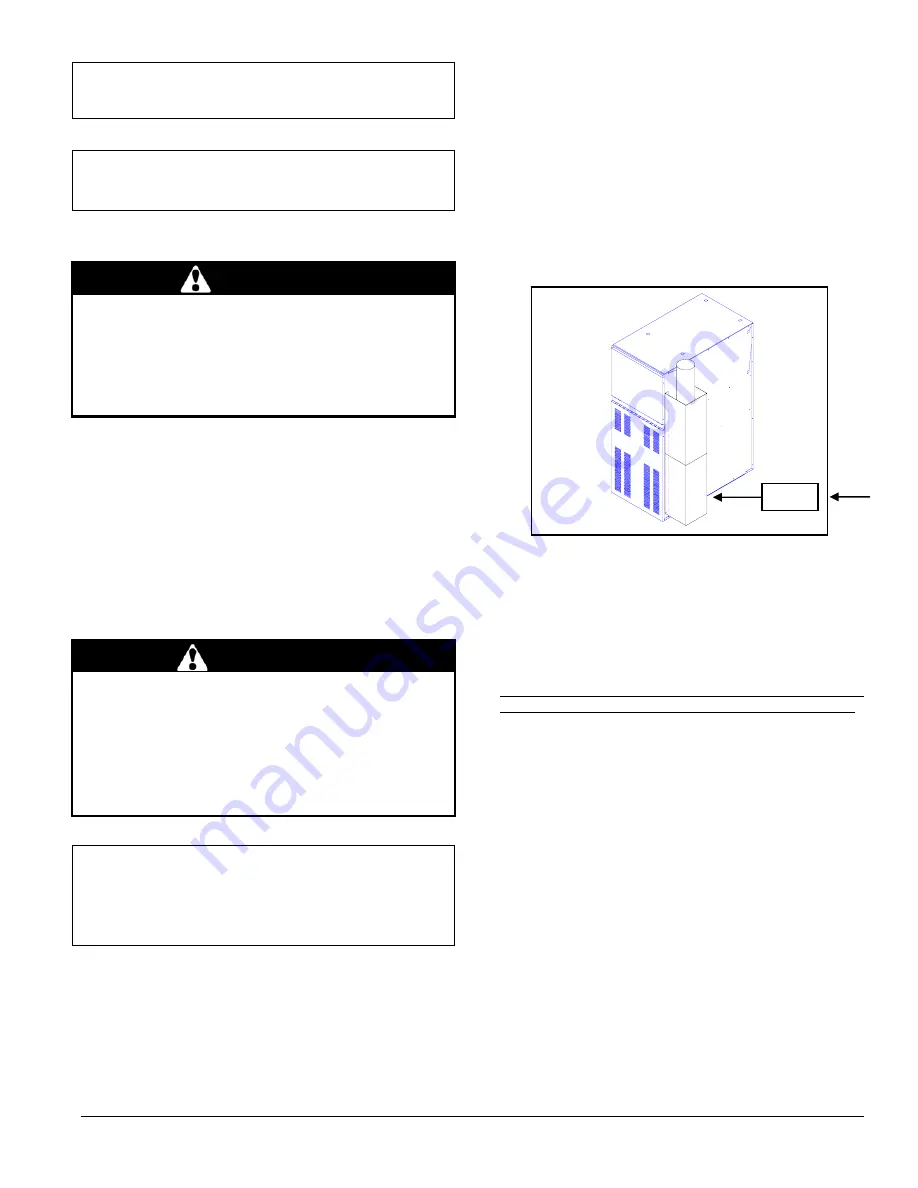
NOTE:
The manufacturer of your furnace does not test
any detectors and makes no representations
regarding any brand or type of detector.
5
CAUTION
Ensure that the area around the combustion air intake
is free of snow, ice and debris
.
1.4.1) Freezing temperatures and your building
WARNING
Freezing temperature warning.
Turn off water supply.
If your heater remains shut off during cold
weather, the water pipes could freeze and burst,
resulting in serious water damage.
If the structure is unattended during cold weather you should take
the following precautions:
a. Turn off main water supply into the structure and drain the
water lines if possible. Open faucets in appropriate areas;
b. Have someone check the structure frequently during cold
weather to make sure it is warm enough to prevent pipes from
freezing. Contact a qualified service agency, if required.
1.5) LOCATION
The unit must be installed in a location where the ambient
and return air temperatures are over 15°C (60°F).
WARNING
This furnace is not watertight and is not designed
for outdoor installation. This furnace shall be
installed in such a manner as to protect the
electrical components from water. Outdoor
installation will lead to a hazardous electrical
condition and to premature furnace failure.
CAUTION
If this furnace is installed in an attic, it is important
to keep insulation at least 0.3 m (12") away from
any furnace openings. Some types of insulating
material may be combustible.
This furnace is approved for reduced clearances to
combustible construction. Therefore, it may be installed in a
closet or similar enclosure. As this unit may be installed as
an upflow, counter flow, or horizontal furnace, it may be
located in a basement, on the same level as the area to be
heated, suspended, or in a crawlspace. In any case, the unit
should always be installed level.
In a basement, or when installed on the floor (as in a
crawlspace), it is recommended that the unit be installed on
a concrete pad that is 25.4 mm to 50.8 mm (1" to 2") thick.
When installed in the counter flow position, this furnace must
not be installed on combustible flooring, unless the approved
sub-base is used (Model # DFB-101). Since the flue pipe is
in counter flow position, be sure that the clearances from the
flue pipe to combustible construction are maintained. Also, it
is recommended to use the flue pipe protection kit FPG-101
or FPG-102. Refer to Figure 1 and the installation
instructions included with the kit.
FIGURE 1
DNS-0278 Rev. A
When installed in an horizontal position, the furnace may be
suspended by using an angle iron frame, as long as the total
weight of both the furnace and the frame are included in the
calculations. Other methods of suspension are acceptable.
When installed in the horizontal position, this furnace must
not be installed on combustible flooring, unless the approved
sub-base is used (Model # HFB-101).
The required minimum clearances for this furnace in all
positions are specified in Tables 8.1 and 8.2, p, 21 & 22.
The furnace should be located as closely as possible to the
chimney or vent in order to keep vent connections short and
direct. The furnace should also be located near the centre of
the air distribution system.
1.5.1) Air for combustion and ventilation
Refer to the CAN/CSA-B139 installation code for complete
regulations and for guidance on retrofit applications.
This furnace should be installed in a location in which the
facilities for ventilation permit satisfactory combustion of oil,
proper venting and the maintenance of ambient tempera-
tures at safe limits under normal conditions of use. The
location should not interfere with the proper circulation of air
within the confined space.
When this furnace is installed in a closet or similar enclosure,
2 ventilation openings are required for com-bustion air. The
openings should be located about 152.4 mm (6") from
the top and the bottom of the enclosure at the front of the
furnace. Table 1 (p. 6) indicates the minimum dimensions
required for these ventilation openings.
FPG
445 01 4036 02