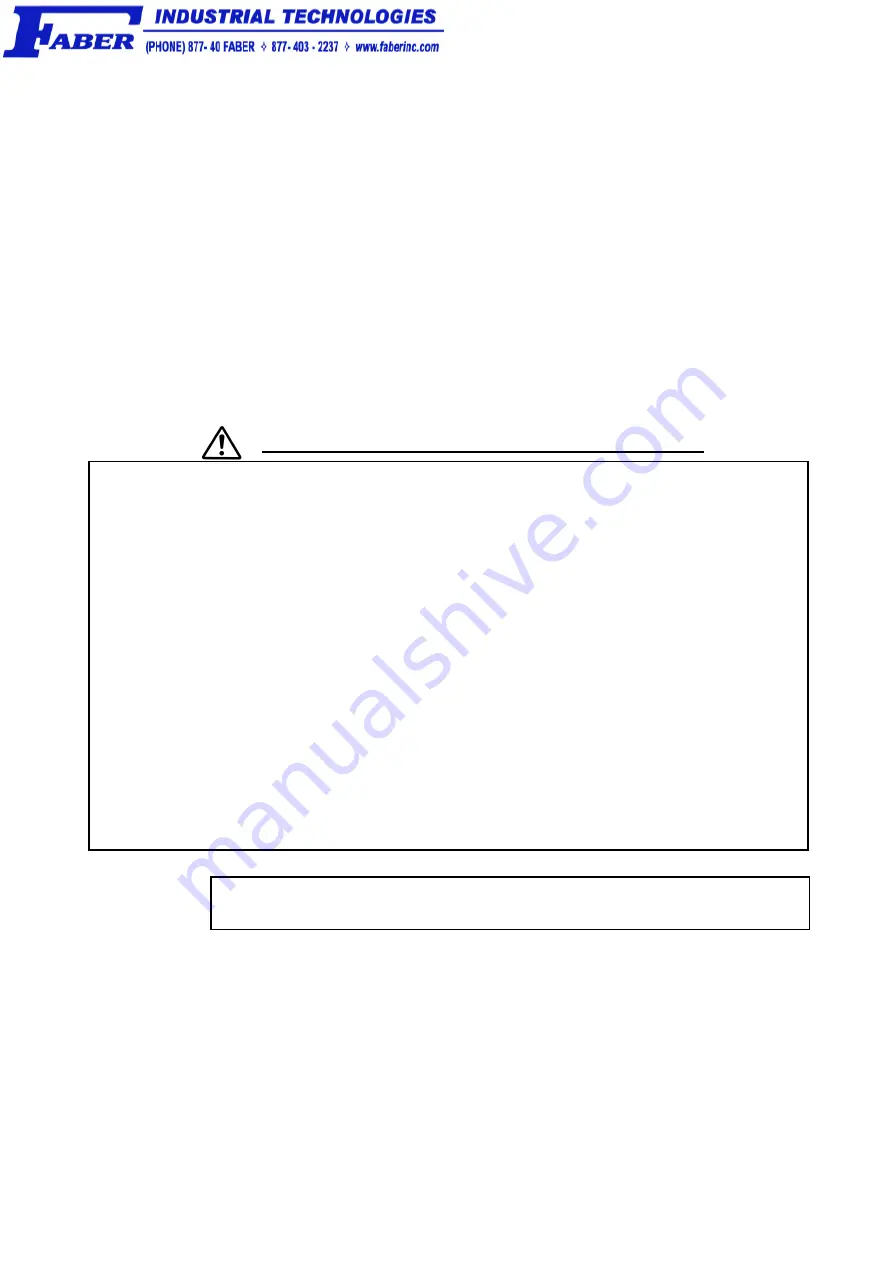
28
2.3
Changing Mechanical Ends to Define New Restricted Space
2.3.1
What is a Mechanical End Change?
In the case of the HS-G series, you may change mechanical ends on the 1st through
3rd (Z) axes.
When the robot leaves the factory, the mechanical ends are set at points 2
to 3
outside the default software motion limits. (Refer to Section 2.2.2 "Software Motion
Limits (Factory defaults)."
Adding mechanical stops to change mechanical ends is called "Mechanical end
change."
Regarding to the additional mechanical stopper installation, you may need to prepare
and install the stopper on your own.
Please contact your DENSO representative for more details.
CAUTIONS IN CHANGING THE MECHANICAL ENDS
1. When changing the mechanical ends, design the mechanical stoppers according to your
usage and manufacture them.
2. After changing the mechanical end, the software motion limits (PLIMs, NLIMs) should be
changed not to interfere the mechanical end at the robot operation.
3. When the robot has collided with a mechanical stopper, contact us for inspection and
repairs before using the robot because the robot may be damaged.
Also because the mechanical stopper designed and made by the customer may be
damaged, do not reuse the mechanical stopper, but replace it before using the robot.
4. The reference drawings described on this manual cannot be covered on the customer’s
usage conditions sufficiently. Design, manufacture and install the mechanical stoppers
according to your usage conditions.
5. The weight addition by the mechanical stoppers may affect the maximum payload.
6. The failures caused by the mechanical stoppers shall not be covered by the warranty even
if the robot is under warranty.
NOTE:
This manual does not include reference diagram of mechanical stoppers.
Please contact your DENSO representative for more details.