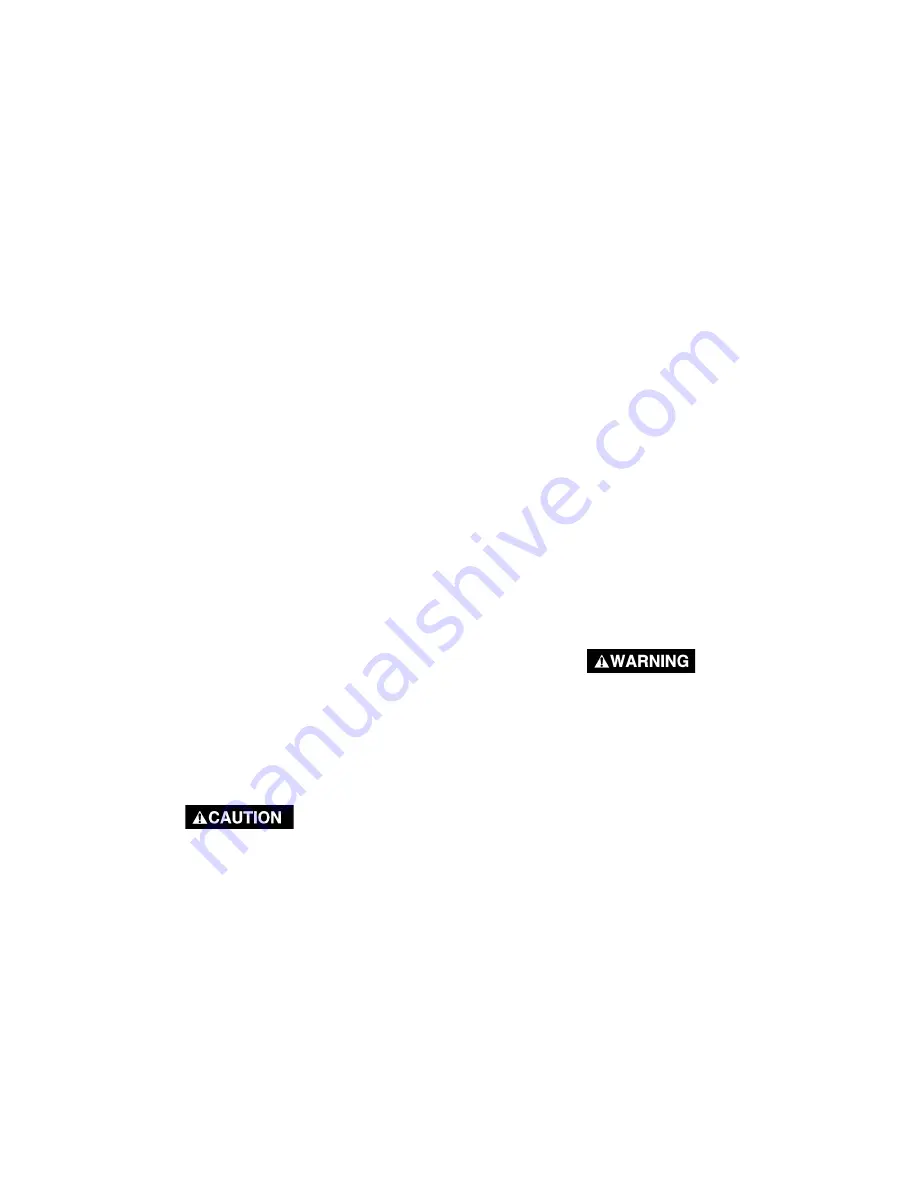
13
MAINTENANCE
Air Compressor
A clean air compressor and engine run cooler and
provide longer service. Clean or blow off fins and any
other parts of the air compressor and engine that collect
dust or dirt. Do not place tags, containers or other
material on or against the ventilation openings in the belt
guard. Adequate ventilation is necessary to maintain
proper air compressor operating temperature.
Check Valve - Inspection and
Replacement
Remove the check valve for inspection or replacement
if air is leaking constantly back through the check valve.
Use the following procedure to inspect, clean or replace
the check valve.
1.
Release air pressure from the air tank.
2.
Loosen the top and bottom tube nuts and remove
the outlet tube.
3.
Unscrew the check valve (turn counterclockwise)
using a socket wrench.
4.
Check that the valve disc moves freely inside the
check valve and that the spring holds the disc in
the upper, closed position. The check valve may
be cleaned with a solvent.
5.
Apply teflon tape to the check valve threads.
Reinstall the check valve (turn clockwise). The disc
should still move freely - do not over tighten.
6.
Replace the outlet tube and tighten top and bottom
nuts.
Safety Valve - Inspection and
Replacement
IF THE SAFETY VALVE DOES NOT WORK
PROPERLY OVER-PRESSURIZATION CAN
OCCUR AND CAUSE AIR TANK RUPTURE
OR EXPLOSION. DAILY PULL THE RING
ON THE SAFETY VALVE AND MAKE SURE IT
OPERATES FREELY. IF THE VALVE IS STUCK
OR DOES NOT OPERATE SMOOTHLY, IT
MUST BE REPLACED WITH THE SAME TYPE
OF VALVE HAVING AN IDENTICAL PRES-
SURE RATING.
Compressor Pump Air Intake
Filter -Inspection and
Replacement
A dirty air filter will not allow the compressor to operate
at full capacity. Before you use the compressor, check
the air filter to be sure it is clean and in place.
If it is dirty, replace with a new filter. The filter may be
removed by using a pair of needle nose pliers or a
screwdriver. Pull or pry out the old filter and push in a
new one.
Compressor Oil - Checking and
Changing
Overfilling with oil will cause premature com-
pressor failure. Do not overfill.
Check oil level in the crankcase daily. Remove the oil fill
plug. The oil level should be even with the top of the fill
hole and must not be allowed to be lower than 3/8" from
the top (6 threads) at any time. It is recommended that
the oil be changed after every 100 hours of operation. To
drain the oil, remove the oil drain plug and collect the oil
in a suitable container. Be sure to replace the plug
securely before adding new oil. Use a compressor oil or
Castrol Heavy Duty 30 weight Crankcase oil capacity is
16 fluid ounces (473.2 ml).
NOTE
Keep the air filter clean at all times. Do not
operate the compressor with the air filter re-
moved.
Summary of Contents for MG4-OLENG-2B
Page 18: ...18 SERVICE NOTES...
Page 19: ...19 SERVICE NOTES...