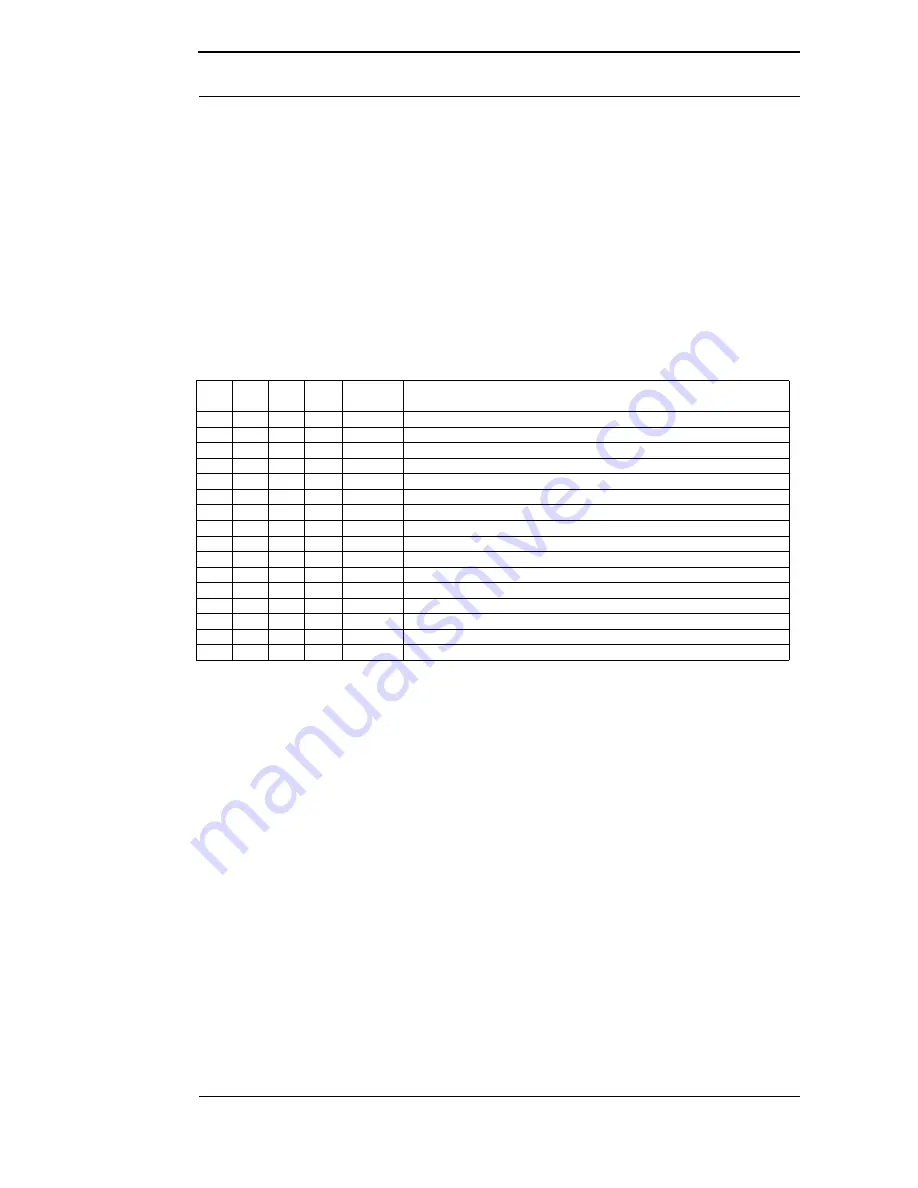
26.8.11
UNIGATE Fieldbus Gateway CANopen® - ProfibusDP V. 2.3
23
Deutschmann Automation GmbH & Co. KG
Error handling
6
Error handling
If the gateway detects an error, the error is signalled by the “State“ LED lighting red and, simulta-
neously, the error number being indicated by means of LEDs “Error No.“ as shown in the table
below. In addition, this error number is transferred as an external diagnostic byte via the Profibus
to the Master. A distinction can be made between two error categories:
Serious errors (1-5): In this case, the gateway must be switched off and switched back on again.
If the error occurs again, the gateway must be exchanged and returned for repair.
Warnings (6-15): These warnings are displayed for one minute simply for information purposes
and are then automatically reset. If such warnings occur frequently, please inform the after-sales
service.
In the configuration mode these displays are not valid and only meant for internal use.
LED8 LED4 LED2 LED1
Error no.
resp. ID Error description
0
0
0
0
0
Reserved
0
0
0
1
1
Reserved
0
0
1
0
2
EEROM error
0
0
1
1
3
RAM error or ASIC error
0
1
0
0
4
Error at Reset CAN-Bus
0
1
0
1
5
Error at "Set Operational" CAN-Bus
0
1
1
0
6
Reserved
0
1
1
1
7
Error at generating PDO
1
0
0
0
8
Error at generating SDO
1
0
0
1
9
Buffer overflow or Timeout at RS232
1
0
1
0
10
Error at "Add-Node"
1
0
1
1
11
Incorrect CANopen® handle (e. g. more than 8 mappings / PDO)
1
1
0
0
12
Profibus configuration error
1
1
0
1
13
General CAN-driver error (e. g. no bus connected or wrong wiring)
1
1
1
0
14
Error at access SDO
1
1
1
1
15
Internal error
Table 1: Error handling