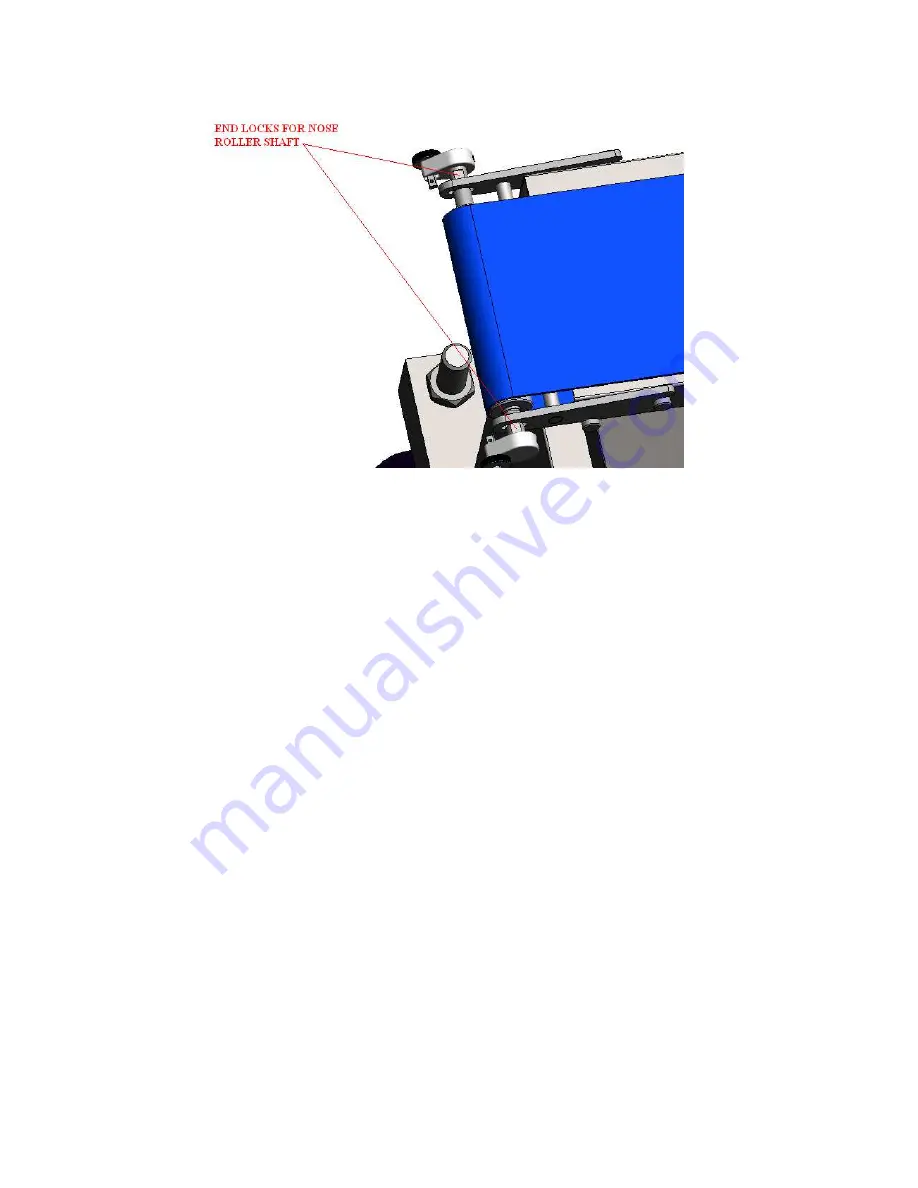
Position the chosen paddles onto the paddle shaft at the top of the machine, ensuring the
keyways are aligned, and secure in place with paddle knob.
Ensure the hopper sealing ring is pressed firmly into its retaining slot in the machine top.
Slacken the four hopper securing knobs on the top of the machine. Place the hopper into the
top machined recess on the hopper seal and rotate such that the hopper
securing lugs engage with the threaded studs.
NOTE - The hopper is handed to ensure correct positioning, one of the hopper lugs is longer
than the other three lugs, the threaded studs, (left hand stud as seen below) is set in a different
position to accommodate the longer lug.
Summary of Contents for FORMATIC D12,000
Page 23: ...10 WIRING DIAGRAMS...
Page 24: ......
Page 25: ......
Page 26: ......
Page 28: ......
Page 31: ...12 Dolomite AB Water chiller Installation and Instruction Manual...
Page 39: ...Dolomite AB water chiller top assembly exploded view...