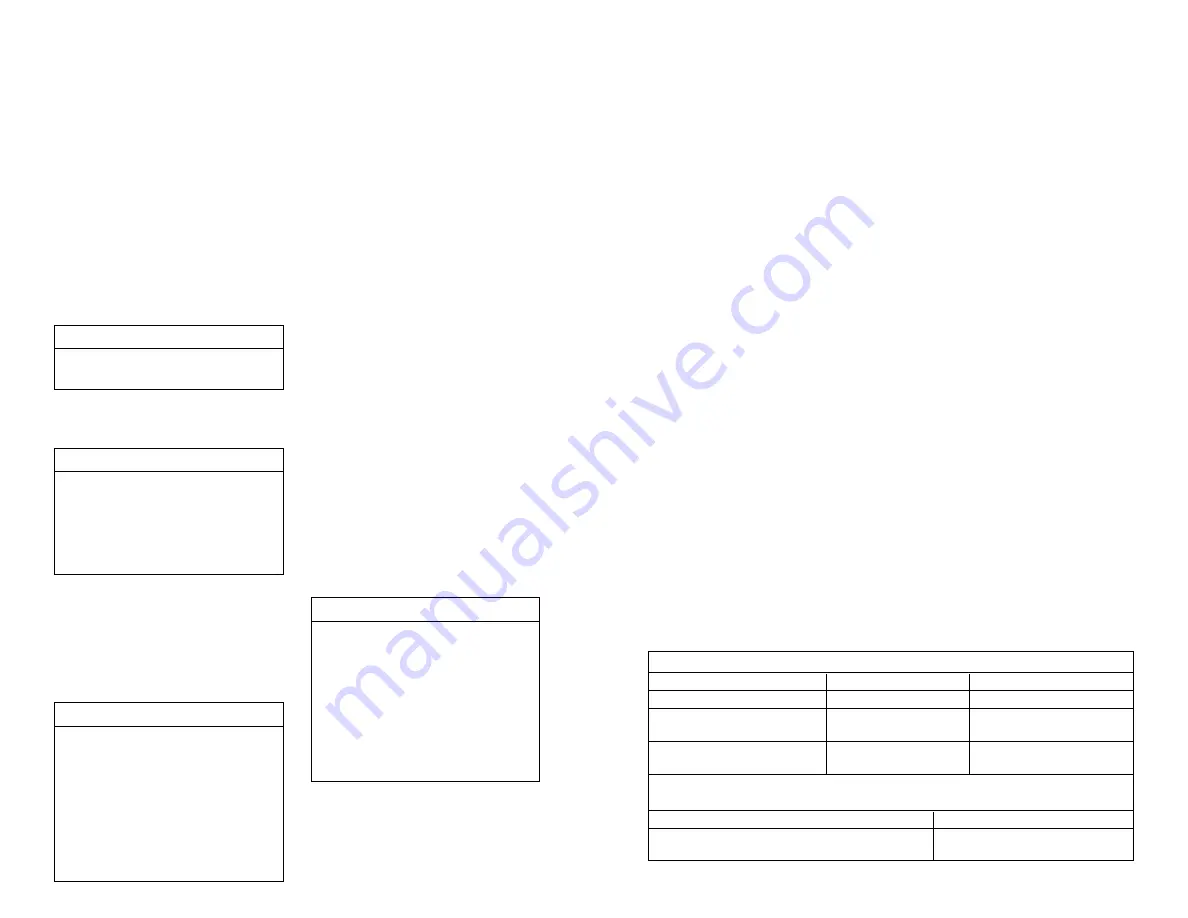
55
G. How to Select Coolant
Antifreeze
Use genuine Detroit Diesel Power
Cool
or an equivalent fully formulated,
inhibited ethylene glycol (IEG)-base
coolant (low silicate formulation) that
meets or exceeds the standard of
either the GM 6038-M formulation (GM
1899-M performance), or ASTM D
4985 requirements.
A 50%
Power Cool
antifreeze/water
solution is normally used as a factory
fill. Concentrations over 67% are not
recommended because of poor heat
transfer capability, adverse freeze pro-
tection and possible silicate dropout.
Concentrations below 33% offer little
freeze, boilover or corrosion protection.
If Detroit Diesel Power Cool or
equivalent precharged inhibited ethy-
lene glycol (IEG) is not used, Detroit
Diesel Maintenance Product supple-
mental inhibitors must be added to
the coolant at initial fill. Inhibitor lev-
els in all coolants used must be
maintained at proper concentration
thereafter. Refer to “Proper SCA
Dosage for Initial Fill and Main-
tenance Requirements” chart in this
section. Refer to “Inhibitor Test
Procedures” (page 58) for required
inhibitor levels.
Antifreeze solution should be used
year-round to provide freeze and boil-
over protection as well as a stable envi-
ronment for seals and hoses.
In extremely hot environments, clean,
soft, properly inhibited water may be
used if Detroit Diesel Maintenance
Product supplemental corrosion
inhibitors are also added in the right con-
centration. If water is used, supplemen-
tal coolant additive levels should be
increased from 3% to 6% by volume
(refer to
Specifications
, pages 73-74).
Only non-chromate inhibitors
should be used with coolant solutions.
Coolant must be tested for required
inhibitor levels at the intervals shown
under “Coolant Test Intervals” in this
section. Adjust the concentration if not at
the proper protection level.
Mix coolant/water solution at the proper
concentration before adding to the cool-
ing system. This should prevent over- or
under-coolant concentration problems.
Methyl alcohol-based antifreeze is
not recommended for use in Detroit
Diesel engines because of its effect
on the non-metallic components of
the cooling system and its low boil-
ing point.
Methoxy propanol-based anti-
freeze is also not recommended
because it is not compatible with
Initial Fill SCA Dosage
Coolant
Coolant Element
Liquid
Precharged IEG* & Water
NONE
NONE
IEG & Water
Select Element from
3% by Volume or 1 Pint
Specifications Page
per 4 Gallons
Water only
Select Element from
6% by Volume or 1 Quart
Specifications Page
per 4 Gallons
*Such as Detroit Diesel Power Cool
®
antifreeze, or equivalent.
Maintenance SCA Dosage
Coolant Element
Liquid
Select Element from
Specifications
Page
0.6% by Volume or 1 Pint
per 20 Gallons
Proper SCA Dosage for Initial Fill and Maintenance Requirements
state and/or federal (EPA) recom-
mendations.
2. Fill a new replacement cartridge
about two-thirds full with clean
fuel oil. Coat the seal gasket light-
ly with clean fuel oil.
3. Install the new cartridge and tighten
by hand until the gasket touches
the mounting adaptor head.
Tighten an additional one-half turn.
4. Start the engine and check for
leaks.
If the engine fails to start after re-
placement of the fuel strainer and/or
filter elements, the fuel system will
require priming with tool J 5956 (or
equivalent). Authorized Detroit Diesel
service outlets are properly equipped
to perform this service.
54
NOTICE:
Overtightening may distort or crack
the filter adaptor.
NOTICE:
To improve engine starting, have
replacement elements filled with
fuel and ready to install immediate-
ly after used elements are re-
moved. This will prevent possible
siphoning and fuel system aeration.
NOTICE:
Under no circumstances should the
starting motor and fuel pump be
used to prime the fuel filter and
strainer. Prolonged use of the start-
ing motor and fuel pump to prime
the fuel system can result in damage
to the starter, fuel pump, and injec-
tors and cause erratic running of the
engine due to the amount of air in
the lines and filters.
F. Engine Out of Fuel—
How to Restart
When an engine has run out of fuel,
there is a definite procedure to follow
when restarting it.
1. Fill the fuel tank with the recom-
mended grade of fuel. If only par-
tial filling is possible, add a
minimum of 10 gallons (38 liters)
of fuel to the tank.
2. Remove the fuel strainer/water
separator from its cover, fill it with
fuel, and reinstall it.
3. Remove the fuel filter from its
cover, fill it with fuel, and reinstall
it.
4. Start the engine, and check fuel fil-
ter and strainer for leaks.
If the engine fails to start after re-
placement of the fuel strainer and/or
filter, the fuel system will require
priming with tool J 5956 (or equiva-
lent). Authorized Detroit Diesel ser-
vice outlets are properly equipped to
perform this service.
NOTICE:
Under no circumstances should the
starting motor and fuel pump be
used to prime the fuel filter and
strainer. Prolonged use of the start-
ing motor and fuel pump to prime
the fuel system can result in dam-
age to the starter, fuel pump, and
injectors and cause erratic running
of the engine due to the amount of
air in the lines and filters.
Summary of Contents for 92 Series
Page 41: ...NOTES 77 NOTES 76 ...
Page 42: ...NOTES 78 ...