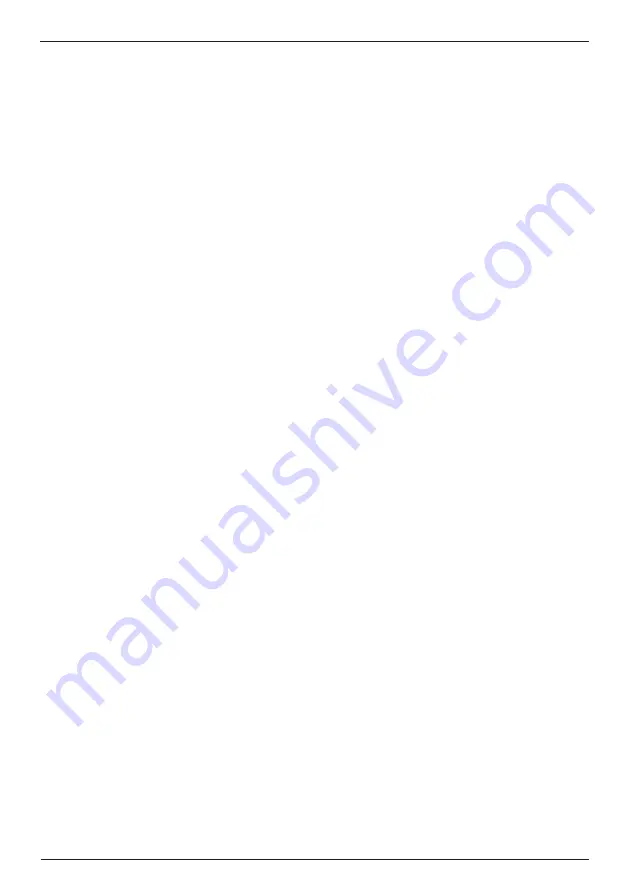
ENGLISH
6
FURTHER SAFETY INSTRUCTIONS
FOR ALL OPERATIONS
Causes and Operator Prevention
of Kickback
Kickback is a sudden reaction to a pinched or
snagged rotating wheel, backing pad, brush or
any other accessory. Pinching or snagging causes
rapid stalling of the rotating accessory which in turn
causes the uncontrolled power tool to be forced in
the direction opposite of the accessory’s rotation at
the point of the binding.
For example, if an abrasive wheel is snagged or
pinched by the workpiece, the edge of the wheel
that is entering into the pinch point can dig into the
surface of the material causing the wheel to climb
out or kick out. The wheel may either jump toward
or away from the operator, depending on direction
of the wheel’s movement at the point of pinching.
Abrasive wheels may also break under these
conditions.
Kickback is the result of power tool misuse and/or
incorrect operating procedures or conditions and
can be avoided by taking proper precautions as
given below:
a)
Maintain a firm grip on the power tool
and position your body and arm to allow
you to resist kickback forces. Always use
auxiliary handle, if provided, for maximum
control over kickback or torque reaction
during start up.
The operator can control
torque reaction or kickback forces, if proper
precautions are taken.
b)
Never place your hand near the rotating
accessory.
Accessory may kickback over your
hand.
c)
Do not position your body in the area
where power tool will move if kickback
occurs.
Kickback will propel the tool in direction
opposite to the wheel’s movement at the point
of snagging.
d)
Use special care when working corners,
sharp edges etc. Avoid bouncing and
snagging the accessory.
Corners, sharp
edges or bouncing have a tendency to snag the
rotating accessory and cause loss of control or
kickback.
e)
Do not attach a saw chain woodcarving
blade or toothed saw blade.
Such blades
create frequent kickback and loss of control.
Safety Warnings Specific for
Grinding and Abrasive Cutting-Off
Operations
a)
Use only wheel types that are
recommended for your power tool and the
specific guard designed for the selected
wheel.
Wheels for which the power tool was
not designed cannot be adequately guarded
and are unsafe.
b)
The grinding surface of centre depressed
wheels must be mounted below the plane
of the guard lip
. An improperly mounted wheel
that projects through the plane of the guard lip
cannot be adequately protected.
c)
The guard must be securely attached
to the power tool and positioned for
maximum safety, so the least amount of
wheel is exposed towards the operator.
The
guard helps to protect the operator from broken
wheel fragments, accidental contact with wheel
and sparks that could ignite clothing.
d)
Wheels must be used only for
recommended applications. For example:
do not grind with the side of cut-off wheel.
Abrasive cut-off wheels are intended for
peripheral grinding, side forces applied to these
wheels may cause them to shatter.
e)
Always use undamaged wheel flanges
that are of correct size and shape for your
selected wheel.
Proper wheel flanges support
the wheel thus reducing the possibility of wheel
breakage. Flanges for cut-off wheels may be
different from grinding wheel flanges.
f)
Do not use worn down wheels from larger
power tools.
Wheel intended for larger power
tool is not suitable for the higher speed of a
smaller tool and may burst.
Additional Safety Warnings Specific
for Abrasive Cutting-Off Operations
a)
Do not “jam” the cut-off wheel or apply
excessive pressure. Do not attempt
to make an excessive depth of cut.
Overstressing the wheel increases the loading
and susceptibility to twisting or binding of the
wheel in the cut and the possibility of kickback
or wheel breakage.
b)
Do not position your body in line with and
behind the rotating wheel.
When the wheel,
at the point of operations, is moving away from
your body, the possible kickback may propel the
spinning wheel and the power tool directly at
you.
Summary of Contents for D28413
Page 1: ...DWE492 DWE493 D28413 ...
Page 2: ...2 Copyright DeWALT English original instructions 3 ...
Page 3: ...1 Figure 1 Figure 3 X M Figure 2 A B E C G ...
Page 4: ...2 K K I L K O O P P F F J J a b J F F Figure 4 Figure 5 Figure 6 ...
Page 17: ......
Page 18: ......
Page 19: ......
Page 20: ...N485047 201608 ...