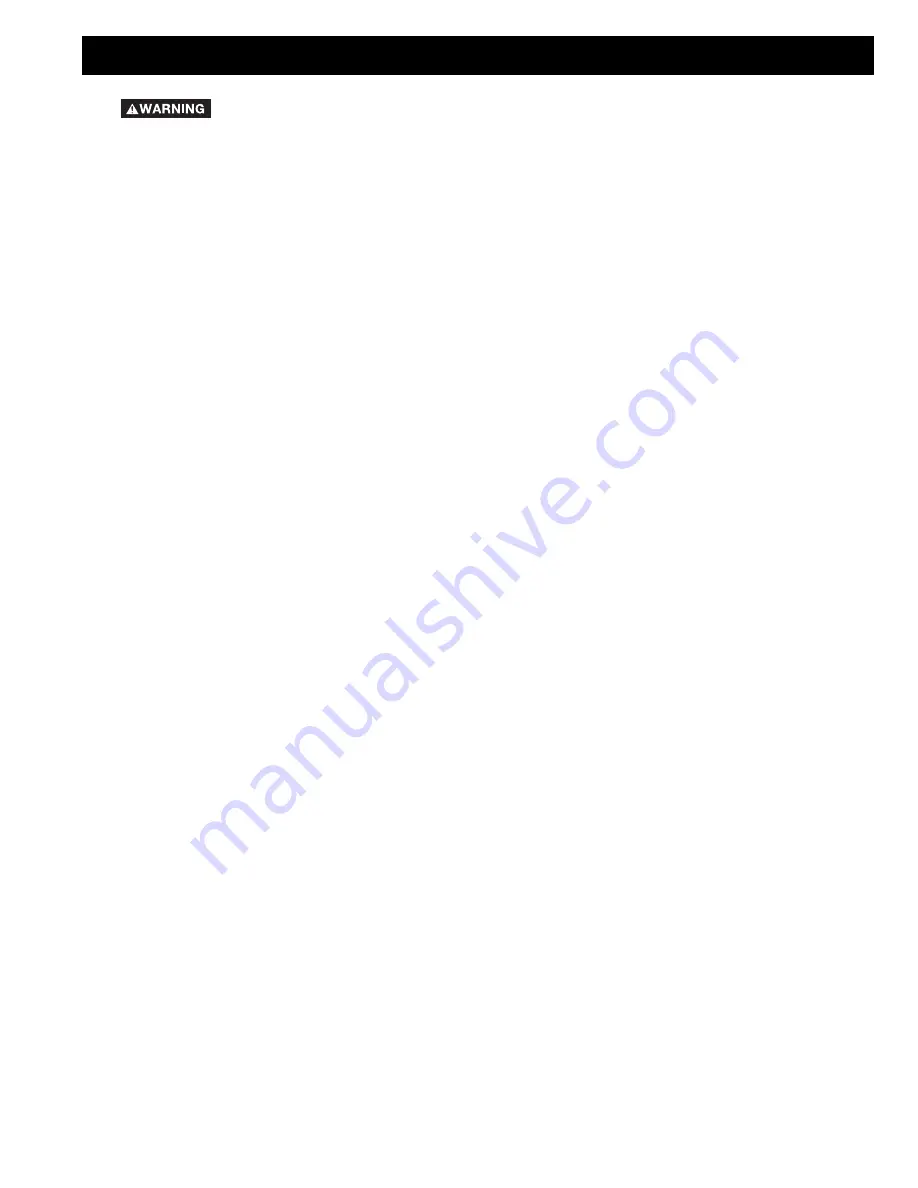
5
FAILURE TO FOLLOW THESE RULES MAY RESULT IN SERIOUS PERSONAL INJURY.
ADDITIONAL SAFETY RULES FOR TABLE SAWS
SAVE THESE INSTRUCTIONS.
Refer to them often and use them to instruct others.
1
.
DO NOT OPERATE THIS MACHINE
until
it is
assembled
and
installed
according to the
instructions.
2.
OBTAIN ADVICE FROM YOUR SUPERVISOR,
instructor, or another qualified person
if you are not
familiar with the operation of this machine.
3.
FOLLOW ALL WIRING CODES
and recommended
electrical connections.
4.
USE THE GUARDS WHENEVER POSSIBLE.
Check
to see that they are in place, secured, and working
correctly.
5.
KICKBACK IS THE NATURAL TENDENCY OF THE
WORKPIECE TO BE THROWN BACK AT THE
OPERATOR
when the workpiece initially contacts the
blade or if the workpiece pinches the blade. Kickback
is dangerous and can result in serious injury.
AVOID KICKBACK by:
A. keeping blade sharp and free of rust and pitch.
B. keeping rip fence parallel to the saw blade.
C. using saw blade guard and spreader for every
possible operation, including all through sawing.
D. pushing the workpiece past the saw blade prior to
release.
E.
never ripping a workpiece that is twisted or
warped, or does not have a straight edge to guide
along the fence.
F.
using featherboards when the anti-kickback device
cannot be used.
G. never sawing a large workpiece that cannot be
controlled.
H. never using the fence as a guide when
crosscutting.
I.
never sawing a workpiece with loose knots or other
flaws.
6.
ALWAYS USE GUARDS, SPLITTER, AND ANTI-
KICKBACK FINGERS
whenever possible.
7.
REMOVE CUT-OFF PIECES AND SCRAPS
from the
table before starting the saw. The vibration of the
machine may cause them to move into the saw blade
and be thrown out. After cutting, turn the machine off.
After the blade has
come to a complete stop, remove
all debris.
8.
NEVER START THE MACHINE
with the workpiece
against the blade.
9.
NEVER
run the workpiece between the fence and a
moulding cutterhead.
10.
CUTTING THE WORKPIECE WITHOUT THE USE OF
A FENCE OR MITER GAUGE IS KNOWN AS
“FREEHAND” CUTTING. NEVER
perform “free-hand”
operations. Use either the fence or miter gauge to
position and guide the workpiece.
11.
HOLD THE WORKPIECE FIRMLY
against the miter
gauge or fence.
12.
CUTTING COMPLETELY THROUGH THE WORK-
PIECE IS KNOWN AS “THROUGH-SAWING”.
Ripping and cross-cutting are through-sawing
operations. Cutting with the grain is ripping. Cutting
across the grain is cross-cutting. Use a fence or fence
system for ripping. DO NOT use a fence or fence
system for cross-cutting. Instead, use a miter gauge.
USE PUSH STICK(S)
for ripping a narrow workpiece.
13.
AVOID AWKWARD OPERATIONS
AND HAND
POSITIONS
where a sudden slip could cause a hand
to move into the blade.
14.
KEEP ARMS, HANDS, AND FINGERS
away from the
blade.
15.
NEVER
have any part of your body in line with the path
of the saw blade.
16.
NEVER REACH AROUND
or over the saw blade.
17.
NEVER
attempt to free a stalled saw blade without first
turning the machine “OFF”.
18.
PROPERLY SUPPORT LONG OR WIDE
workpieces.
19.
NEVER PERFORM LAYOUT,
assembly or set-up work
on the table/work area when the machine is running.
20.
TURN THE MACHINE “OFF” AND DISCONNECT
THE MACHINE
from the power source before
installing or removing accessories, before adjusting or
changing set-ups, or when making repairs.
21.
TURN THE MACHINE “OFF”,
disconnect the machine
from the power source, and clean the table/work area
before leaving the machine. LOCK THE SWITCH IN
THE “OFF” POSITION to prevent unauthorized use.
22.
ADDITIONAL INFORMATION
regarding the safe
and proper operation of power tools (i.e. a safety
video) is available from the Power Tool Institute,
1300 Sumner Avenue, Cleveland, OH 44115-2851
(www.powertoolinstitute.com). Information is also
available from the National Safety Council, 1121 Spring
Lake Drive, Itasca, IL 60143-3201. Please refer to the
American National Standards Institute ANSI 01.1
Safety Requirements for Woodworking Machines and
the U.S. Department of Labor OSHA 1910.213
Regulations.