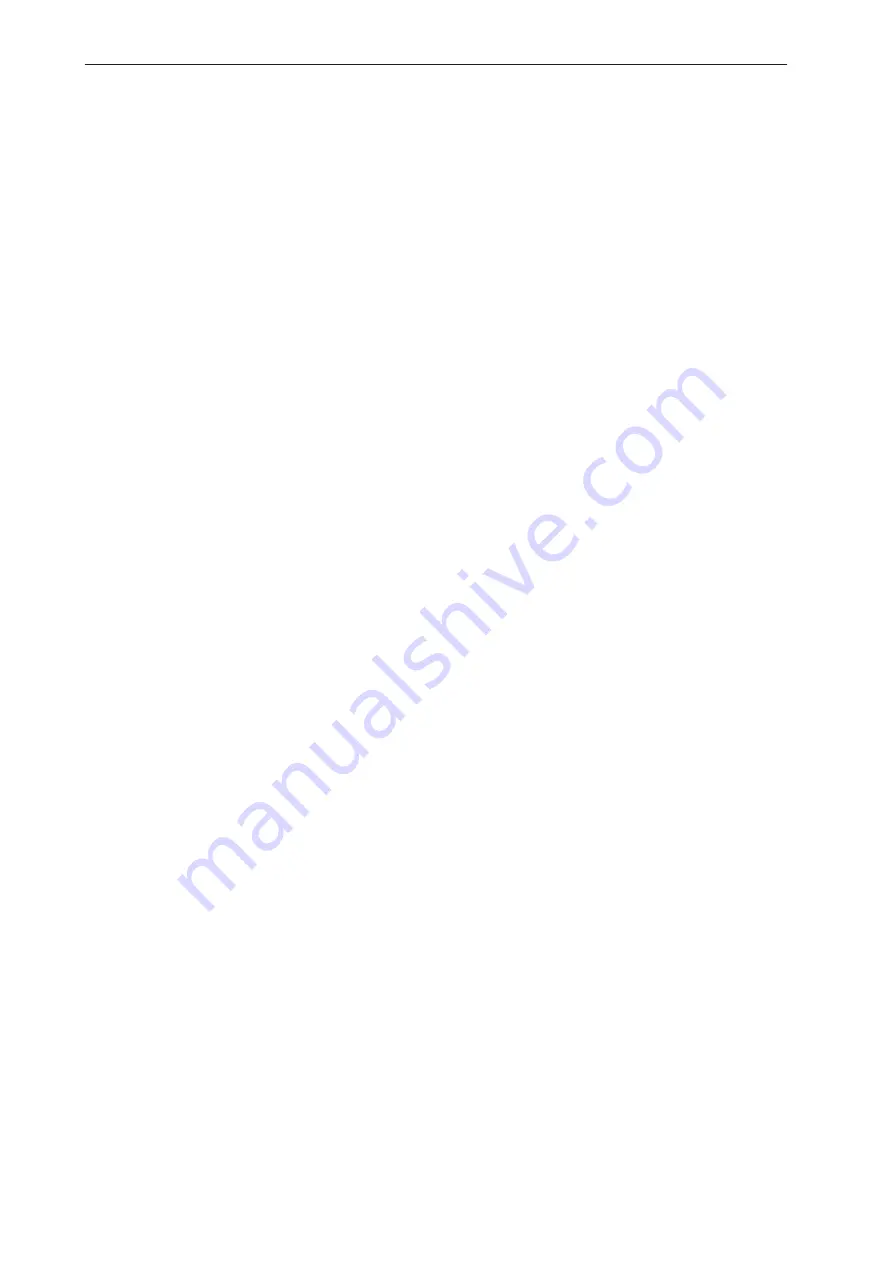
16
EN
1. As a rule, disengage the driving system, secure the tractor and stop the engine prior to carrying out
any maintenance, servicing, cleaning or repair work! Always remove the ignition key!
2. Check all nuts and bolts at regular intervals and retighten as required! Comply with prescribed
torques!
3. If the Rotary Tedder is raised, prop up the implement with suitable supports before carrying out
maintenance!
4. When changing working elements, use appropriate tools and protective gloves!
5. Dispose of used oil, grease and filters according to regulations!
6. Always disconnect the power suppy before carrying out any work on the electrical system!
7.
The protection devices which are subject to wear and tear must be inspected frequently and be
exchanged in good time.
8. The generator and battery cables should be disconnected before any electrical welding is carried
out on the tractor or the mounted Rotary Tedder!
9. Do not clean the Rotary Tedder with aggressive cleaning agents. This can cause corrosion to
polished metal surfaces, e.g. hydraulic cylinders.
1.11 Safety instructions for the Rotary Tedder
1. General safety instructions are contained in this documentation and in the accident prevention
regulations UVV 1.1 §1 of the German "Landwirtschaftliche Berufsgenossenschaft" (Agricultural
Trade Association).
2. Prior to mounting the implement or lifting the implement for the first time, check the space available.
3. Check the cardan shaft before the first operation and adjust it to your tractor, if necessary (see
chapter "Adjusting the cardan shaft")!
4. Check the tyre pressure 1.5 bar (16x6.50-8 4PR) and 2.5 bar (215/65-15) at regular intervals.
5. Before each transport:
z
disengage p.t.o shaft,
z
wait until rotary units come to a complete standstill,
z
place the Rotary Tedder in transport position,
z
check that it is correctly secured,
6. Make sure that no-one is within reach of the implement when raising, lowering, and swivelling in
the rotary unit.
7.
Repair work on pre-tensioned energy storers (springs, accumulators etc.) may only be carried out
by specialists using the correct tools which comply with all prescribed standards. All such repairs
may only be carried out in specialist workshops!
8. Before proceeding with any maintenance and repair work, you must read the corresponding
instructions! All maintenance, repair and adjustment work may only be carried out with the Rotary
Tedder at a standstill! Shut down the engine and remove the ignition key!
Summary of Contents for CondiMaster 6831
Page 2: ......
Page 4: ...2 EN...
Page 13: ...11 EN 6 Keep clear of the swivel area of the implement...
Page 33: ...31 EN 40 h 8 h 40 h 40 h 8 h 8 h 16 h 40 h Fig 5 1 Fig 5 2...
Page 37: ......