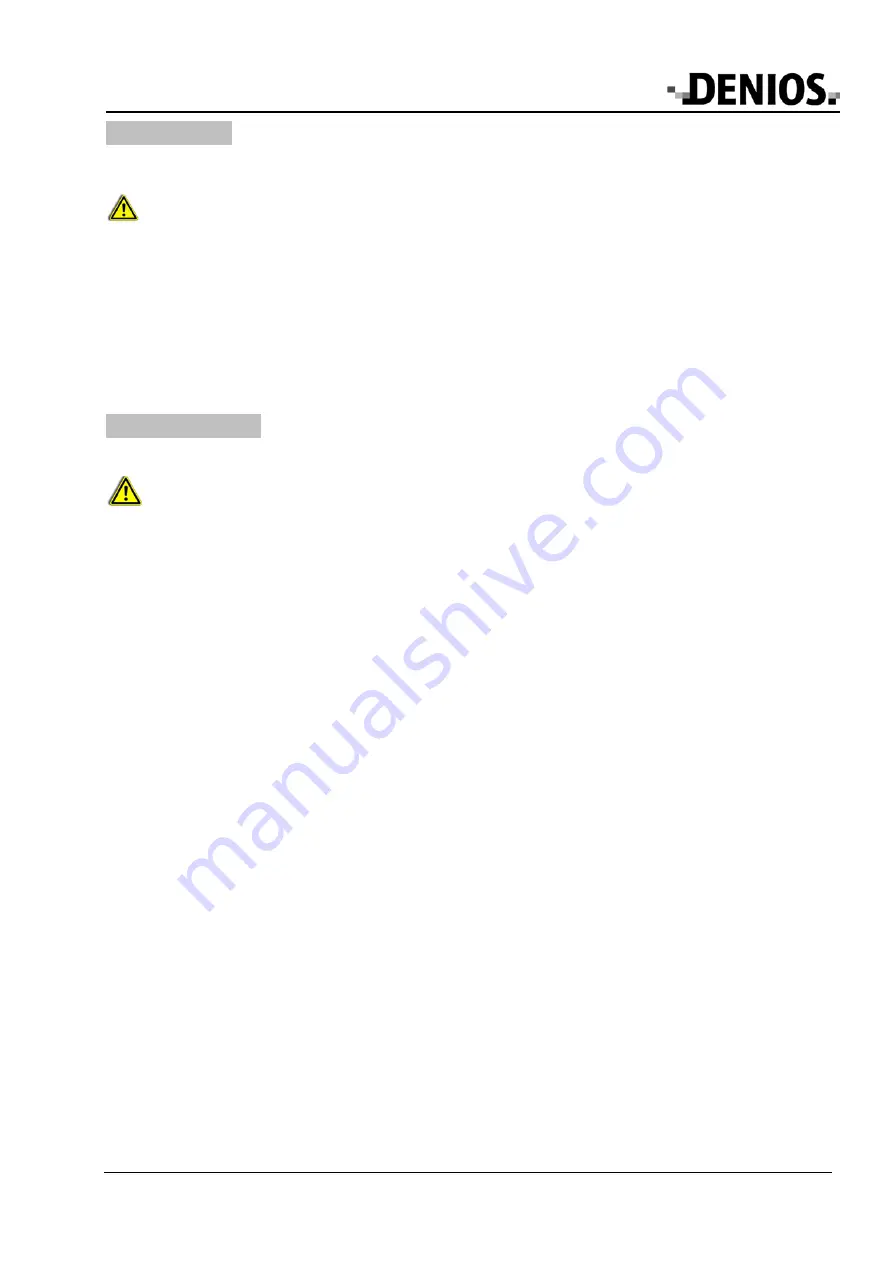
bio.x B200
Page 6 of 12
01/2010
5. Operation
Place the parts to be cleaned in the cleaning basin.
Do not exceed the maximum load of 100 kg!
Activate the ball valve (6.1.) Press the on/off switch (A). The parts are cleaned with a wash brush.
The dirty detergent runs back into the tank via the middle plug outlet where special micro-organisms remove
oil and grease contaminants.
Note:
When interrupting work, do not disconnect the unit from the mains, so the detergent remains warm. The micro-
organisms in the detergent require heat and oxygen to degrade the oil and grease. For this reason, the heat-
ing system maintains the temperature of the detergent at 41º C and an aerator ensures oxygen is permanently
fed to the micro-organisms. If the unit is switched off, or it breaks down for a long period of time, the micro-
organisms become inactive.
6. Maintenance
Warning!
Before starting work on the cleaning table fixtures unplug from the mains!
Test the equipment to ensure the power is off!
The unit can be opened at the side for servicing or to fill the tank with fresh detergent (see point 4.1).
Fill level
Check the fill level regularly so you can refill to make up for any losses through evaporation and removal. The
mark on the back wall of the container shows the maximum fill length. If the minimum fill level (approx .23 cm
below the maximum level) is reached, the pump and the heating system switch off automatically for safety
reasons. The red control display (B) lights up. Please refill enough cleaning fluid so that the optimum fill level
is reached and the maximum mark is not exceeded. The message will disappear once there is enough deter-
gent in the tank.
Additive
More additive should be put in every 6 months to replenish the micro-organisms.
After refilling, the detergent must be left to stand for 24 hours so that the micro-organisms can become active.
It is therefore recommended to refill with the additive before a weekend.
Filter
The washstand is equipped with two filters as standard. A stainless steel perforated filter on the washstand
surface and a synthetic filter for impurities underneath. It is recommended to clean these filters on a daily
basis. To do so, remove the filters from the unit and rinse with water.
172236, 172292, 176074