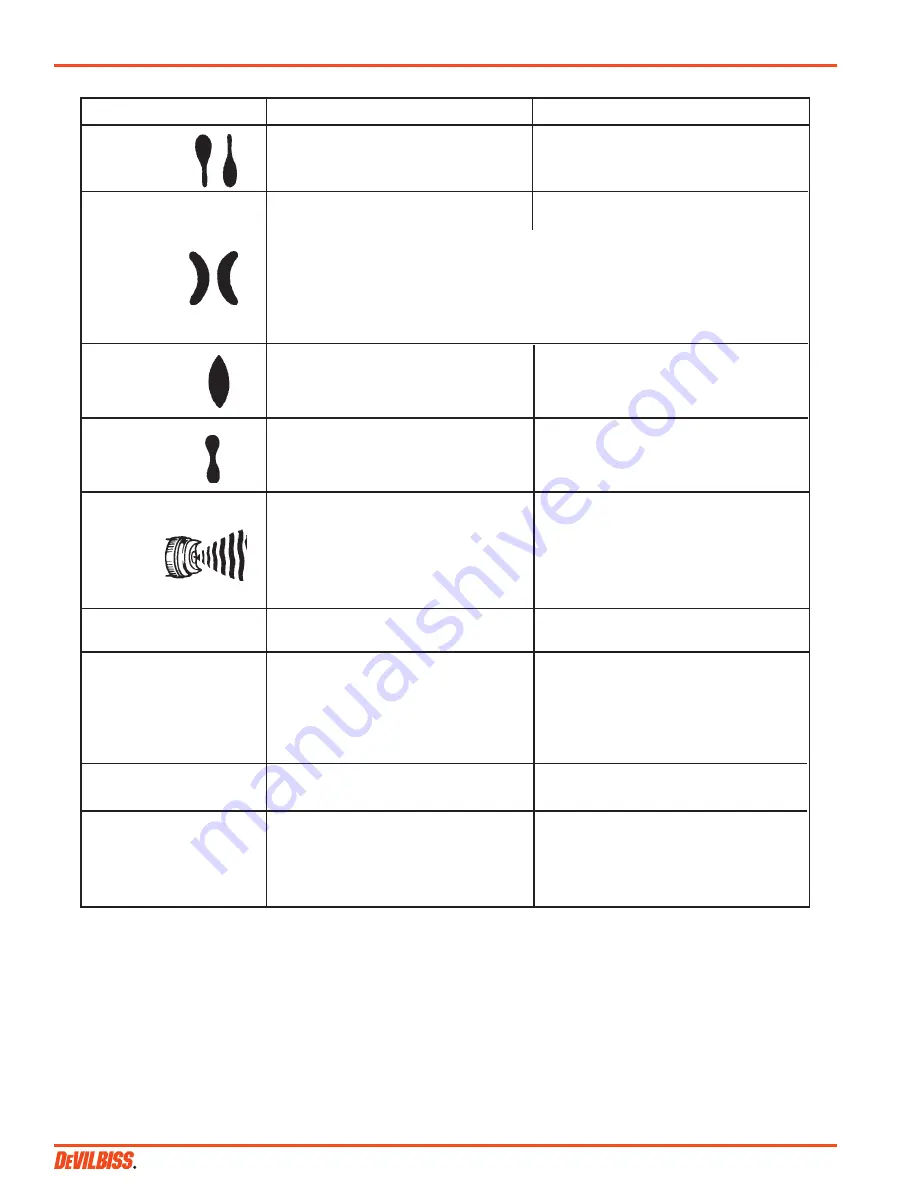
EN
SB-2-303-F (1/2016)
6 / 8
TROUBLESHOOTING
CONDITION
CAUSE
CORRECTION
Heavy top or
Horn holes plugged.
Clean. Ream with non-metallic point.
bottom pattern
Obstruction on top or bottom of fluid tip.
Clean.
Cap and/or tip seat dirty.
Clean.
Heavy right or left side pattern
Left or right side horn holes plugged.
Clean. Ream with non-metallic point.
Dirt on left or right side of fluid tip.
Clean.
Remedies for the top-heavy, bottom-heavy, right-heavy and left-heavy patterns:
1) Determine if the obstruction is on the air cap or the fluid tip. Do this by making a test spray
pattern. Then, rotate the cap one-half turn and spray another pattern. If the defect is inverted,
obstruction is on the air cap. Clean the air cap as previously instructed.
2) If the defect is not inverted, it is on the fluid tip. Check for a fine burr on the edge of the
fluid tip. Remove with #600 wet or dry sand paper.
3) Check for dried paint just inside the opening. Remove paint by washing with solvent.
Heavy center pattern
Too much material.
Reduce fluid flow on suction guns. Reduce
fluid pressure on pressure feed guns .
Material too thick.
Thin to proper consistency.
Split spray pattern
Not enough material.
Reduce air pressure or increase fluid flow by
turning fluid needle adjusting screw counter
clockwise on suction feed, increase fluid
pressure on pressure feed guns.
Jerky or fluttering spray
*Loose or damaged fluid tip/seat.
Tighten or replace.
Insufficient fluid in cup or pressure tank.
Fill cup or tank.
Gun (with cup) tipped at excessive angle.
Do not tip excessively or rotate fluid tube.
Obstructed fluid passage or hose.
Clean.
Loose or cracked fluid tube in cup or tank.
Tighten or replace.
Too heavy fluid for suction feed. Dry or
Change to pressure feed.
worn packing (14) or loose packing nut (15).
Lubricate or replace. Tighten.
Unable to get round spray
Fan adjustment screw not seating properly.
Clean or replace.
Air cap retaining ring loose.
Tighten.
Will not spray
No air pressure at gun.
Check air supply and air lines.
Internal mix or pressure feed air cap and tip
Change to proper suction feed air
used with suction feed.
cap and tip.
Fluid pressure too low with internal mix cap
Increase fluid pressure at tank.
and pressure tank.
Fluid needle adjusting screw not open enough. Open fluid needle adjusting screw.
Fluid too heavy for suction feed.
Thin material or change to pressure feed.
Fluid leaking from packing nut
Packing nut loose.
Tighten, do not bind needle.
Packing worn or dry
Replace or lubricate.
Dripping from fluid tip
Dry packing.
Lubricate. See “Preventive Maintenance”.
Sluggish needle.
Lubricate. See “Preventive Maintenance”.
Tight packing nut.
Adjust. See “ Preventive Maintenance”.
Sprayhead misaligned, causing needle to bind. Tap all around sprayhead with wooden
mallet and retighten locking bolt.
*Most common problem.