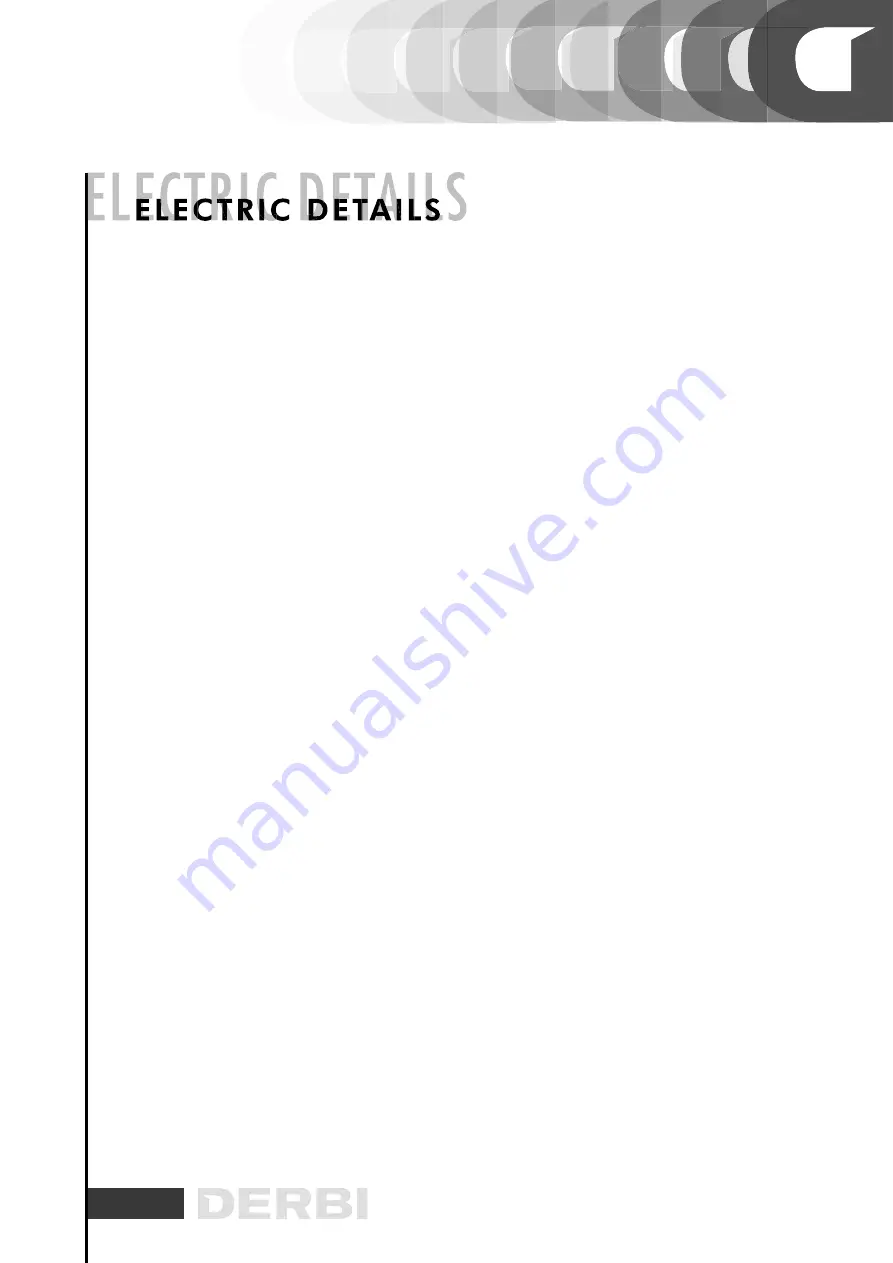
167
6-4-1. Starter motor removal(Fig. 6-34, 6-35)
01. remove the starter motor wire lock. nut (1) Fig. 6-34
02. remove the two starter motor mounting bolts (1) and the motor. Fig. 6- 35
CAUTION
BEFORE SERVICING THE STARTER MOTOR, TURN OFF THE IGNITION SWITCH AND DISCONNECT THE
BATTERY GROUND. THEN TURN ON IGNITION SWITCH TU SEE IF THE STARTER MOTOR CAN OPERATE TO
ENSURE WORK SAFETY.
6-4-2. Disassembly and inspection (Fig. 6 -36, 6-37, 6-38)
01. remove the two starter motor case bolts (1) and remove the front and rear covers, commutator, housing,
and other parts. Fig. 6-36, 6-37
02. inspect the removed parts.
03. inspect the commutator for any wear. damage, or discoloration and other visual faults -- replace if
necessary.
04. Clean off any metal powder from the commutator segments.
05. Check for continuity between pairs of commutator segments. There should be continuity. Fig. 6-38
06. a continuity check between individual commutator segment and armature shaft. There should be no
continuity.
6-4-3. Starter motor housing continuity check (Fig. 6-39)
01. Check and make sure that there is no continuity between the wire terminal and the brushes -- replace if
necessary.
6-4-4. Brush inspection (Fig. 6-40)
01. measure the length of each brush (a).
* Service Limit.:8.5mm; replace if below
02. check for continuity between the brushes replace if there is continuity.
03. check front cover bearing and oil seal for wear, looseness, or damage -- replace if necessary.
04. check the rear cover bearing for wear, looseness, or damage
* replace if necessary.
6-4.5. Assembly (Fig. 6-37)
01. remove the brush springs and then install the brushes into the brush holder.
02. insert the commutator into the starter motor body. Be careful not to damage the mating surfaces of
brushes and commutator.
03. apply a thin coat of grease to the rear cover bearing and then install the washers and rear cover.
04. Install the brush spring and make sure that the brushes can move freely after installation.
Summary of Contents for ATV DXR 200
Page 1: ...ATV DXR 200 WORKSHOP MANUAL ...
Page 3: ......
Page 8: ...7 ...
Page 9: ...8 ...
Page 11: ...10 ...
Page 18: ...17 ...
Page 19: ...18 ...
Page 23: ...22 ...
Page 28: ...27 ...
Page 31: ...30 ...
Page 35: ...34 ...
Page 37: ...36 ...
Page 39: ...38 ...
Page 41: ...40 ...
Page 45: ...44 ...
Page 47: ...46 ...
Page 49: ...48 ...
Page 56: ...55 ...
Page 61: ...60 ...
Page 63: ...62 ...
Page 65: ...64 ...
Page 69: ...68 ...
Page 71: ...70 ...
Page 73: ...72 ...
Page 77: ...76 ...
Page 79: ...78 ...
Page 81: ...80 ...
Page 85: ...84 ...
Page 87: ...86 ...
Page 91: ...90 ...
Page 93: ...92 ...
Page 97: ...96 ...
Page 99: ...98 ...
Page 101: ...100 ...
Page 103: ...102 ...
Page 107: ...106 ...
Page 109: ...108 ...
Page 111: ...110 ...
Page 115: ...114 ...
Page 117: ...116 ...
Page 123: ...122 ...
Page 127: ...126 ...
Page 129: ...128 ...
Page 133: ...132 ...
Page 135: ...134 ...
Page 139: ...138 ...
Page 141: ...140 ...
Page 143: ...142 ...
Page 145: ...144 ...
Page 147: ...146 ...
Page 151: ...150 ...
Page 153: ...152 ...
Page 154: ...153 6 2 IGNITION SYSTEM BRIEFING 01 AC generator 03 Ignition coil 02 C D I 04 plug cap ...
Page 159: ...158 ...
Page 165: ...164 ...
Page 166: ...165 6 4 STARTING SYSTEM BRIEFING 01 starter motor 03 start button 02 starter relay ...
Page 169: ...168 ...
Page 171: ...170 ...
Page 175: ...174 ...
Page 177: ...176 ...
Page 194: ...create by w w w ciandisseny com ...