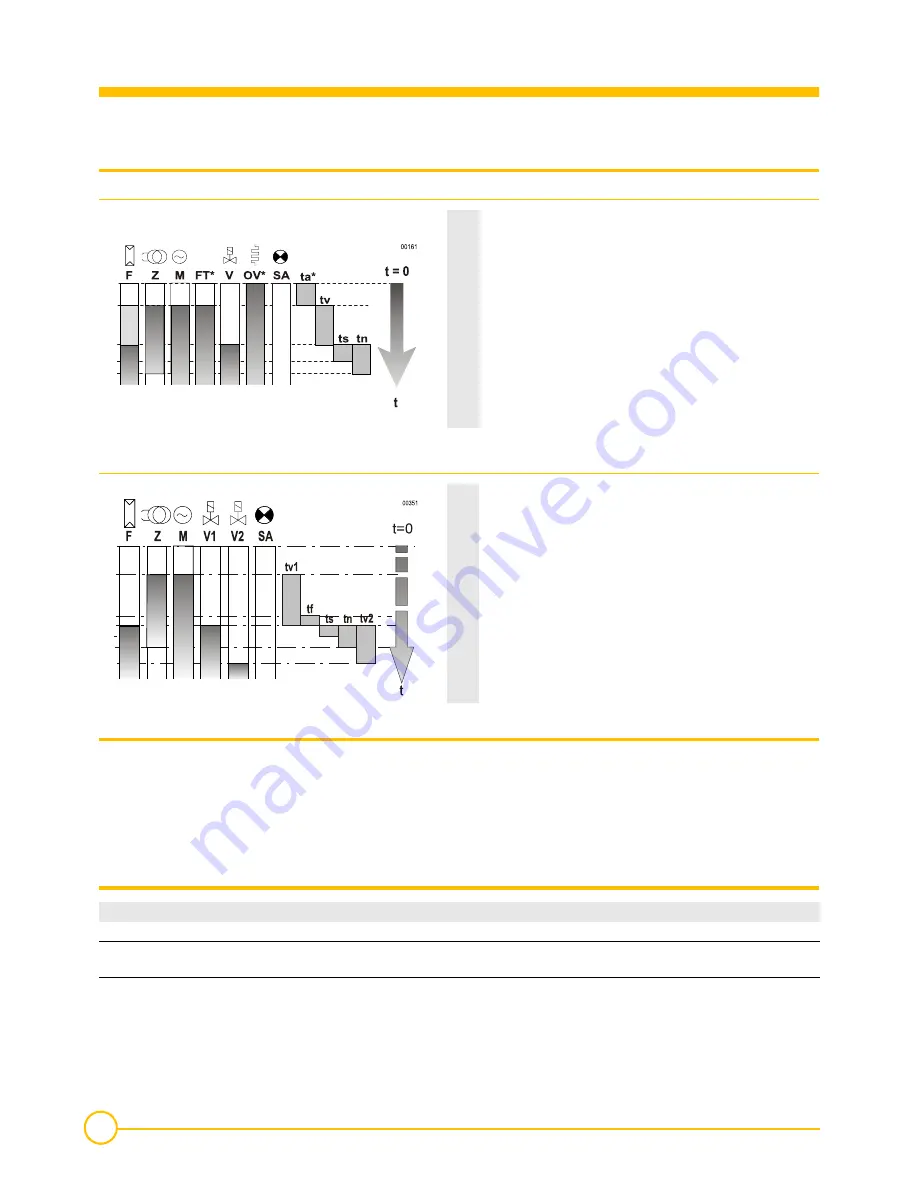
14
11/2010 - 300003201-001- F
M 300 S
Command and safety box
The command and safety box is a safety device which must only be stacked on the base or removed when the current has been
switched off by the main heating installation switch. The command and safety box is a safety device which must not be opened.
1 Operating cycle
TF 874 - M 301 S
DKO 976 - M 302 S
2 Safety (For DKO 976 only)
The DKO 976 command box is operated by a microprocessor.
In the event of a disturbance, the LED is lit for 10 seconds, then the signal is switched off by a disturbance code, indicating the nature of the
fault. Breakdown diagnoses are indicated in the table below.
Malfunction description code
3 Diagnosing breakdowns (For DKO 976 only)
SATROPEN is a pocket terminal displaying disturbances and the intensity of the flame signal. It is available as an option.
F
Flame detection
Z
Ignition
M
Burner motor
FT*
Unblocking the fuel heater
V
Solenoid valve
OV*
Fuel pre-heater
SA
External breakdown indicator
ta*
Fuel heater reheating time: 55
70 s
tv
Pre-ignition and preventilation time: 12 s
ts
Safety time: 10 s
tn
Post-ignition time: 20 s
* except M 301 S/M 302 S
F
Flame detection
Z
Ignition
M
Burner motor
V1
Solenoid valve speed 1
V2
Solenoid valve speed 2
SA
External breakdown indicator
tv1
Pre-ignition and preventilation time: 15s
tv2
Speed timer 2: 20s
ts
Safety time: 5s
tn
Post-ignition time: 7s
tf
Surveillance time for flare: 5s
Short press
Long press
.
Short pause
--
Long pause
Error code
Type of fault
Cause of fault
Disturbance occurrance while in safety time
No flame detection
Unwanted light during preventilation
Unwanted light
Cell defective
--
Manual or external disturbance
External fault