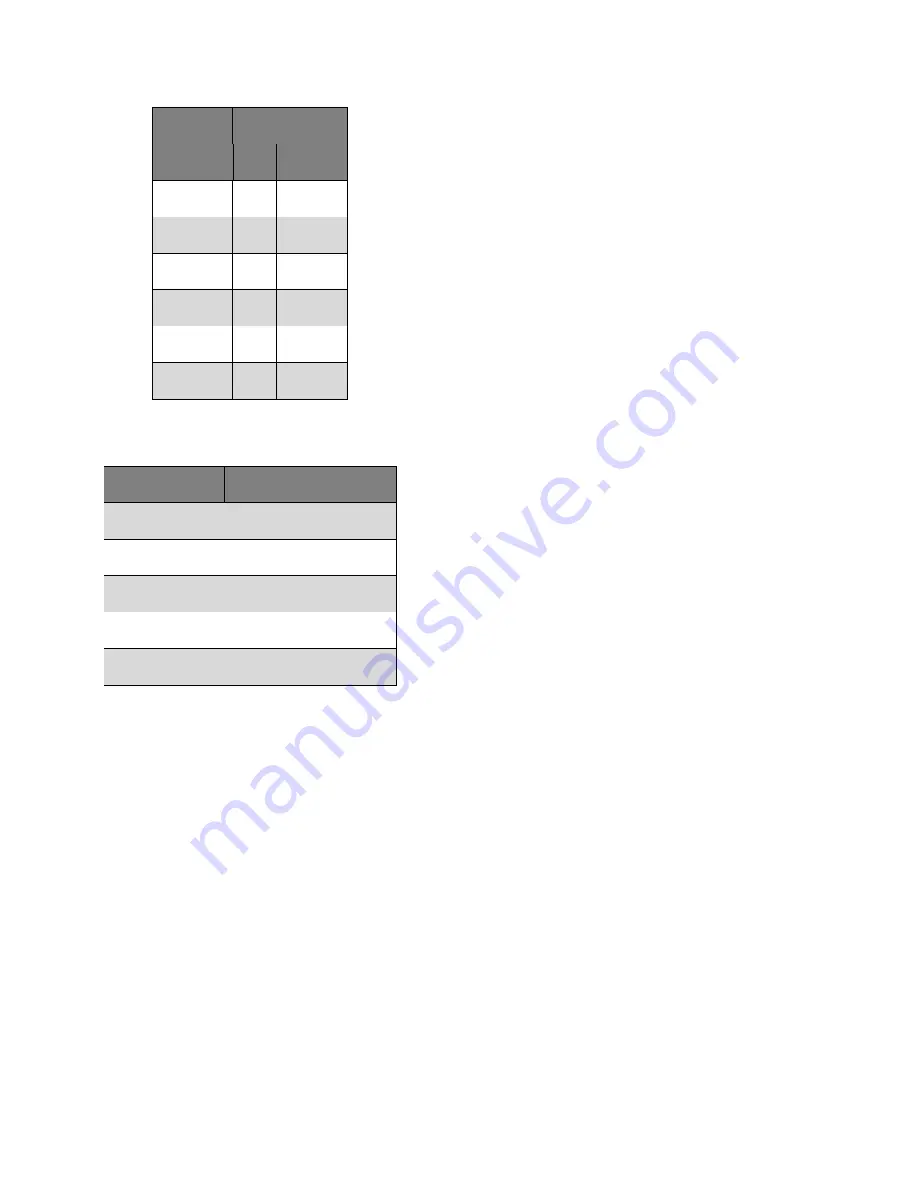
Table 8 – Maximum equivalent vent length (ft) for 2-
stage unit and altitude up to 4500 ft
Unit size
Vent pipe dia.
BTU/hr
2"
3"
30,000
100
N/A
45,000
70
90
60,000
70
90
75,000
70
90
105,000
15
80
120,000
10
40
Table 9 – Deduction for fittings
Type of elbow
Equivalent Length (ft)
45° standard
5
45° long sweap
2.5
90° standard
10
90° long sweap
5
Tee
1.5
7.7
EXHAUST PIPE CONNECTION
TO FURNACE
Never common vent with any other appliance. Do not
install in the same chase or chimney as a metal or high
temperature plastic pipe from another gas or fuel-burning
appliance unless the required minimum clearances to
combustibles are maintained between the approved PVC
pipe and the other pipes. Clean and deburr all pipe cuts.
In the included parts bag, an exhaust venting gasket is
supplied and needs to be installed on the exhaust of the
top panel. (See figure 27)
When 3" pipe is used, connect a 2" to 3" coupling to the
2" pipe.
For proper installation of venting/exhaust pipe:
1. Position the supplied venting gasket on the top
panel exhaust.
2. Slowly slide a 2" diameter pipe throught the venting
gasket. This step will be easier if pipe is chamfered.
3. Position this venting pipe length on the rubber vent
collector and tighten the collar.
4. Install the remaining vent pipes. It is recommended
that all pipes be cut, prepared, and preassembled
before permanently cementing any joint.
5. Working from furnace to outside, cut the pipe to the
required length(s).
6. Deburr the inside and outside of the pipe.
7. Chamfer the outside edge of pipe for better
distribution of primer and cement.
8. Clean and dry all surfaces to be joined.
9. Check dry fit of the pipe and mark insertion depth
on the pipe.
10. After the pipes have been cut and preassembled,
apply a generous layer of cement primer to the pipe
fitting socket and end of the pipe to insertion mark.
Quickly apply approved cement to end of the pipe
and fitting socket (over primer). Apply cement in a
light, uniform coat on the inside of socket to prevent
build-up of excess cement. Apply second coat.
11. While cement is still wet, twist pipe into the socket
with 1/4” turn. Be sure the pipe is fully inserted into
the fitting socket.
12. Wipe excess cement from the joint. A continuous
bead of cement will be visible around perimeter of
a properly made joint.
13. Handle pipe joints carefully until cement sets.
14. Horizontal portions of the venting system shall be
supported to prevent sagging. Support any piping
at a minimum of every 5 ft. using perforated metal
hanging strap or commercially available hangars
designed to support plastic pipe.
15. Prevent condensate from accumulating in the pipes
by sloping the combustion air piping and vent piping
downward toward furnace a minimum of 1/4” per
linear ft. with no sags between hangers.
16. Complete the vent installation by installing the
required termination.
allowed termination.
17. Use appropriate methods to seal the openings
where combustion air pipe and vent pipe pass
through roof or sidewall.
7.8
COMBUSTION AIR PIPE
CONNECTION
Chinook gas furnaces have three possible locations for
the combustion air connection : top panel, right side
panel or left side panel. Choose which configuration is
best suited for your application. See figures 18 and 19.
20
Summary of Contents for C105-1-D
Page 24: ...Figure 26 Alternate horizontal termination C Figure 27 Venting gasket 23...
Page 25: ...Figure 28 Direct vent clearance 24...
Page 26: ...Figure 29 Other than Direct vent clearance 25...
Page 34: ...Figure 32 Single Stage PSC Wiring diagram...
Page 35: ...Figure 33 Two Stage PSC Wiring diagram...
Page 36: ...Figure 34 Single Stage ECM Wiring diagram...
Page 39: ...Figure 35 Dimensions 38...
Page 40: ...Figure 36 Exploded view CXX 1 X part 1...
Page 41: ...Figure 37 Exploded view CXX 1 X part 2...
Page 43: ...Figure 38 Exploded view Cxx 1 D part 1...
Page 44: ...Figure 39 Exploded view Cxx 1 D part 2...
Page 46: ...Figure 40 Exploded view Cxx 2 D part 1...