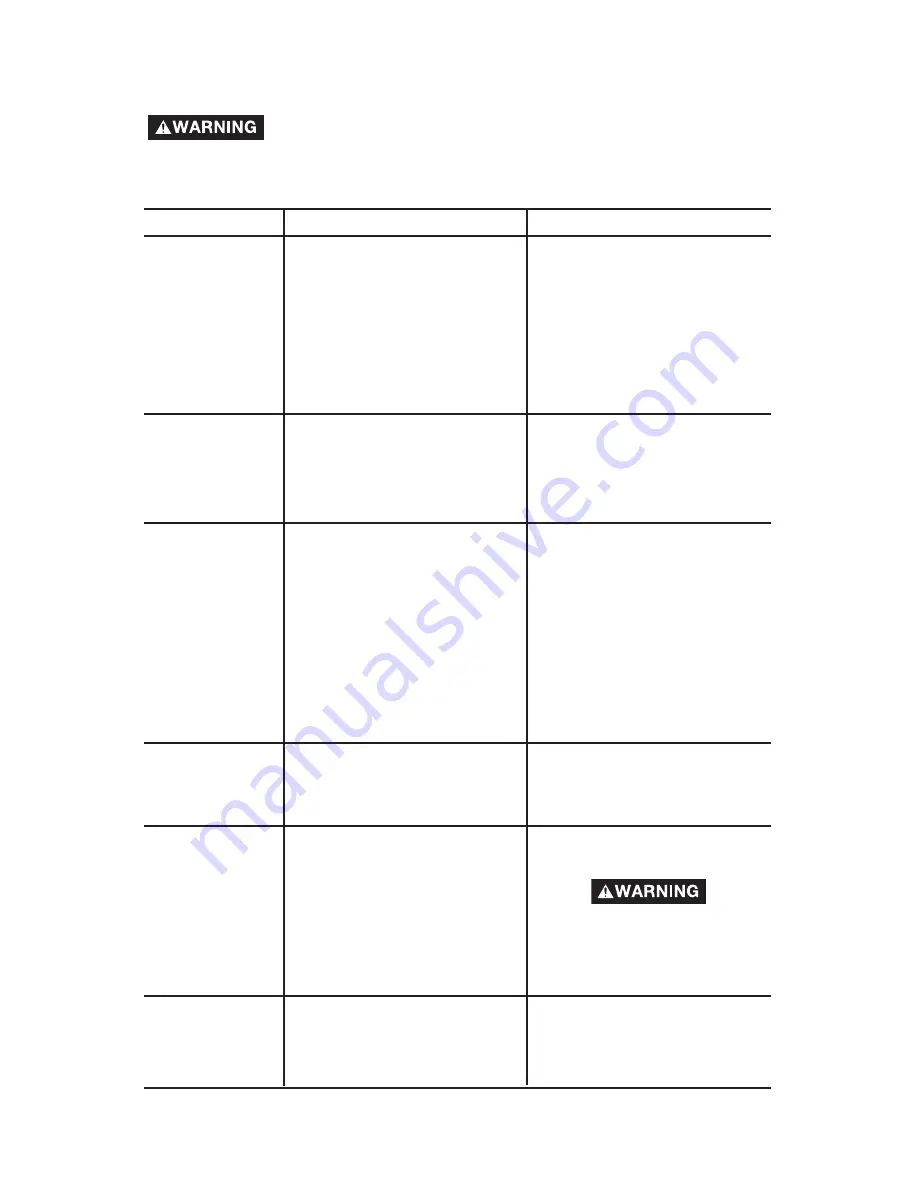
19- ENG
D26195
TROUBLESHOOTING
Performing repairs may expose voltage sources, moving
parts or compressed air sources, moving parts or
compressed air sources. Personal injury may occur. Prior to attempting
any repairs, unplug the air compressor and bleed off all air tank air
pressure.
PROBLEM
CAUSE
CORRECTION
Pressure switch does not
shut off motor when
compressor reaches "cut-
out" pressure.
Pressure switch "cut-out"
too high.
Move On/Auto/Off lever to
the "OFF" position, if the
outfit does not shut off
contact a Trained Service
Technician.
Contact a Trained Service
Technician.
Excessive tank
pressure - safety
valve pops off.
Tube fittings are not tight
enough.
Tighten fittings where air can
be heard escaping. Check
fittings with soapy water
solution.
Do Not
Overtighten.
Air leaks at
fittings.
Air leaks at
pressure switch
release valve.
Defective pressure switch
release valve.
Contact a Trained Service
Technician.
Air leaks in air
tank or at air
tank welds.
Defective air tank.
Air tank must be replaced.
Do not repair the leak.
Do not drill into, weld or
otherwise modify air tank
or it will weaken. The tank
can rupture or explode.
Air leaks
between head
and valve plate.
Leaking seal.
Air leaks at or
inside check
valve
Check valve seat damaged.
A defective check valve
results in a constant air leak
at the pressure release valve
when there is pressure in the
tank and the compressor is
shut off. Replace check
valve. Refer to the "To
Replace or Clean Check
Valve" in the "Service and
Adjustment" section.
Contact a Trained Service
Technician.