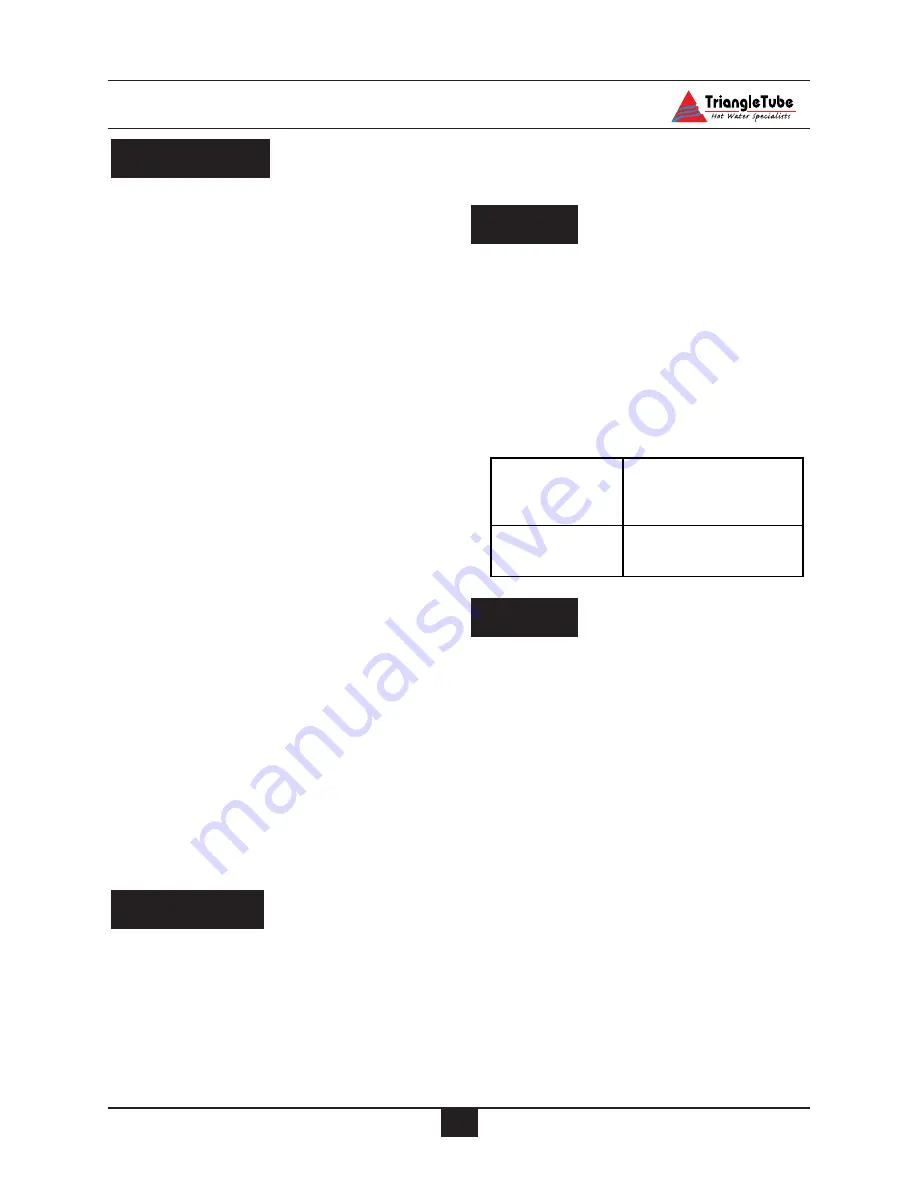
28
Venting and Combustion Air Installation
The total horizontal distance of a vent
plus the horizontal vent connector shall
not be greater than 75% of the vertical
height of the vent.
Vent Connectors
-
When a vent connector must be located
in or pass through an un-conditioned
space, attic or crawl space, that portion
of the vent connector must be listed as
Type B or other approved material hav-
ing equivalent insulation qualities.
-
The minimum clearance to com-
bustibles for single wall vent connec-
tors shall be 6 inches.
-
The minimum clearance to com-
bustibles for Type B vent connectors
shall be 1 inch or per vent manufactur-
er’s instructions.
-
The vent connector shall be installed in
a manner to avoid excessive turns or
other construction features that create
excessive resistance to the flow of the
vent gases.
-
The vent connector should be installed
in a manner without any dips or sags
and should slope upward toward the
vent or chimney at least 1/4 inch per 1
foot.
-
The location of the appliance should be
located as close to the vent or chimney
to maintain the vent connector length as
short as possible.
The maximum horizontal length allow-
able should not exceed 75% of the height
of the vent or chimney assuming no off-
sets in the vertical vent.
-
The entire length of a vent connector
shall be readily accessible for inspec-
tion, cleaning and replacement.
-
The diameter of the vent connector
should not be upsized more than two
sizes greater than the flue outlet diameter.
The minimum recommended vent con-
nector given in Table 1 is only a general
guideline. The vent system must be
designed and installed in compliance
with all applicable codes. Failure to
properly size and install the vent system
could result in severe personal injury,
death or substantial property damage.
There are certain applications for the
PERFORMANCE in which upsizing the
vent connector to 5 inches will not result
in sufficient maximum capacity require-
ments. In these applications the
installer, after consultation with Triangle
Tube Engineering, may upsize the vent
connector to 6 inches provided the vent
connector and vent system are Type B.
Common Venting - Category I
The PERFORMANCE may be vented into a
common vent system using the guidelines and
sizing Tables of the National Fuel Gas Code
NFPA 54 ANSI Z223.1 latest edition.
The PERFORMANCE may also be vented into
a common multi story vent using the guidelines
and sizing Tables of the National Fuel Gas
Code NFPA 54 ANSI Z223.1 latest edition.
NOTICE
WARNING
BEST PRACTICE
BEST PRACTICE
PERFORMANCE
Min. Recommended
Model
Vent Connector
Diameter
PG-25/30
4 inches
PG-35/40/45
5 inches
TABLE 1: Vent Connector Diameter