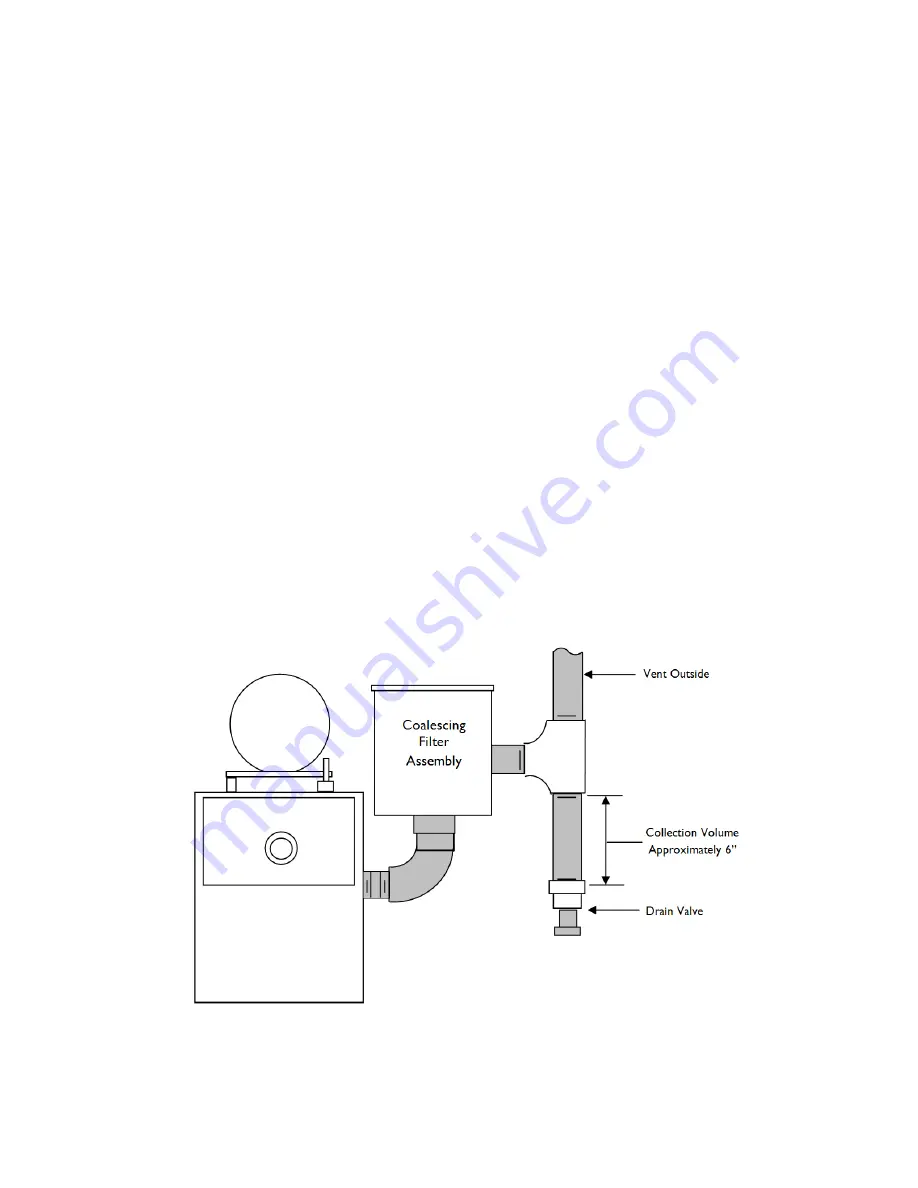
DEKKER Vacuum Technologies, Inc. – HullVac / September 2016
11
Inlet Piping
Note: Install a temporary screen at the pump inlet flange at first start-up to protect the unit
against carryover of pipe debris and welding slag. The screen must be removed after the
initial run in period.
Inlet piping must be welded carbon steel that is vacuum rated and should be at least the size of the pump
inlet. Install the system as close as possible to the process to minimize losses due to the length of the
suction line. If the system has to be installed further away from the process, be sure the inlet piping is
properly sized to minimize the overall line pressure drop. For more information consult your dealer or call
the factory.
If the inlet gas pumped contains dust or foreign particles, a suitable 5 micron (or finer) inlet filter should be
installed at the inlet port. For more information consult your dealer or factory. A vacuum rated isolation
valve should be installed for routine blank-off performance testing and servicing.
Discharge Piping
DEKKER recommends, as a minimum, CPVC discharge piping as discharge temps may exceed +170°F.
CPVC is rated for 200°F max, and PVC is only rated for 140°F max. Discharge piping must be at least the
size of the pump exhaust port. Discharge piping should be routed outside or to a properly sized coalescing
filter. Install a drip leg with a tee on the discharge line to prevent condensables from draining back into the
pump. See the “Discharge Piping Diagram” as shown below. The drop leg volume should be such that it is
unlikely to fill with condensate between routine draining.
It is imperative that no flow restriction be present in the outlet line.
Outlet flow restrictions lead
to excessive power consumption at high inlet pressure as well as overheating which may cause damage to
the pump.
Discharge Piping Diagram