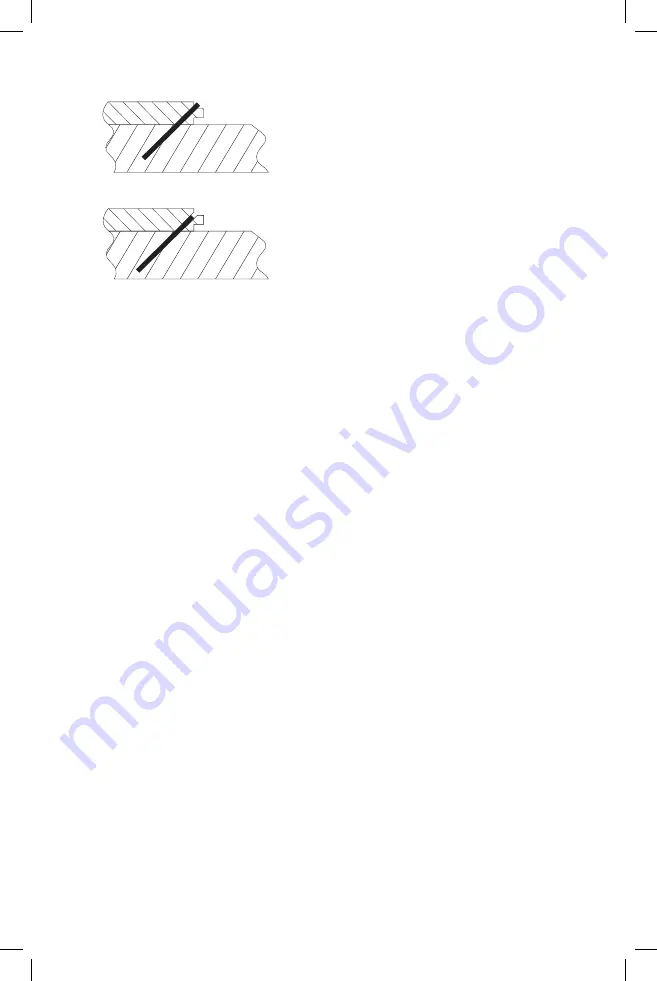
English
6
Maintenance
Cleaning
WARNING:
Blow dirt and dust out of all air vents with
clean, dry air at least once a week. To minimize the risk
of eye injury, always wear ANSI Z87.1 approved eye
protection when performing this.
WARNING:
Never use solvents or other harsh
chemicals for cleaning the non-metallic parts of
the tool. These chemicals may weaken the plastic
materials used in these parts. Use a cloth dampened
only with water and mild soap. Never let any liquid
get inside the tool; never immerse any part of the tool
into a liquid.
Replacement Parts
D
e
WALT
replacement parts are recommended. Do not
use modified parts or parts which will not give equivalent
performance to the original equipment.
To Replace Piston
1. Insert the flats on the lower end of the driver piston
stem carefully into the end of piston and plunger
wrench, BC1009.
2. Using another special wrench, BC1009, or another
wrench of the proper size, unscrew the plunger from
the upper end of the stem. After this is done, it will be
possible to lift the poppet off the stem.
3. Place the special wrench, BC1009, down over the piston
stem onto the driver piston, locking the piston ears
in the slots in the wrench. Unscrew the piston from
the stem.
To Replace Driver
1. It is not necessary to disassemble the piston-poppet-
driver assembly to replace the driver. Pull the poppet up
on the driver piston stem as far as it will go.
2. Insert special wrench, BC1009, over the driver piston,
locking the piston ears in the slots in the wrench.
Unscrew the piston from threaded portion of the stem.
3. To remove the driver blade from the piston stem, push
the driver blade pin out of the stem. This will release
the blade.
4. Insert new driver blade into the slot in the end of the
driver piston stem and assemble the driver blade pin.
Test the side play in the driver blade by grasping the
driver piston stem in one hand and the blade in the
other and moving the blade sideways in alignment with
the slot in the stem. There should be a small amount of
side play in the blade. This is necessary to take care of
any slight misalignment between the blade and guide
in the nose. If there is no side play, the blade should
be removed and the top (pin end) just barely dressed
off with a stone. It is not necessary to do more than
smooth off the top to get the necessary side play. Do
not grind. Reinsert the blade and pin in the stem and
test for side play once more. Repeat as necessary to get
this small amount of side play. Carefully examine the
large threaded portion of the piston stem. A nylon lock
can be seen imbedded in a recessed hole in the stem.
It is very important that this nylon lock can be replaced
when its locking efficiency has been reduced through
several disassemblies of the piston. It is necessary to
use the sharp point of a knife, or some such instrument,
to remove this nylon lock. Insert a new one by setting
it into the recessed hole in the stem, and tapping it
gently until firmly seated. Reverse these instructions
to reassemble.
5. Assemble plunger flush with end of piston stem.
Assembly Procedure For seals
When repairing a tool, make sure the internal parts are
clean and lubricated. Use Parker “O”-LUBE or equivalent
on all “O”-rings. Coat each “O”-ring with “O”-LUBE before
assembling. Use a small amount of oil on all moving
surfaces and pivots. After reassembly add a few drops
of
D
e
WALT
Air Tool Lubricant through the air line fitting
before testing.
Air supply-Pressure And Volume
Air volume is as important as air pressure. The air volume
supplied to the tool may be inadequate because of
undersize fittings and hoses, or from the effects of dirt and
water in the system. Restricted air flow will prevent the tool
from receiving an adequate volume of air, even though the
pressure reading is high. The results will be slow operation,
misfeeds or reduced driving power. Before evaluating tool
Under Driven Fastener
Properly Driven Fastener
Fig. F
Cold Weather Operation
For cold weather operation, near and below freezing,
the moisture in the air line may freeze and prevent tool
operation. We recommend the use of winter formula air tool
lubricant or permanent antifreeze (ethylene glycol) as a cold
weather lubricant.
CAUTION:
Do not store tools in a cold weather
environment to prevent frost or ice formation on the
tools operating valves and mechanisms that could
cause tool failure.
nOTE:
Some commercial air line drying liquids are harmful
to “O”-rings and seals – do not use these low temperature
air dryers without checking compatibility.