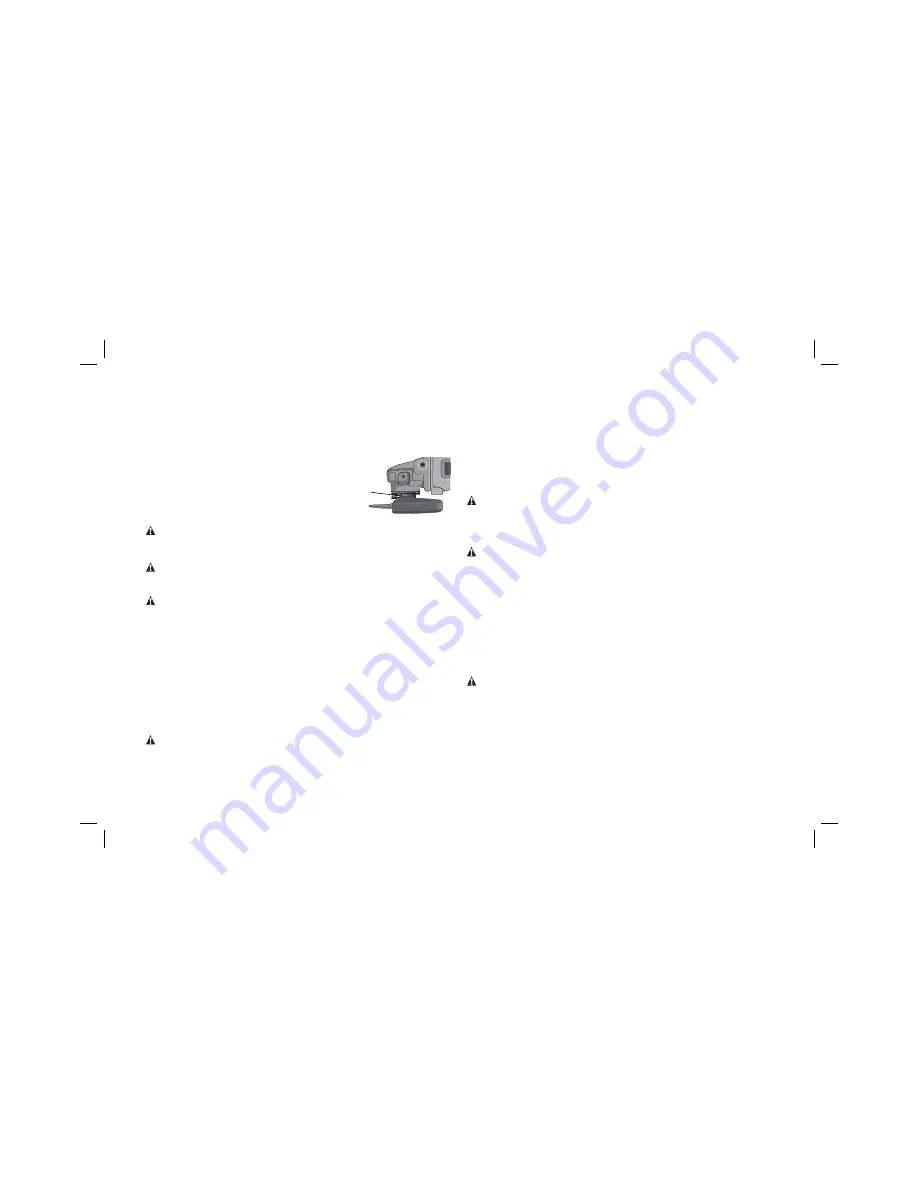
12
4. Close the guard latch to secure the guard on the gear case cover. You should
be unable to rotate the guard by hand when the latch is in closed position. If
rotation is possible, tighten the adjusting screw (P) with clamp lever in the
closed position. Do not operate grinder with a loose guard or clamp lever in open
position.
5. To remove the guard, open the guard latch, rotate
P
the guard so that the arrows are aligned and pull
up on the guard.
NOTE:
If, after a period of time, the guard becomes loose,
tighten the adjusting screw (P) with the clamp lever in the
closed position.
CAUTION:
Do not tighten adjusting screw with clamp lever in open position.
Undetectable damage to guard or mounting hub may result.
MOUNTING CUTTING WHEELS
WARNING:
Turn off and unplug the tool before making any adjustments or
removing or installing attachments or accessories.
Before reconnecting the tool,
turn the switch on and off as previously described to ensure that the tool is off.
CAUTION:
Matching diameter unthreaded backing flange and clamp nut (included
with tool) must be used for cutting wheels.
1. Place the unthreaded backing flange on spindle with the raised section (pilot)
facing up. The raised section (pilot) on the backing flange will be against the
wheel when the wheel is installed.
2. Place the wheel on the backing flange, centering the wheel on the raised section
(pilot).
3. Install the threaded clamp nut with the raised section (pilot) facing away from the
wheel.
4. Depress the spindle lock button and tighten clamp nut with a wrench.
5. To remove the wheel, grasp and turn while depressing the spindle lock button.
USING CUTTING WHEELS
WARNING:
Do not use edge grinding/ cutting wheels for surface grinding
applications because these wheels are not designed for side pressures encountered
with surface grinding. Wheel breakage and injury may result.
1. Allow tool to reach full speed before touching tool to work surface.
2. Apply minimum pressure to work surface, allowing tool to operate at high speed.
Cutting rate is greatest when the tool operates at high speed.
3. Once a cut is begun and a notch is established in the workpiece, do not change
the angle of the cut. Changing the angle will cause the wheel to bend and may
cause wheel breakage.
4. Remove the tool from work surface before turning tool off. Allow the tool to stop
rotating before setting it down.Maintenance
WARNING: To reduce the risk of serious personal injury, turn tool off and
disconnect tool from power source before making any adjustments or removing/
installing attachments or accessories.
Cleaning
WARNING:
Blow dirt and dust out of all air vents with dry air at least once a week.
Wear proper ANSI Z87.1 (CAN/CSA Z94.3) eye protection and proper NIOSH/OSHA/
MSHA respiratory protection when performing this.
Blowing dust and grit out of motor and switch actuator using clean, dry compressed
air is a necessary regular maintenance procedure. Dust and grit containing metal
particles often accumulate on interior surfaces and could create an electrical shock
or electrocution if not frequently cleaned out. It is recommended that a ground fault
circuit interrupter (GFCI) is utilized to further protect the user from electric shock
resulting from the accumulation of conductive particles. If the tool is deactivated by
the GFCI, unplug the tool and check and clean the tool before resetting the GFCI. Wear
proper ANSI Z87.1 (CAN/CSA Z94.3) eye protection and proper NIOSH/OSHA/MSHA
respiratory protection when performing this.
WARNING:
Never use solvents or other harsh chemicals for cleaning the non-
metallic parts of the tool. These chemicals may weaken the plastic materials used in
these parts. Use a cloth dampened only with water and mild soap. Never let any liquid
get inside the tool; never immerse any part of the tool into a liquid.
Lubrication
D
E
WALT tools are properly lubricated at the factory and are ready for use.
Summary of Contents for D28106-XE
Page 2: ......