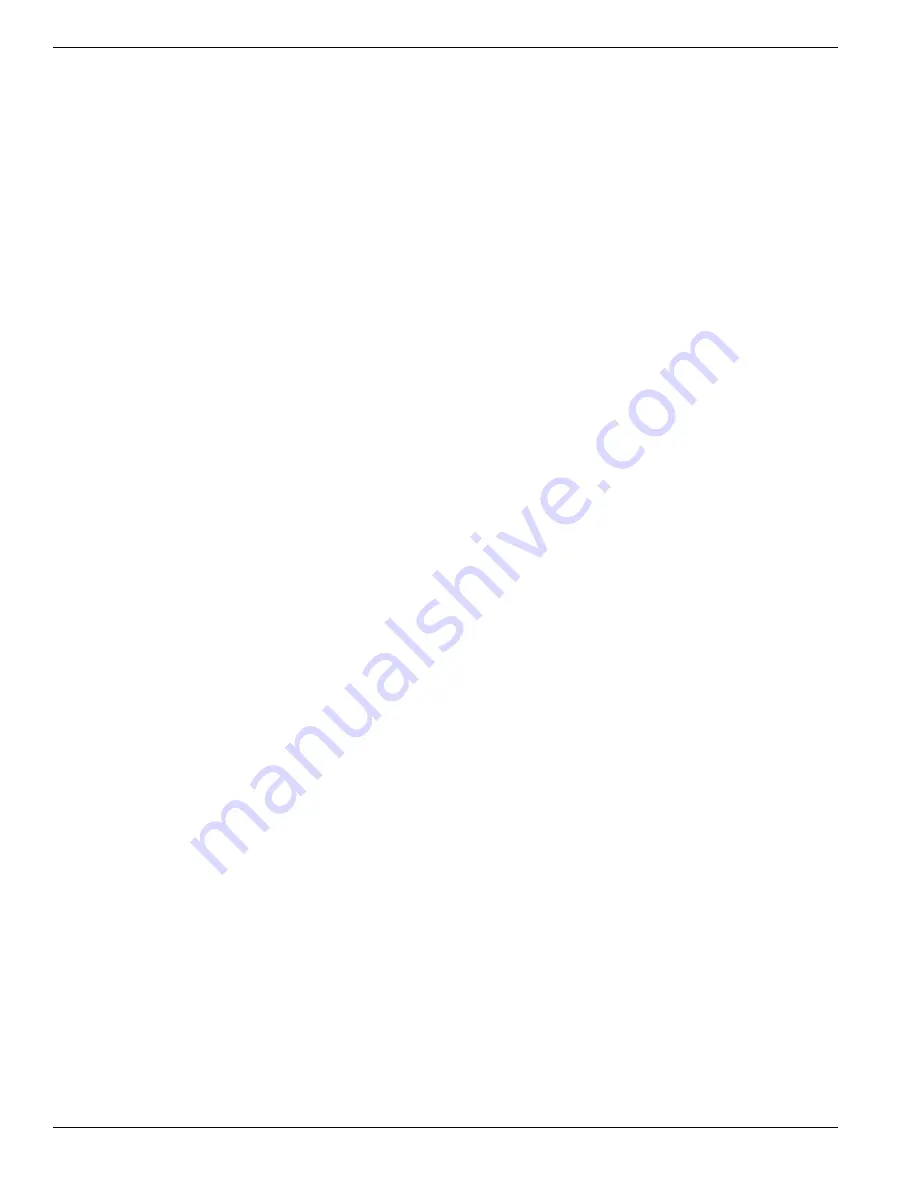
Section 3 Engine Diagnostic Tests
36
Diagnostic Repair Manual
throttle and, with a pair of pliers, rotate
GOVERNOR SHAFT fully clockwise (CW).
Use minimum amount of force against
governor shaft.
b. While holding GOVERNOR SHAFT fully
clockwise and the GOVERNOR LEVER at
wide open throttle, tighten GOVERNOR
CLAMP BOLT to 70 inch-pounds (8 Nm).
3.
Start engine. Let stabilize and warm up at no-load.
4.
Turn ADJUSTER NUT to obtain frequency reading
of 62 Hertz.
5.
Determine if GOVERNOR SPRING is properly
located in slot of GOVERNOR LEVER (Figure 48).
6.
After repositioning SPRING on LEVER slot, check
frequency reading and, if necessary, adjust
ADJUSTER NUT to obtain 62 Hertz at no-load.
7.
When frequency is correct at no-load, check AC
voltage reading. If voltage is incorrect, the voltage
regulator may require adjustment. See Test 12,
“ADJUST VOLTAGE REGULATOR”.
Test 31 – Check Oil Pressure Switch
(if equipped)
If engine cranks and starts, then shuts down almost
immediately, check the following:
•
Low engine oil level.
•
Low oil pressure.
•
Defective oil pressure switch.
Procedure
1.
Check engine crankcase oil level.
a. Check engine oil level.
b. If necessary, add recommended oil to dipstick
FULL mark. DO NOT OVERFILL ABOVE
FULL MARK.
2.
Do the following:
a. Disconnect wires from oil pressure switch
terminals. Remove switch and install an oil
pressure gauge.
b. Start engine while observing oil pressure
reading on gauge.
c. Note oil pressure.
(1) Normal oil pressure is approximately 50
psi or higher with engine running. If normal
oil pressure is indicated, go to Step 4 of
this test.
(2) If oil pressure is below about 10 psi, shut
engine down immediately. A problem
exists in engine lubrication system.
NOTE:
The oil pressure switch is rated at 10 psi for
single cylinder engines.
3.
Remove oil pressure gauge and install oil pressure
switch.
a. Set a DMM to measure resistance.
b. Connect meter test leads across switch
terminals. With engine shut down, the meter
should read CONTINUITY.
c. Crank and start engine. The meter should read
INFINITY.
d. Connect one test lead to Wire 0 (disconnected
from LOP). Connect the other test lead to a
clean frame ground. Continuity should be
measured. If continuity is NOT measured
repair or replace Wire 0 between the LOP and
the ground terminal connection on engine
mount.
4.
If LOP switch tests good in Step 3 and oil pressure
is good in Step 2 but unit still shuts down with a
LOP fault, check all wiring connections between
START-STOP-RUN switch and LOP pressure
module and LOP sender for a short to ground. Any
ground on this wire will cause the oil pressure wire
to receive a ground, also inhibiting spark from
occurring. If a short to ground is found, replace
wire.
Results
1.
If LOP switch, oil pressure, and wiring all test good,
refer to flow chart.
2.
If LOP switch failed, replace switch.
3.
If no pressure was measured, an internal failure of
oil pump may have occurred.
Test 32 – Check Oil Level Switch (if
equipped)
General Theory
Some engines utilizes a splash type lubrication system.
The switch should be open when the engine is filled with
oil. The switch will close when the oil level drops too low.
The switch will close and ground out the magnetos
inhibiting spark until the oil level is raised.
Procedure
1.
Verify the oil level is full.
2.
Unplug wire from oil level switch (Figure 55).
3.
Set DMM to measure resistance.
4.
Connect one meter test lead to disconnected wire
from oil level switch. Connect the other meter test
lead to frame ground. INFINITY should be
measured.
Results
1.
A CONTINUITY reading indicates the switch is not
functioning. Replace switch.