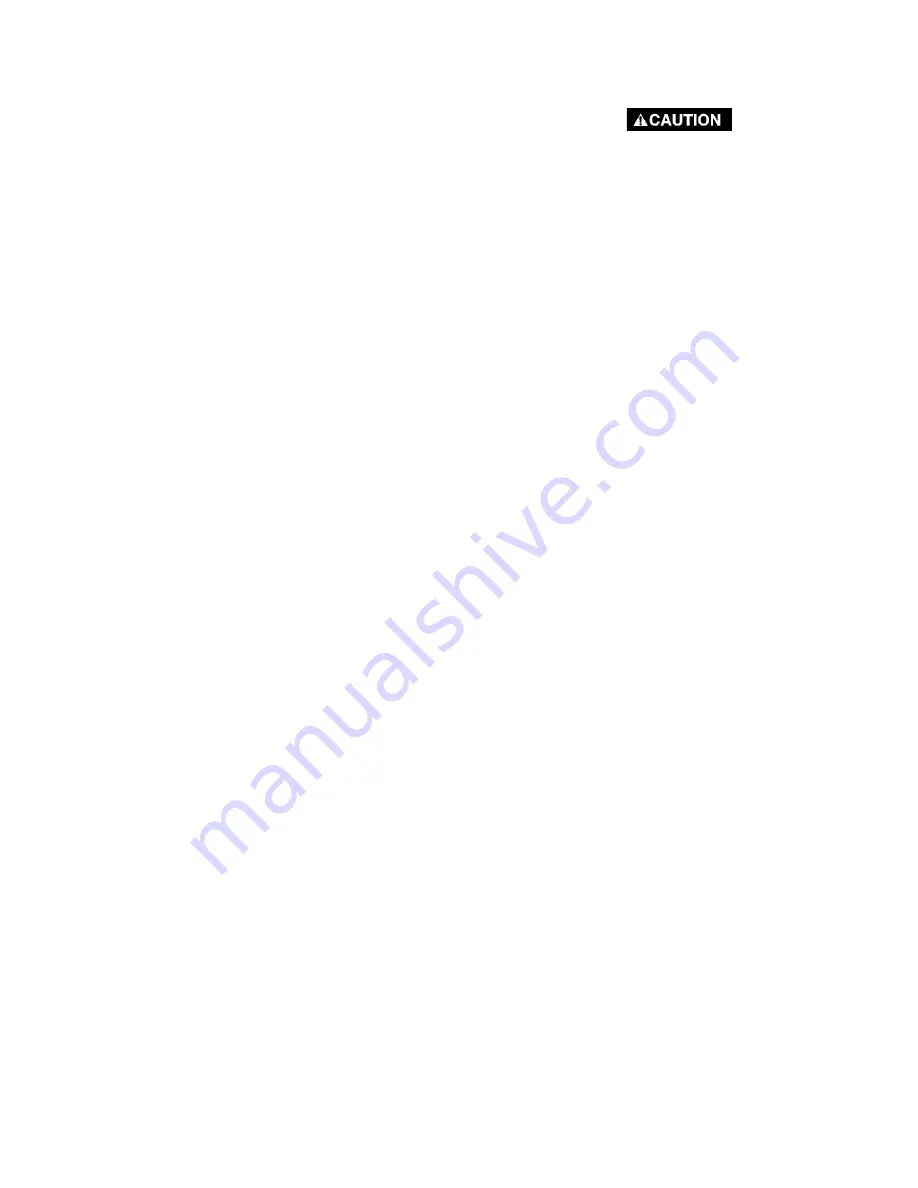
5
Refer to Outfit Part Listing for the specifications of your compres-
sor. Use only a fuse or circuit breaker that is the same rating as the
branch circuit the air compressor is operated on. If the compressor
is connected to a circuit protected by fuses, use dual element time
delay fuses, as noted in the Outfit Parts Listing.
Improper electrical installation of this product
may void its warranty and your fire insurance.
Have circuit wiring performed by qualified per-
sonnel such as a licensed electrician who is
familiar with the current national electric code
and any prevailing local electrical codes.
GLOSSARY
CFM:
Cubic feet per minute.
SCFM:
Standard cubic feet per minute; a unit of measure of air
delivery.
PSIG:
Pounds per square inch gauge; a unit of measure of
pressure.
ASME:
American Society of Mechanical Engineers; made, tested,
inspected and registered to meet the standards of ASME.
California Code: Unit may comply with California Code 462 (L)
(2) / (M) (2). Specification/Model label is on the side of the tank on
units that comply with California Code.
To Lock Out Power:
Place a lock on the line power switch so no
one else can turn on the power.
Cut-In Pressure:
While the motor is off, air tank pressure drops
as you continue to use your accessory or air tool. When the tank
pressure drops to a certain low level the motor will restart auto-
matically. The low pressure at which the motor automatically re-
starts is called “cut-in pressure.”
Cut-Out Pressure:
When you turn on your air compressor and it
begins to run, air pressure in the air tank begins to build. It builds
to a certain high pressure before the motor automatically shuts off
- protecting your air tank from pressure higher than its capacity.
The high pressure at which the motor shuts off is called “cut-out
pressure.”
All DeVilbiss Air Power manufactured air compressors should be
operated on not more than a 50% duty cycle. This means an air
compressor that pumps air more than 50% of one hour, is
DUTY CYCLE
considered misuse, because the air compressor is undersized for
the required air demand. Maximum compressor pumping time per
hour is 30 minutes.
You have purchased an air compressor unit consisting of an
aluminum 2 cylinder, single-stage air compressor pump (with cast
iron sleeves), an air tank, and associated controls and instru-
ments. You will also find a Parts Manual.
Your air compressor can be used for operating paint spray guns,
air tools, caulking guns, grease guns, air brushes, sandblasters,
inflating tires and plastic toys, or spraying weed killers, insecti-
cides, etc. An air pressure regulator is required for most of these
applications.
An air line filter is usually required for removal of moisture and oil
vapor in compressed air when a paint spray gun is used.
ON-RECEIPT INSPECTION
Each air compressor outfit is carefully tested and checked before
shipment. With improper handling, damage may result in transit
and cause problems in compressor operation.
Immediately upon arrival, check equipment for both concealed
and visible damages to avoid expenses being incurred to correct
such problems. This should be done regardless of any visible signs
of
damage to the shipping container. If this product was shipped
directly to you, report any damages to carrier and arrange for
inspection of goods immediately.
For the location or a listing of the nearest DeVilbiss Air Power
Authorized Warranty Service Center, call our toll free number at
1-800-888-2468, Ext. 2
.
GENERAL INFORMATION
An in-line lubricator is usually required for air tools to prolong tool
life.
Separate air transformers which combine the functions of air
regulation and/or moisture and dirt removal should be used where
applicable.
A regularly scheduled program of preventive maintenance will
help provide the long life that has been designed into your
compressor outfit. Before operating or performing any mainte-
nance on your compressor, refer to this manual and your Outfit
Parts Manual. To keep your compressor in good working order,
refer to these publications often and perform preventive mainte-
nance steps as recommended.
SPECIFICATIONS