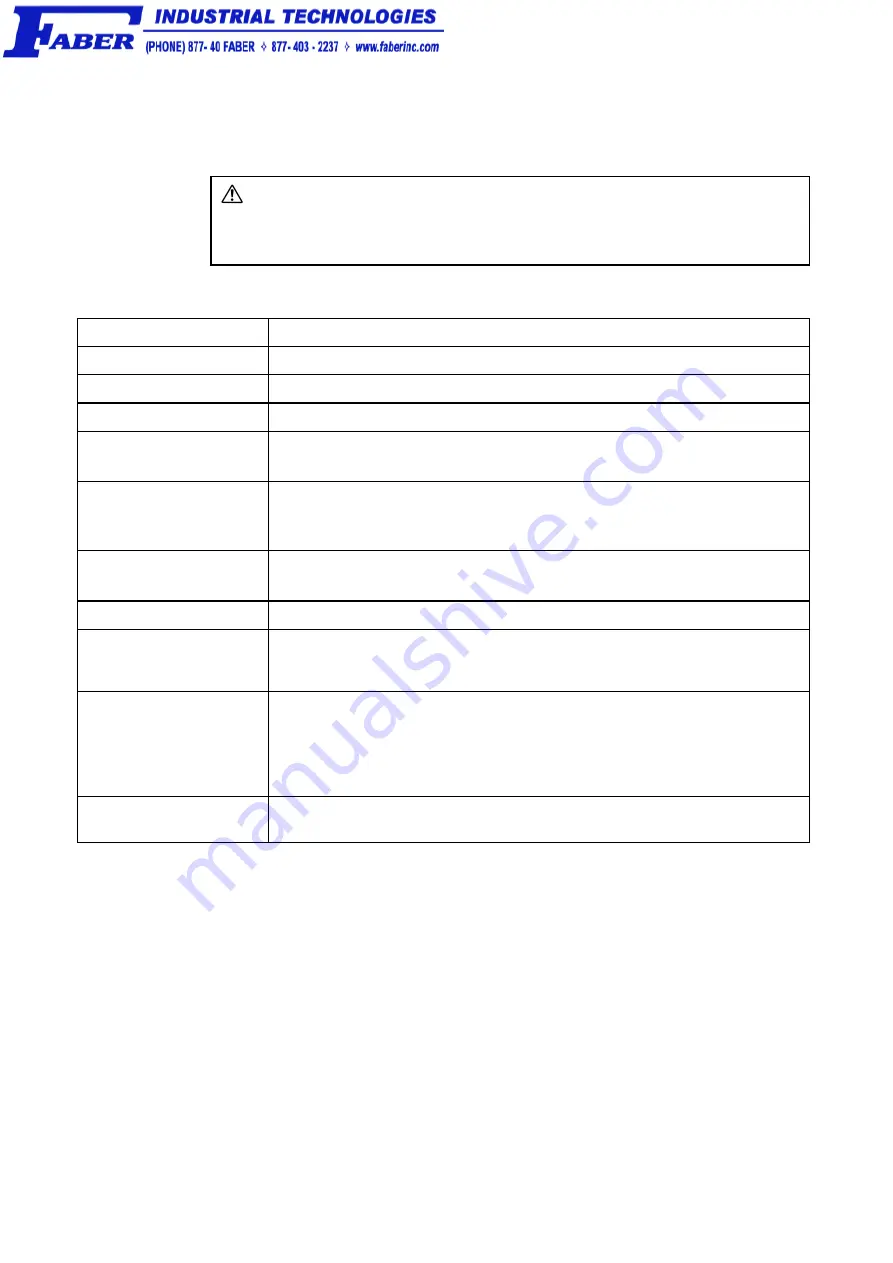
2
1.1.4
Installation Environment of the Robot Unit
The table below lists the installation requirements for the robot unit. Prepare a highly
rigid mount as shown on the next page.
Caution: Do not electric-weld the equipment including the robot. A large
current may flow through the motor encoder or robot controller
resulting in a failure. If electric welding is required, remove the
robot unit and the robot controller from the equipment beforehand.
Installation Requirements for the Robot Unit
Item
Environments and Conditions
Flatness of the mount
0.1/500 mm (See the next page.)
Rigidity of the mount
Use steel materials. (See the next page.)
Installation type
Floor-mount or overhead-mount (Only for HSS-G)
Ambient temperature
During operation: 0 to 40ºC
During storage and transportation: -10 to 60ºC
Humidity
During operation: 90% or less (No dew condensation allowed.)
During storage and transportation: 75% or less (No dew condensation
allowed.)
Vibration
During operation: 4.9 m/s
2
(0.5G) or less
During storage and transportation: 29.4 m/s
2
(3G) or less
Altitude
During operation: 1,000 m or less
Safe installation
environment
Refer to the SAFETY PRECAUTIONS,
3.1 "Insuring the proper
installation environment"
Working space, etc.
• Sufficient service space must be available for inspection and disassembly.
• Keep wiring space (at least 190 mm for Standard type, at least 230 mm for
Dust-proof, splash-proof type) behind the robot, and fasten the wiring to the
mounting face or beam so that the weight of the cables will not be directly
applied to the connectors.
Grounding conditions
Functional ground
See the figure given on page 11.