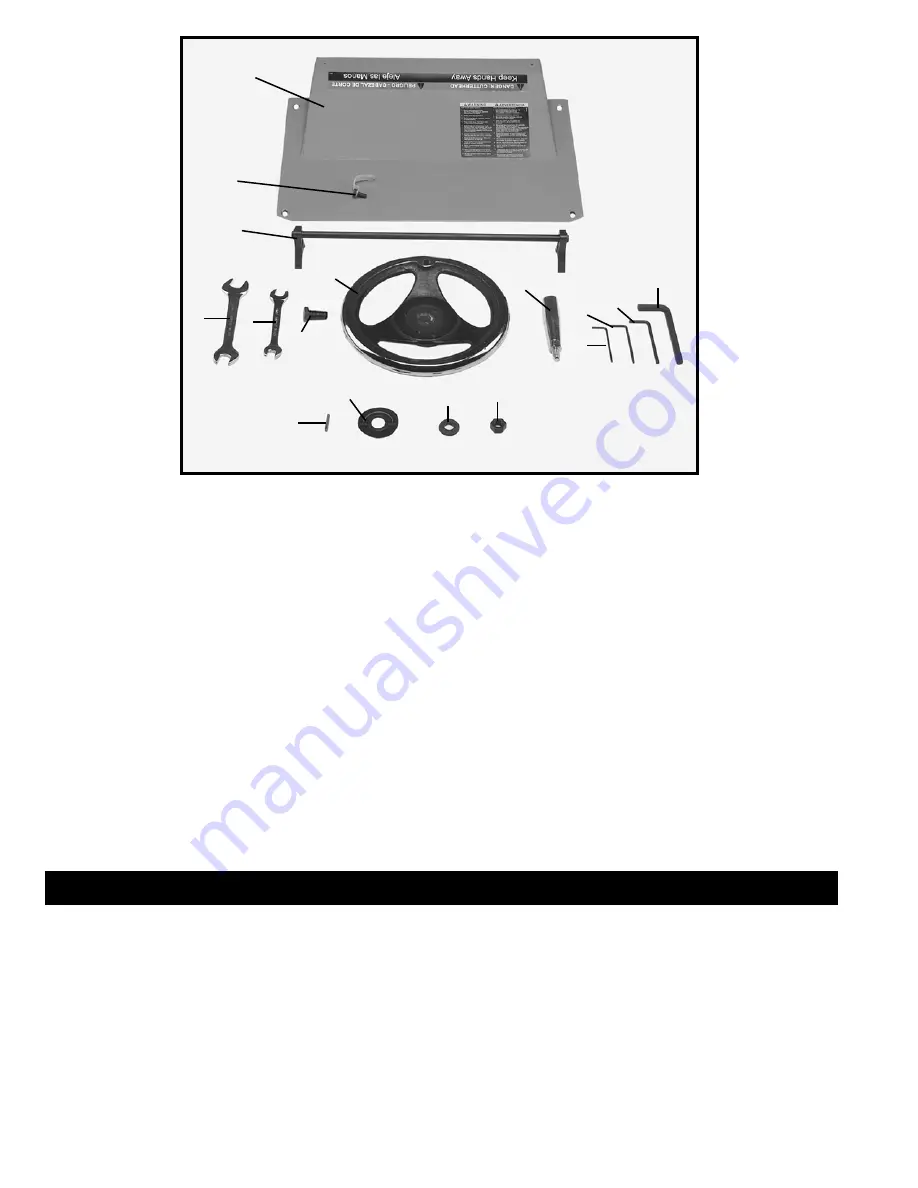
8
1 - Top cover
2 - Cord clamp
3 - Knife setting gage
4 - Open end wrench (14 and 17mm)
5 - Open end wrench (10 and 12mm)
6 - M6x1x16mm hex flange screw (4) - for fastening
top cover to machine
7 - Raising and lowering handwheel
8 - Handle for raising and lowering handwheel
9 - Hex wrench (2.5mm)
10 - Hex wrench (3mm)
11 - Hex wrench (5mm)
12 - Hex wrench (6mm)
13 - Key for raising and lowering handwheel
14 - Decal for raising and lowering handwheel
15 - M10 flat washer for raising and lowering
handwheel
16 - M10x1.5 hex nut for raising and lowering
handwheel
Fig. 3
1
2
3
4
5
6
7
8
9
10
11
12
13
14
15
16
UNPACKING AND CLEANING
Carefully unpack the machine and all loose items from the shipping container(s). Remove the protective coating from
all unpainted surfaces. This coating may be removed with a soft cloth moistened with kerosene (do not use acetone,
gasoline or lacquer thinner for this purpose). After cleaning, cover the unpainted surfaces with a good quality household
floor paste wax.
ASSEMBLY
ASSEMBLY TOOLS REQUIRED
ASSEMBLY TIME ESTIMATE
1) - Open end wrench (10 and 12mm)
- provided
5) - Hex wrench (3mm)
- provided
2) - Open end wrench (14 and 17mm)
- provided
6) - Hex wrench (2.5mm)
- provided
3) - Hex wrench (6mm)
- provided
7) - 10, 12, 14, 17mm Sockets - not provided
4) - Hex wrench (5mm)
- provided
8) - 2 -
2 x 4’s
- not provided
Assembly for this machine takes approximately 2 hours.